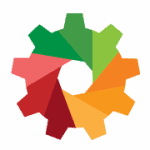
As more and more organizations seek to improve their maintenance, many are shifting from the reactive ‘repair-focused’ maintenance models to more proactive ‘reliability-focused’ maintenance which includes things like tracking, identifying, and eliminating failure, maintenance planning and scheduling, reduced downtime, reduced costs, continuous improvement, and similar.
A critical tool for making and sustaining this transition is computerized maintenance management systems (CMMS). But, a CMMS implemented in isolation or haphazardly will never deliver the desired results. For CMMS to improve maintenance – and reliability – it must address the failure modes identified in the critical systems. Therefore, the involvement of reliability engineers is vital for successful deployment of the software.
As any other tool, CMMS is only as good as the person using it. You can have the best maintenance software on the planet, but if your maintenance plan is based on guesses, unexpected failures are your one and only future.
This is why I decided to create this CMMS and Reliability series that seeks to delve into the connection between CMMS and reliability. I intend showing the supporting role CMMS can play in reliability efforts and exactly how it can aid asset reliability professionals.
Before that, let’s first use this introductory piece to take a summarized look at what I plan to write on in the upcoming months.
Bringing CMMS into the Reliability Equation
Reliability is the quality of being consistent. It is also the ability of a system or product to perform its desired function without failure under stated conditions over a specified period of time.
I will not bore everyone with additional bland definitions you already know so let’s move on.
If we start from what CMMS does, it’s easy to start building a clear connection between reliability and CMMS.
Basically, CMMS is a software that is designed to automate and simplify maintenance management. This is the most essential role of any CMMS solution. It delivers several benefits to users and gives valuable insights into their maintenance position.
Ultimately, it empowers them to make timely maintenance decisions. Such timely decisions help organizations avoid asset failure, reduce the costs of failure associated with unplanned downtime, boost overall maintenance, improve asset lifespan, and much more: all things that reliability engineers seek to achieve.
With the above in mind, this series will attempt to discuss as many topics as possible that highlight the various ways in which CMMS, directly or indirectly, improves machine reliability. The issues discussed will include:
- Eliminating/minimizing loss – tracking and managing production losses and excessively high maintenance costs.
- Safety management – tracking safety risks, minimizing safety concerns, creating safety policies and procedures and monitoring compliance.
- The connection between CMMS and FMEA – the relevance of CMMS as a tool for gathering past failure data, for equipment history, for diagnosis, etc.
- CMMS optimization – getting the full benefits of your CMMS for managing preventive and predictive plans.
- Emerging trends in CMMS – discussing possible relevance for reliability managers.
- CMMS and predictive maintenance – setting up automated failure detection.
Although it’s likely that many of you are already familiar with some of these topics, I plan to tackle them from different angles and hopefully bring new insights where even seasoned reliability professionals will able to pick up a thing or two.
Leave a Reply