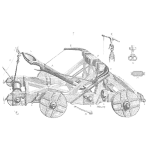
High reliability is expected of mature products with track records (low hazard rate). But new products with little or no track record (hazard rate = ?) are commercialized every day in the upstream industry. The technical objectives for new equipment always consist of performance targets, but should also include designing to maximize reliability. So, how does an OEM achieve this? The answer involves culture, capabilities, and best practices.
OEM Culture. Equipment reliability begins with rigorous QA and DfR programs (see Quality and Reliability in Oilfield Equipment). A Failure Reporting and Corrective Action System (FRACAS) should also be used to track installed reliability. All are used by OEMs that value high reliability.
Configuration stability. Equipment reliability is largely determined by configuration (see Design Assurance). A mature configuration is stable and has a consistent response to inputs. New configurations can require sophisticated modelling, analysis, and lab testing to prove stability. OEMs that value high reliability have these capabilities.
Materials stability. Stable materials experience no more than the predicted deterioration in the service environment. Unstable materials deteriorate to the point of compromising configuration. Materials stability and service life modelling are capabilities of OEMs that value high reliability.
Operation within specification (OWS). Reliability estimates are based on OWS, which means using equipment within OEM recommended limits. Casing sizes, and tension, pressure, and temperature ranges, are examples of recommended limits. Ignoring them may result in product failure. An OEM that values high reliability conducts thorough testing to define OWS and discover product limitations.
TRUTH: Culture, capabilities, and best practices lead to high equipment reliability.
This is the 3rd in a series of five articles on risk and reliability in downhole applications.
Leave a Reply