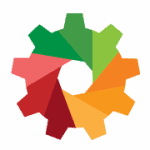
The manufacturing sector has seen a rise in competitiveness because of the introduction of Industry 4.0 technologies over the last decade. It has become important for manufacturers to stand out in the industry by optimizing their systems to be as perfect as possible. One of the factors that make a factory competitive is its reliability, and a smart factory has great opportunities to improve it using the failure data from its assets.
The smart factories created using these technologies have greater efficiency and provide valuable data about the assets which can be used to further improve plant performance. The asset failure data gathered from different assets can provide insights into the reliability of assets and how to improve it.
Collecting Failure Data
The first step towards becoming a reliability pro is collecting failure data from your production system. Since reliability is based on failures over a period of time, the failure data has to be collected regularly. Moreover, the failures occur due to various reasons at irregular intervals.
Modern digital factories have made it really easy to collect large amounts of data in real-time using sensors and IIoT. Manual data collection can be minimized when you have an integrated CMMS. However, it is important to make sure all the information about a failure is recorded, including any information the sensors can’t detect.
For example, a CNC servo motor failure may occur due to overheating or lack of cleanliness. Some parts fail in different modes under different conditions. Such details might not be detectable by sensors and may require manual entry. Accurate and complete failure history of an asset allows for a comprehensive picture of its life. This becomes important during the analysis of various reliability measures. Better data on failure also helps make better decisions about the asset’s maintenance and upgrade.
Storing Failure Data for Future Use
Once the data has been collected using the sensors and IIoT, the CMMS has to store it for future use. As mentioned before, reliability analysis can’t be done in real-time. It requires large amounts of data over long periods of time to notice patterns in failure incidents. The more good data you have, the better understanding of plant reliability you can achieve.
A good CMMS can come in handy with its own data storage solutions. There are two types of CMMS available in the market: on-premise and cloud-based.
On-premise data storage requires physical space for the data storage system of the CMMS. It allows for greater customization and scheduling of maintenance that can be aligned with the production schedule. However, the on-premise data storage system requires maintenance and human resources to operate.
On the other hand, cloud-based CMMS data storage uses cloud storage that is handled by the system manufacturer. It can be accessed through the web using the CMMS as per the requirement. The access is reliable but the maintenance schedule is determined by the CMMS manufacturer and the production schedule has to be aligned with it. Still, the requirement of no extra space and maintenance might be worth the extra scheduling work for most plants.
Analyzing Failure Data for Insights
Now that you have collected and stored the assets’ failure data, the next step is analyzing it. Analyzing failure data can help make changes to the maintenance scheduling to improve the reliability of the plant. A key part of analyzing failure data is running an FMEA (failure mode and effects analysis). Using a CMMS with failure data for FMEA can make it quicker. FMEA results can help optimize product designs and processes to increase their reliability.
Analyzing failure data and FMEA results also generates information about the reliability of assets in various measures. You can get the failure rate of an asset to see how likely it is to fail over a period of time. On the other hand, MTTF (mean time to failure) gives an idea of how long an asset is likely to perform well before a failure.
Apart from these, the analysis will calculate the availability of the asset and the production system. Availability is the percentage of scheduled operation time that the asset or system is actually available for use.
Failure data has to be analyzed regularly to stay aware of the changes in various reliability indices of the plant. The results of these analyses generate insights for maintenance, production, and management-level decisions for the plant.
Failure data of the assets in a manufacturing plant can be just as useful as production data. Harnessing the failure data, storing it and then utilizing it to get reliability information of the assets helps you make production, maintenance, and management decisions. Working on improving the reliability of parts and machines requires expertise and dedicating resources for reliability analysis in the long term.
Leave a Reply