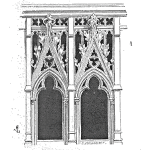
Chemical corrosion occurs at increased rates in agitated conditions.
Typical iso-corrosion curves for alloy metals no longer apply. These curves only show corrosion rates at various chemical concentrations and temperatures in stagnant conditions.
A typical curve is shown below. The curves are available from alloy metal suppliers on request.
When metals are selected for agitated corrosive conditions the curves can only be used in a relative sense.
They help grade the metal selection but they cannot provide absolute corrosion rates.
Corrosion barrier
Metals can develop a corrosion barrier when they come into contact with certain chemicals.
In some cases, this protective layer can be easily removed. Carbon steel in contact with 98% sulphuric acid forms a protective ferrous sulfate layer.
To prevent this protective layer from being removed the velocity of sulphuric acid in pipelines must be kept below 1 m/sec. Alloy steels when in contact with chemicals develop a corrosion barrier that protects the metal underneath.
In agitated conditions, this barrier is more easily removed and the fresh metal is exposed to renewed chemical attack.
The rate of protective layer removal is greatly increased in agitated conditions.
Agitated conditions include stirred vessels and tanks, mixers and agitators, pumps, pipelines, and valves.
An example of incorrect selection was with the bolts and nuts holding paddles on an agitator in a reactor mixing 50% sulphuric acid with a slurry of powder in water.
The operating temperature was 90 centigrade (195 F). The nuts and bolts installed to hold the agitator blades were wrongly chosen to be of 316 stainless steel and lasted two months.
Inspection of the iso-corrosion curve above for the process conditions indicates the unsuitability of the metal for this service.
Even a high alloy metal such as 904L would have limited life in the application.
The nuts and bolts were changed to Hastalloy C and have been in the same service for over two years.
Availability of metal
Another difficulty when selecting specialist alloys for agitated conditions is the availability of the metal in the form required, at an acceptable price.
Sometimes compromises are necessary between availability, price, and longevity. This situation can be seen with the construction of an agitator in contact with the chemicals mentioned previously.
Hastalloy C was preferred but it was only available from overseas with a long shipping delay and at a high price.
Locally 904L was available but the iso-corrosion curves indicated a limited life.
However previous experience with a similar grade alloy from a different supplier in the same service conditions indicated a life of about four years.
Because the choice of alloys was limited and repairs were required, the agitator shaft and paddles were constructed of 904L.
To date, they have been in service for over a year without obvious deterioration. Not an ideal selection but an acceptable one.
Use of the iso-corrosion curves combined with other available corrosion behavior data, such as pitting corrosion potentials, can be used to mix-and-match metals to reduce costs.
For example, a tank wall and floor in direct contact with the process chemicals may be made of a higher-grade alloy while the roof, which only sees the vapor, may be made of a lesser grade metal.
Pipeline equipment
Valves selected for corrosive services need to be designed to cope with agitated flow conditions.
Some valves cause much turbulence. Gate valves have recesses in their bodies that cause the flow to swirl in the gate pocket.
Under-and-over valves like globe valves cause the flow to twist up and around the plug and then turn back toward the outlet.
Even butterfly valves, with their disc projecting into the fluid flow cause some agitation.
When selecting valves for agitated conditions chose chemically compatible materials with wear resistance, which minimize turbulence and meet the pressure requirements of the process.
The selection of equipment in agitated corrosive conditions is difficult because both right and wrong decisions become expensive.
High grade and high-quality materials cost more and it is wasteful to specify exotic metals such as titanium if alloy steels could be used.
In contrast using materials of inadequate abilities will mean money is lost because a replacement is more frequent.
Alternate materials
In looking at better material selection for corrosive services it is useful to consider the use of non-metals.
Plastics can have excellent corrosion properties. Provided their temperature limits are respected they can be used to line the contact surfaces.
Fully Teflon lined plug valves have performed well in sulphuric acid pipelines.
Plastic lined pipes in corrosive service are common.
Corrosion resistant bricks and mortars have been successfully used as linings.
Fiberglass can be used provided the corrosion barrier layer is not worn away by abrasion.
Rubber lined valves, such as diaphragm valves, have been used for agitated corrosive conditions for decades. Rubber lined agitators have been installed into reactors.
The internals of pumps and pipes have been successfully protected with specialist epoxy coatings.
In-situ testing
Where the opportunity is available, the best method to confirm the suitability of a material is to put a test piece into the environment with which it must cope.
In the case of the 904L agitator mentioned previously, test coupons of other alloys have been welded to the agitator blades so they could undergo trial under the full service required.
If any prove to be more suitable than the 904L, the next agitator will be fabricated from that material.
Mike Sondalini – Maintenance Engineer
If you found this interesting, you may like the ebook Bulk Materials Handling Introduction.
Leave a Reply