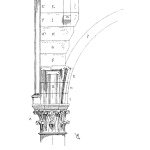
When a product is said to be of “high quality”, it is usually perceived to be reliable. Conversely, if the product is said to be “reliable”, it is probably perceived it to be of high quality. Why is this?
A product is an assembly of many components, all of which must be manufactured to some quality standard. Quality in component manufacturing is achieved through rigor in the manufacturer’s Quality Assurance (QA) system. QA systems define the Quality Control (QC) processes which ensure that materials, components, and assemblies meet the quality standard. The rigor must be appropriate for the product’s application. In critical applications (e.g. for sub-surface safety valves), the rigor must be high.
QC processes therefore ensure that manufacturing can deliver components that meet the quality standard and comply with engineering requirements, regardless of whether product design is excellent or poor.
TRUTH: Manufacturing quality is only part of the story. The rest is design reliability.
Will the finished product perform reliably? For a product to function with the highest possible reliability, its materials and configuration must be stable over its service life, i.e. design risk must be low.
However, completion equipment tends to highly customized, have a long service life, and be developed within compressed schedules. But even within compressed schedules, design risk management must occur.
TRUTH: Design risk management begins with a Design for Reliability (DfR) program.
A DfR program enables the development of completion equipment with an appropriate level of rigor and design risk management. So, the answer to the question posed at the beginning of this article is simply this – the combination of a rigorous QA program and a DfR program ensures reliable product performance over service life.
This is the 1st in a series of five articles on risk and reliability in downhole applications.
Leave a Reply