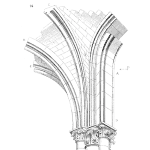
Equipment risk is a reality of every oil or gas well completion, but is this risk the exclusive responsibility of the equipment manufacturer (OEM)? To answer this question, let’s examine the major aspects of equipment risk in more detail.
Performance. Validation to industry standards such as API 11D1 and 19AC can mitigate most performance risks, but not all. Equipment performance is only as good as the OEM’s design, manufacturing, and Quality Assurance (QA) processes. The OEM owns this risk.
Interfaces. Interface problems can bring the completion process to a halt at the wellsite. Even if all equipment is supplied by the same OEM, interfaces must be verified prior to wellsite delivery. The OEM owns most of this risk.
Installation. OEMs provide installation recommendations, but most equipment is designed for a variety of applications, and generic recommendations are the norm. Enhancements are usually required for individual well conditions.
The OEM and operator share this risk.
Service Life. Service life estimates are based on material and configuration stability. OEMs estimate these stabilities using the application and environmental data provided by the operator. If either change, service life may be reduced. Therefore, the OEM and operator share this risk.
Survivability. Laboratory testing can assess some aspects of survivability but cannot simulate wellbore tortuosity. A tortuous well path can damage equipment, which can lead to premature actuation. Wellbore geometric modelling software can help mitigate this, but survivability is still proven by installing the completion equipment. Therefore, the operator owns most of this risk.
TRUTH #1: OEMs and operators share equipment risk in completions.
TRUTH #2: Equipment risk must be minimized to maximize equipment reliability.
This is the 2nd in a series of five articles on risk and reliability in downhole applications.
Leave a Reply