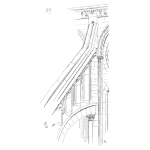
Assets or components in an operation can be dependent on each other. The network of equipment contributing to the operation output is complex and intricate. A RAM model helps account for the complexities including dependencies.
The fundamental purpose of Reliability, Availability, and Maintainability (RAM) modeling is quantifying system performance, typically in a future interval of time. A system is a collection of items whose coordinated operation leads to the output, generally a production value. The collection of items includes subsystems, components, software, human operations, etc. For example, an automobile is a system. Its sub-components being the drivetrain, engine, gearbox, etc. In RAM models, it is crucial to account for relationships or dependencies between items. This helps determine the final output of the system. In various industries, RAM models have proven to be effective as cost avoidance or decision-making tools, as well as their ability to confirm or counter stated assumptions by internal stakeholders.
What is a Dependency in a System?
Dependency refers to the quality or state of being dependent. It implies relying on someone or something for support, influence, or determination. In the case of equipment in an operating network, they rely on each other’s state of operation to work or not. If one component is down it might trigger the shutdown or start of another. Listed below are dependency types.
1. Network Dependency
For example, Diagram 1 below represents a centrifugal pump broken down into its critical components. The components are in a series configuration. The failure of any component leads to the shutdown of the entire system. Therefore, the operation of the entire system is dependent on all its components being in a functioning state.

2. Standby Dependency
Equipment that operate in a standby mode alternate between being up or down. The operating status of one unit is dependent on that of the other unit. Diagram 2 illustrates this. The system has 2 pumps placed in a parallel configuration. Only 1 pump is required to run for the system to be up. The other is on “hot” standby. If Pump 1 is operating, Pump 2 is in a hot standby mode. Hot standby means that Pump 2 is ready to start operating as soon as Pump 1 stops operating for whatever reason. This could be a failure or the need for maintenance.
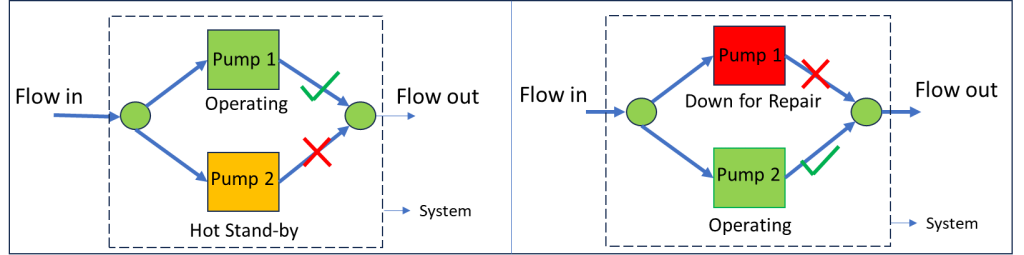
3. Deterioration Dependency
The concept of deterioration or degradation dependency is more prevalent in repairable systems.
A repairable system is expected to fail multiple times over its life. It will be restored to as close as possible to its original functional state. Failures on this system will occur more and more frequently over time. A good example of a repairable system is an automobile. Changing a failed component such as the gearbox will get the car going again, but the rest of the original components such as the engine or drivetrain will retain the same amount of wear, making the whole automobile “as good as it was just before it failed.”
The deterioration of one component is dependent on that of another. It is akin to secondary damage. For example, the deterioration of a bearing in a pump will over time, especially if left unchecked, lead to other failures such as mechanical seal or shaft damage.
In the analysis of a system it is important to account for those types of dependencies. Treating them in isolation would lead to errors in the analysis. This happens in FMEAs (Failure Modes and Effects Analysis). Dependencies are not considered in the FMEA analysis. This does not mean that the FMEA is a poor process in itself. It is on the contrary extremely useful in identifying all the correct failure modes. However once those modes are identified, their dependencies should be taken into account. A RAM model will integrate all the dependencies and correctly project the future operating performance of the asset.
Leave a Reply