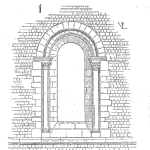
A benchmark is the end distance point from the start.
In the world of maintenance, it is the name for the targets that an organization sets for itself in an improvement program.
Benchmarking is often against world-best practice and it is used to provide direction and focus in an organization’s efforts to improve.
When RAV is chosen as the benchmark it means that the annual cost of maintaining the plant will be measured against the value of the plant.
RAV is a percentage of the cost to replace the plant. The lower the RAV the more effective the maintenance effort.
Keywords: metric, maintenance cost, percentage replacement value
The percentage of annual maintenance costs, as a proportion of replacement asset value (RAV), is becoming the universal way of benchmarking companies across a particular industry.
It involves collecting the total annual maintenance costs and then dividing the RAV into it and multiplying by 100 to give a percentage.
The RAV is, strictly speaking, the current cost to rebuild your plant today exactly as it is today.
It is the current cost to construct the plant to its present design.
This approach takes in the effect of inflation on both the project costs and the spare parts and maintenance costs.
The difficult part- how can you cost the rebuild of your plant today?
The most accurate way is to give all your design and construction drawings of the plant and facility as-it-is-today to a contractor and ask for a current price to build it.
But that is a huge job and most people don’t keep that sort of detail on their plant.
You can go to your insurer and ask them to let you use their replacement cost data for the equipment in your plant and then, asset number by asset number, give it a current cost.
But few insurers would have all the data you need.
The last option is the one most used and that is to get the as-constructed asset value from the company accountants for each asset and then increase the as- constructed cost for inflation over the intervening years since construction.
Complications with revalued assets
This is not too hard to do if you use an average annual inflation increase on all the as-constructed values.
Some complications arise if the assets have been revalued. When assets are revalued, the revalue is the monetary worth of the asset at that point in time, it is what people will pay for it and not actually what it costs.
In that case, take the as-constructed figure and multiply it by the average annual inflation rate.
Complication also arises if a lot of capital work was done on maintenance and expensed.
In that case, the asset values in the asset register are undervalued. This is not usually a major issue.
The thing with using as-constructed costs
Unfortunately using as-constructed costs does not take into effect the savings made from the introduction of new technology into the plant.
Using new and better technology means the plant can now be made for less cost. But the accountant’s books only register actual historical costs and would show a higher value than it would really need to be.
This also is not usually a problem unless your plant has had a major technological change introduced into it since construction.
Talk to the accountants in that case and come up with new asset values that they are happy with.
If you cannot get as-constructed values (the asset register should have them) then a rough way to estimate RAV is to get the total asset value for the entire plant as it is today from the accountants.
The current value allows for depreciation.
Then factor back in the average depreciation and the average inflation rates by asset number.
The accountants will have both those rates.
Looking at annual maintenance costs
The other side of the benchmarking equation is the annual maintenance costs.
How true are your maintenance costs?
If you include plant improvements, safety improvements, environmental improvements, site security improvements, small capital works and equipment modifications in the maintenance cost then you have an unreal, higher figure than the true maintenance cost for maintaining your plant.
Your benchmark result will be higher than it should be.
Maintenance costs are really the cost to repair and return an item to its as-designed function and specification – like-for- like.
Anything else is really a capital expense. But don’t argue with people over definitions, as it is not worth the stress.
Just be aware of the issue and if it clearly is affecting the figures then talk the issue and its implications through with the people at your place, and come to an acceptable decision for true maintenance costs.
If you do not collect your real maintenance costs separately to your total accounting costs then you need to introduce a CMMS (Computerised Maintenance Management System) so you know where your money is going.
Mike Sondalini – Equipment Longevity Engineer
If you found this interesting, you may like the ebook Pumping Basics.
Mike, nice article. We are just starting to look at using this type of metric at our plant and this info was very informative. Was wondering if there’s any industry benchmark levels once you have a % calculated. For example is <3% considered world class or <5%, 10%, etc….Thanks.
Hi Josh, as Mike mentions in the article the metric provides a means to compare within an industry. As far as I know these values are not commonly available. Might a good project for one of your industry-specific professional societies. cheers, Fred