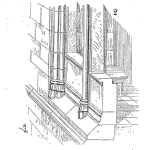
Don’t run centrifugal pumps on the end of the curve. Pumps are designed and selected to operate near their highest efficiency point.
If they operate at the right-hand end of the pump curve the likelihood of cavitation increases.
Keywords: suction pressure, flow velocity, vapor pressure, duty point.
Pump curves and what they mean
When the impellers in centrifugal pumps turn, they spin the liquid sitting in the cavities between the vanes outward.
This liquid is forced up the discharge pipe and new liquid is sucked in to replace the liquid ejected by the spinning impeller.
The amount of liquid pumped depends on:
- the diameter of the impeller
- the size and shape of the cavity between the vanes
- the size of the pump and the size of its inlet and outlet
openings - the rotational speed (RPM) of the impeller
- how much back pressure is at the pump discharge
- how much pressure is at the pump suction
- the density and viscosity (slipperiness) of the liquid
For a pump with a particular impeller running at a certain speed in a liquid, the only items on the list above that can change the amount flowing through the pump are the pressures at the pump inlet and outlet
The effect on the flow through a pump by changing the outlet pressures is graphed on a pump curve. A typical set of pump curves for a centrifugal pump is shown above.
The lines running to the right and downward are the performance curves for the pump.
They apply only to this pump running at 2900 RPM with the impeller diameters shown at the right end of each curve. At different speeds or with different impellers different curves would result. As an example of how to use the curves, assume 120 cubic meters per hour of water had to be pumped up to a tank on a 50-meter high building.
The impeller size to use in the pump is found from the curves by running a line up the page at 120M3/H. Another line is run across the page at 55 meters (allowing about 10% extra back pressure due to friction loss in the piping and valves).
The intersection point falls near the 211 mm size impeller.
The curves running up and down are the pump efficiency curves.
They indicate the pump efficiency at different operating conditions.
Pump efficiency is a measure of how much of the energy put into the pump actually goes into pumping the liquid. The duty point of 120M3/H and 55 m back pressure for the 211 mm impeller determined above is well positioned at a high efficiency.
This is a good pump selection for the duty.
What do the pump curves tell us?
The pump curves tell what flow to expect from a particular size impeller for a given amount of back-pressure on the pump.
When a pump is selected for a duty, the designer selects a pump that operates at high efficiencies on the pump curve for the impeller size. Changing the impeller width, the impeller diameter or the angle of the vanes in the impeller alters the impeller curve characteristics.
A wider impeller scoops more liquid and produces more flow, a larger diameter impeller flings liquid out at higher speed and so produces more pressure and changing the angle of the vanes alters the shape and steepness of the pump curve.
The pump curves suddenly stop at the right end of each curve.
Beyond the end of the curve, the pump manufacturer is advising that the pump cannot be safely operated.
Trying to run a pump off the right end of the curve will result in pump cavitation and eventually destroy the pump.
Pump cavitation
Pump cavitation occurs when pockets of vapor enter the pump because the liquid is boiling.
As a pump tries to pull through more liquid, the pipe friction pressure loss on the suction line rises and the liquid entering the pump sees less pressure (because it was lost to friction). A vacuum starts to develop at the pump suction.
If the vacuum gets deep enough the liquid will start to boil and vaporize and the liquid passing through the pump will contain bubbles of vapor. There is a roaring sound as if the pump is pumping gravel.
This noise is the vapor bubbles imploding when the pressure increases again after the low-pressure point.
Effects of ‘running on the right’
A pump operating off the right of the curve is cavitating.
The suction and discharge pressures fluctuate wildly pulling and pushing the impeller about because of the out-of-balance forces.
The shaft rattles; mechanical seals are damaged; packing is worn; bearings are destroyed by brinelling (hammering) and shafts are bent. Pumps will be noisy, vibrate and shake, get hot and the microjets of liquid ejected by imploding bubbles will hit and erode the impeller metal.
Consequently, the pump will fail often and need a lot of maintenance.
Some possible reasons why a pump may be running off the right side of the curve are shown in the table below:
Incorrect head pressure calculation | The pump duty was incorrectly determined or unknown. Grabbing any pump available without doing calculations and checking the pump curve can result in this problem. |
Additional tankage was added and the suction line extended | A longer suction line has more pipe wall friction pressure loss so lowering the pressure available at the pump suction. |
Blocked suction line. | Blocked strainers and closed valves are examples |
Suction pipeline Friction losses not allowed for. | Pressure loss occurs at every valve, every elbow and tee, every projection into the flow and along every millimeter of pipe. |
Broken discharge pipeline or discharge bypass valve opened. | Once the back pressure is lowered a higher flow occurs which forces the duty point to the right of the original operating point. |
Removing valves, tanks, and pipes from the pump delivery line. | Reducing the back-pressure on a pump causes the flow through the pump to rise. The duty point moves to the right of the original point. |
An old pump is moved to a new duty. | To keep capital costs down old pumps are often reused. If the pump is oversized it will operate on the right side of its original design duty point. |
Change in the process conditions. | Often a new product will be put through an existing pump. This product may have different properties and so will behave differently. |
Correcting the situation
To solve the problems caused by pumps running off the right side of the curve it is necessary to ensure the pump suction pressure is above the pressure at which the liquid vaporizes (boils).
The list below indicates ways to maintain suction pressure:
Use larger diameter suction pipelines | A larger diameter pipe has less pipe wall friction loss because the flow velocity is lower. |
Pressurize the suction side. | The suction pressure can be increased by keeping a higher level in the tank, by moving the tank higher and by lowering the pump. |
Put more back- pressure on the pump discharge. | Partially closing a valve on the pump discharge will increase the back-pressure and force the pump to operate further up on the left of the pump curve. |
Install inducers to reduce suction loss. | These are long helical screws (like a feed screw on an auger) which fit up the suction pipe and spin with the impeller. They scavenge the liquid and draw it through by force. |
Stop unnecessary pressure losses. | Maintain free-flowing suction line conditions. Clear blockages, use smooth bore pipes and long radius elbows. |
Change to a slower, larger pump impeller | Change the pump size to one that delivers the same flow and pressure but at a slower speed. This usually also requires suction piping changes. |
Keep the process liquid cool | Keep the liquid as cool as possible to increase the temperature range to the boiling point temperature. |
Slow the impeller speed. | Slowing the pump down reduces the flow rate of the liquid and lessens the pipe friction losses. Pumping takes longer and the head pressure falls. |
Let the pump manufacturer know the range of duties required. | The manufacturer can make changes to the pump such as using harder impeller material, bigger bearings and changing the impeller shape to improve operation under cavitation conditions. |
Mike Sondalini – Maintenance Engineer
DISCLAIMER: Because the authors, publisher, and resellers do not know the context in which the information presented in the articles is to be used, they accept no responsibility for the consequences of using the information.
If you found this interesting, you may like the ebook Centrifugal Pump Problems & Answers.
I’ve always wondered how centrifugal pumps work, and what effected their efficacy. I wonder why people would try to run them on anything other than the predetermined optimal settings. I think factory recommendations like that are there for a reason.
I suspect you would not be surprised how some will use equipment inappropriately rather than purchase the right solution. To save a few hours or dollars, they will likely end up spending more later to get it right. cheers, Fred
Thank you for sharing this thorough explanation of pump performance curves, as well as the trouble shooting tips and suggestions. Up-time is critical for certain OEM pump applications.
Thanks for sharing this useful info.
Just to add, a proper review of the pump performance curve is always recommended. I have gone through few examples where the pump supplier would recommend whats available on the shelf.
good advice Ayaz
thanks for the comment.
Cheers,
Fred
Excellent article. Thank you. I have a question about runout. Do you have any data on how long pumps ususally function before pump failure occurs in a runout condition? I know we shouldn’t operate here but I’m interested in failures.
HELLO
thank you for this explication;
I have a question: What if you are on the far left of your curve, or near a dead head situation, or not even on the curve? What is happening to the pump/impeller?
In your curve attached:
What if you had a pump with a 180mm impeller but your system has 46ft of head? That point does not even exist on the curve. Of course the pump is sized wrong, but it is moving some water correct?
Thanks
If the deadhead pressure of the pump (i.e. at zero flow but maximum pressure) with a 180mm impeller is below 46ft of head pressure, the pump will turn but it will not be pumping liquid. There can only be flow once the pressure pushing the liquid gets above the pressure stopping the liquid from flowing. When you start the motor it will turn the impeller but if the pump curve says the delivered pressure will never reach 46ft of head then eventually the spinning impeller is just going to boil the water in the volute. – response provided by Mike Sondalini (provided to me via email)
Hai Sir, wonderful explanation. I was searching for how to face such a problem. Now I may raise my problem sir. will you pls. look in to this.
I have four nos of centrifugal pumps using to pump sewege water , means it is in sump, immersed in water. this pumps are of 35 meter head. recently we reduced the head approximately 6 meter and pumping to ground water pipes, which is flowing by gravity.
After one year my pumps are break down one by one ,winding defective, seal damaged bearing damage etc…. How can I solve this problem.
WITH REGARDS
Hi David,
By reducing head by 6 m, you probably surpassed right end of curve. Writer mentioned above that end of curve operation frequently result in seal damage, shaft damage. Also due to higher power pulling by pump resulted in burning windings
With a submersed pump there is positive pressure at the inlet and no suction pipe to hinder flow. If the discharge head is very low compared to the pump design (off the right of the pump curve) can you not cavitate but over amp and burn out the motor anyway? Think of it this way… Ek=1/2 x mV^2. If there is low back pressure you pump more water and therefore do more work (more mass and higher velocity at the discharge manifold). More work means more power (watts) – means more amps for given voltage.
My specific example, the pump is at the bottom of a tank 5 feet deep. It discharges and spills the water over the wall of the tank 1 foot above the surface of the water. Suction pressure = 5ft. Lift = 6ft. Pipe loss is negligible. Total head = 1ft. The efficient range of the pump curve is 100 to 150 ft of back pressure. The It pumped lots of water for a while and them burned out and I wonder if my science described above is correct.
I am also curious about this in a similar context.
I currently have a pond fountain in my backyard that is essentially just a deep well submersible pump suspended from a float/buoy with a diffuser plate on the discharge. The pump suction is about 1 – 1.5 ft below the pond surface, and the discharge is just above the surface, so basically no back-pressure except for the restriction from the diffuser plate.
The motor / pump currently runs, but only for awhile (anywhere from 1-4 hours) before making some groaning noises and then quitting. It still makes some faint noises after quitting. It doesn’t kick the breaker on the panel. If I unplug and leave it for awhile, I can plug it back in and it will run for awhile again.
Can’t figure out what’s happening. I imagine that this pump is operating way over on the left of the curve as it likely has a reasonably high NPSHR. Any thoughts??
Thanks in advance!
There isn’t enough info here to give you a definite answer. You would need to know the back pressure developed by the diffuser plate to know where the pump is running on the curve. You would also need to have a pump curve (or failing that make and model).
It is possible that the pump is operating at one end of the curve or the other. My best guess is it would be operating at the far right of the curve and that cavitation is a possibility. To address this you would need to add additional backpressure.
Something else you might want to consider (assuming it is a submersible well pump) is a flow sleeve for the motor. You want to force cooling water over the motor. If you don’t have this the motor can overheat and will likely fail prematurely.
Something else not mentioned it’s the distance from power source to the motor. You should check the wire size to make sure it meets the manufacturers recommendations. A wire that is too small can cause the motor to overheat.
I am designing a submersible sewage pump station project. The project’s phase -1 has already been designed. The designed arrangement has three parallel pumps each having capacity 400 M³/Hr @ 58 Meter Head. Thus the total capacity was 800 M³/Hr @ 58 Meter.
Now as a part of expansion, we want to get total flow 1300 M³/Hr @ 65-meter Head, for this we are adding two pumps each having capacity 700 M3/Hr and 600 M³/Hr @ 65 Meter.
All the pumps will have common discharge header.
Please advise, if this parallel combination having two different flows & heads is feasible and will have safe pumping operations. What will be its effect on performance and system curves?
If you are designing a two pump parallel system from scratch it always best to have identical pumps. This way one pump is not doing more work than the other and the larger pump is not overpowering the smaller one. You can also easily alternate the pumps to keep the wear even.
If you are running two pumps in parallel you will want to make sure you are getting 1300 M./Hr. when running on the system curve. Adding the two pump flows won’t necessarily provide the flow rate you require on the system curve.
Thank you for the Wonderful article. I have a question:
How does the characteris curve of a centrifugal pump change with the decrease in temperature provided that the power at pump shaft remains constant (say 200 W).
I have a centirifugal pump attached in a closed loop for cooling purpose. The normal operation temperature is 25°C but the temperature can go as low as -30°C where the density of fluid would increase by a factor of 1.1 and the viscosuty would increase by a factor of 3 to 4. I have system curve at different temperatures but I don’t have pump curve at different temperatures (only at 25°C) to determine the operating point.
A reference material to read would of great help.
Thank you
sir ,
I am facing a problem for vertical multistage (6 stage ) barrel pump, The pump is very old more than 35 years (David brown ) 12*6*20B-D.DB50.pumping fluid is crude oil. differential head-441.9m,capacity 908.4m3/h ,discharge pressure 3930 KPA G. The problem is very high vibration at high flow in motor non drive end , and continuous seal failure. Pump is running some times more than 7000 BPH and some times in reduced flow at 4500 BPH. Another thing is discharge is divded to two side and the flow is controlled by different valves
i need your support to analyze the issue of why vibration in high flow and seal failure occurs.
thanks and waiting for your reply
Hi Sumesh, I got an email from Mike with a suggestion:
“suggest they get a vibration analyst in to diagnose the motor vibration frequencies to identify what is contributing to the high bearing vibration at high flow rates.”
cheers,
Fred