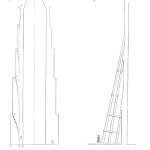
In the world of reliability engineering, ensuring the long-term dependability and safety of components is of paramount importance. Nondestructive Testing (NDT) technologies have emerged as indispensable tools for reliability professionals in various industries, including aerospace, automotive, manufacturing, and power generation. By enabling the inspection and evaluation of materials and components without causing damage, NDT techniques play a crucial role in enhancing short and long-term reliability.
In this blog post, we will explore several NDT technologies and how they contribute to improving component reliability.
Liquid Penetrant Testing (PT):
Liquid Penetrant Testing is an inexpensive and widely applicable NDT technique that helps identify surface-breaking defects in various materials. Engineering professionals rely on PT to locate fine cracks, porosity, and other surface anomalies that might otherwise go undetected. By detecting these defects early, manufacturers can mitigate the risk of component failure and extend the service life of critical parts. The versatility and cost-effectiveness of PT make it an essential tool for ensuring product quality and longevity.
Ultrasonic Testing (UT):
Ultrasonic Testing is a powerful NDT technique that uses high-frequency sound waves to inspect materials for internal defects. Reliability engineers often employ UT to identify cracks, voids, inclusions, and other flaws that might compromise the structural integrity of components. By detecting these defects at an early stage, engineers can take corrective actions to prevent catastrophic failures in the future. UT’s capability to evaluate the size, depth, and orientation of defects enhances the accuracy of defect characterization, ensuring the components meet stringent reliability standards.
Magnetic Particle Testing (MT):
Magnetic Particle Testing is a widely used NDT method for detecting surface and near-surface defects in ferromagnetic materials such as iron, nickel, and cobalt based alloys. Reliability professionals find MT particularly effective in identifying surface cracks and discontinuities. By employing MT during the manufacturing process, engineers can ensure that critical components, such as forgings and welds, are free from surface flaws that could lead to premature failure. Detecting defects early in the manufacturing process can prevent costly and potentially dangerous consequences down the line, making MT an asset for improving the reliability of manufactured components.
Eddy Current Testing (ECT):
Eddy Current Testing is a valuable NDT method used to inspect conductive materials for surface and near-surface defects. Reliability engineers often turn to ECT for detecting corrosion, cracks, and material thickness variations in critical components. The ability to perform non-contact inspections and identify defects without the need for extensive surface preparation makes ECT an efficient and time-saving tool. By detecting defects at an early stage, engineers can implement timely maintenance and repair measures, enhancing the overall reliability of components.
Radiographic Testing (RT):
Radiographic Testing is a powerful NDT method that uses X-rays or gamma rays to inspect internal structures of components. Reliability professionals rely on RT to identify volumetric defects such as voids, inclusions, and improper bonding in materials. The detailed imaging capabilities of RT provide a comprehensive assessment of the component’s internal integrity, offering valuable insights for reliability assessment. Detecting and addressing internal defects early in the manufacturing process can prevent costly recalls or replacements and improve the long-term reliability of components.
Nondestructive Testing technologies are essential tools in the arsenal of reliability engineering professionals seeking to improve the short and long-term reliability of the components they manufacture. By enabling early detection and characterization of defects, these NDT methods play a crucial role in preventing catastrophic failures, optimizing maintenance strategies, and enhancing the overall dependability of critical components. From Ultrasonic Testing to Magnetic Particle Testing and beyond, each NDT technique brings unique capabilities that contribute to a safer and more reliable future for various industries.
Leave a Reply