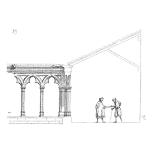
I used to be on Facebook many years ago in an effort to keep up with old friends. However, I began to realize the forum was often used to create an illusion that someone wanted their community to have about them. I knew many of these people creating such illusions, that is how I know they were ‘illusions’. Their ‘Facebook Family’ simply was not their reality.
This is not a paper about the pro’s and con’s of social media forums such as Facebook, but more about our propensity to create illusions, or prisms in which we want others to view our work initiatives. While I could apply this concept to many personal and business situations, I’m going to limit it to our general views of Reliability, Maintenance and to a degree Safety (as a by-product of effective Maintenance and Reliability).
What is the purpose of creating such an illusion? Does spending more money, make us more profitable? Does doing more tasks make us more productive? Will spending more money and doing more tasks make us safer?
Throughout this paper I will cite a couple of recent reports and surveys from the Maintenance and Reliability communities, that prompted me to write this paper. As I read them both and their conclusions, I found them to be applicable to either the Maintenance and/or the Reliability spaces, based on my experience. As you read through this, let me know if you draw the same conclusions or not!
Creating the Illusion
We’ve all seen it on such apps where people post about their perfect lives, their vacations, accomplishments, beautiful homes, giving personalities and on-and-on (see Figure 1). But many of us know these types of families and they are not perfect. This is an exaggeration, but in this model nuclear family, mom is maxing out her credit cards, dad is embezzling monies from the company, Billy is a bully at school and young Madison is normal despite the influences of her family. This is the reality and not the illusion we often want people to think about us. Let’s take this concept out of our personal social media lives and apply it to our working lives.

What Is Reliability?
Let’s start with the obvious, What is Reliability? As usual, it’s never that easy to come up with a universally acceptable definition for such a term (much like doing the same for ‘RCA’). So, I will cite one of the more common definitions I hear about and propose an alternative for the sake of simplicity. The American Society of Quality (ASQ) defines Reliability as:
“Reliability[i] is defined as the probability that a product, system, or service will perform its intended function adequately for a specified period of time, or will operate in a defined environment without failure.”
There are many other definitions, but they are similar in construct to this one.
In a recent Economics of Reliability[ii] Report released by Pinnacle, the definition of Reliability they use is simply:
“Reliability is a measure of how often something performs when you want it to”.
To measure something, there has to be a constant in which to establish a baseline. So, no matter what definition you use, ensure there is clarity in what that definition means (encompasses), and that field performance is measurable.
Is ‘What Is Being Measured’…What Really Matters?
In a recent UpKeep survey, State of Maintenance: 2021 Top Trends[iii], according to over 1000 Maintenance and Reliability respondents, the most common KPI maintenance leaders measure is ‘Planned Maintenance’. However, the biggest concern for teams is reducing the number of unplanned breakdowns.
I’m making the bridge here that Reliability is highly dependent on consistency of operations, which is highly dependent on efficiency and effectiveness of Maintenance.
This is an interesting finding because Leadership (who defines the KPI’s) is most interested in Planned Maintenance (47%), which is a task compliance metric (see Figure 2). The assumption here is the ‘Planned Maintenance’ conducted is the most efficient and effective maintenance strategy. If it’s not, we could certainly be doing excellent maintenance on the wrong things (issues with priorities), which may not increase Reliability. Or conversely, we could be doing poor maintenance on the right things. Just because we are doing ‘maintenance’ does not make it effective of efficient for these reasons.

Ironically, those in the field closest to the work, are more concerned with getting control of the unplanned equipment breakdowns (31%) and the constant interruptions or disruptions to work (31%). To me, as a Root Cause Analysis (RCA) expert, there is certainly a correlation between these two concerns.
Constant interruptions and disruptions to our work, imposes time pressures on us. Whenever we are time-pressured, we have a tendency to take short-cuts. These shortcuts often end up surfacing as undesirable outcomes (a.k.a. – unplanned equipment breakdowns).
Normalization of Deviance: Are We Forgetting to Be Afraid?
In Figure 3 below, when we take shortcuts, we are deviating from a set standard, or our potential. Very often, when we deviate like this, nothing bad happens and we may even get a pat on the back for making up the time. When this happens, it is a logical deduction that the shortcut we took, exposed an unnecessary task. As a result, we have lowered/eroded the initial standard. This iterative process is called normalization of deviance. This is a dangerous slide away from our intended standard. The academic term for this gradual decline is called ‘drift’.
As the graphic is titled, over time, ‘we forget to be afraid’. We are comfortable with the new, lowered standards and don’t realize the gap between our initial standard and our current state, is widening. Eventually we will drift into an unsafe zone and this is where catastrophes breed.

The key to preventing drift is to ensure that our Supervisory Oversight is adequate (in the graphic, LTA = Less Than Adequate). Supervisors should be well-versed in Human Performance Improvement (HPI) principles and be able to recognize when this drift is occurring…AND STOP IT.
Unfortunately, I’ve seen way too many ‘RCA’s where a conclusion is drawn (a ROOT cause) that blames the individual for taking a shortcut, when the decision-maker, and many others have been doing so for years, with supervision knowing about it. That’s not a ‘Root Cause Analysis’, that’s a ‘Shallow Cause Analysis’. That’s also hypocrisy at its finest!
Does How Much We Spend on Reliability, Correlate to Increased Profitability?
Operators around the world spend an estimated $500B USD annually on Reliability in complex processing systems[iv]
In the cited Pinnacle report, they draw an interesting differentiation between the ‘Reliability spend’ and actual ‘Reliability performance’. In the past I have written extensively about if a direct correlation exists between Reliability and Safety. Interestingly enough, there are two schools of thought on that seemingly obvious topic, but the basic premise is that Reliability is viewed from a performance standpoint…not what we spend on Reliability. This is why this report caught my eye.
It should be noted that this Pinnacle Report is evidently the first in a series of upcoming reports. This first one focused on global refining. I predict that in subsequent reports from different industries, the inefficiencies of the ‘spend’ will be consistent with the refining report.
Here are some findings that stood out to me when reading this Report:
1. A Reliable operation is the largest correlative indicator of a profitable operation [Page 5]. [I would go one step further and say that a Reliable operation is also a large correlative indicator to a safe operation.]
2. The more money that refiners spend on Reliability, the less profitable they become [Page 33]
3. Global refiners spend over $50B annually on Reliability-focused activities. Between 10% and 30% of this spend is wasted, meaning it does not improve Reliability. Suboptimal approaches to Reliability costs refiners between $5B and $15B annually worldwide. [Page 36]
4. Companies with the most efficient Reliability spend tend to be using the most quantitative analysis processes to inform strategies. [Page 36]

This got me to thinking, Does how much we spend on Planned Maintenance (the KPI that most leadership was interested in), correlate to greater profitability? The Pinnacle Report was focused only on the Reliability spend [in global refining – Figure 4], but would the Maintenance spend in general, yield a different conclusion? Do we spend our Maintenance dollars efficiently? Could up to 1/3 of our Maintenance dollars be wasted as well?
Does How Much We Spend on Software/Technology Correlate to Improved Profitability?
While the UpKeep survey did not focus on the costs of the actual Maintenance spend, I can make the logical leap that the investment in Maintenance infrastructure (software/technology) can be significant as well. How often does that investment yield the ROI’s we would expect?
In the UpKeep survey, it was found that COVID-19 has accelerated the digital transformation for Maintenance work (Key Finding #5).
60%+ of respondents who use an Enterprise Resource Planning (ERP) system, report their software being difficult to use. Analysts have found that roughly 75% of ERP projects fail. And that is no different when it comes to Maintenance.
My takeaway from this is that no matter the spend level, the success of the execution of the software will determine its actual impact on bottom-line performance. Think of how much was/is invested globally in ERP systems, and how much a 75% failure rate impacts the bottom-line of those investors.
I think back to the days of Jack Welch and his laser focus on Six Sigma while leading GE. Essentially if you were not on board with Six Sigma, you would not be working at GE. GE had full backing and support of the CEO to make Six Sigma the priority. As a result, GE produced astounding results and the world took notice.
Many thought that Six Sigma was the greatest thing since sliced bread at that time. Hundreds of companies jumped on board and said we want similar results so we’ll implement Six Sigma as well. These companies invested billions of dollars and most of them failed. How could that be, they spent a ton of money?
In hindsight, we all learned it is not the principles of the initiative that failed, it is our implementation, execution, support systems and culture that failed to accept the principles. These other companies did not have the dedicated CEO support like Welch. They just signed fat checks and expected results. How many other such initiatives have failed because of this cycle?
I did such an impromptu analysis on RCA effectiveness years ago, by conducting an RCA on ‘Why RCA Efforts Are Not Meeting Expectations?’. What if we did an effective ‘RCA’ on why 75% of ERP projects fail, what would your experience come up with as ‘root causes’?
In the UpKeep survey 42% of respondents reported using a Computerized Maintenance Management System (CMMS) in 2019. 65% of respondents reported that they would be using a CMMS in 2021. That is a significant increase in the spend associated with such technologies. However, as stated earlier, the increase in the spend does not automatically correlate to improved profitability.

The UpKeep survey reports that McKinsey found that effective and efficient use of technology within maintenance processes, can reduce spending by 10-15%, as well as increase OEE by 2-3 percentage points (which is often millions of dollars annually). The key here is the ‘effective and efficient’ implementation of such technology.
How does your facility monitor and track the ROI for technology investment? Most capital engineering projects are subject to a corporate ROI (%) and a certain payback period. Are we aware of what those expectations are for Maintenance and Reliability technology investments?
Conclusions.
While the data sources I provide in this paper (one for Maintenance and the other for Reliability), I see a commonality in their findings.
1. Are we focusing on what truly matters? Are we only focusing on the monies spent/investments, or our we focusing on their bottom-line results (how effectively and efficiently we used those monies)?
2. We all have ‘unity in purpose’ when it comes to Reliability. Reliability = Proaction = No Surprises. Optimal Process Reliability equates to:
- Increased profitability due to 1) Optimized throughput (full-rate, 1st pass quality & steady state operations), 2) Decreased maintenance costs (due to decrease in unplanned equipment breakdowns) and 3) Decreased Process Safety incidents
3. Unplanned Breakdowns are the enemy of Reliability. Control the fix and don’t let the fix control us.
4. The Pinnacle Report suggest that in order to optimize the Reliability spend and Reliability performance to minimize risk and maximize profits, a [refinery] can do four (4) things:
- Develop consistent, quantitative systems for evaluating system performance
- Integrate Reliability data from a range of sources and assets into single system models to ensure the critical inputs and influences are identified
- Ensure personnel are adapting their work processes and utilizing these systems effectively to leverage their capabilities (optimizing the investment monies).
- Push past traditional decision processes or practices to uncover new opportunities and solutions.
5. I would add that gaining a deep understanding about how and why unplanned breakdowns occur, is a key to preventing their recurrence. This involves a leadership commitment to incorporating the social sciences into RCA efforts. This means acknowledging that blaming the decision-maker is not an appropriate conclusion to an effective RCA, but rather understanding why they felt the decision they made at the time…was the appropriate one. This usually will uncover flaws in our organizational systems that are victimizing our decision-makers. A major contribution to an effective RCA, is our ability to look in the mirror and acknowledge that we [leadership] are part of the problem, as we are responsible for our organizational systems.
6. Aspire to apply RCA proactively. There is no reason that effective RCA’s cannot be applied to chronic failures (that do not typically meet set triggers), near-misses and unacceptable risks (identified via risk analysis tools like FMEA).
I’m interested in hearing stories about whether your experience is consistent with the Pinnacle findings that we our wasting between 10% and 30% of monies spent for our Reliability efforts (and I’ll add Maintenance as well)? If so, why?
About the Author
Robert (Bob) J. Latino is CEO of Reliability Center, Inc. (RCI). RCI is a 48-year old Reliability Engineering Consulting firm specializing in Equipment, Process and Human Reliability. Bob has been facilitating RCA’s with his clientele around the world for over 36 years and has taught over 10,000 students in the PROACT® RCA methodology.
Root Cause Analysis: Improving Performance for Bottom-Line Results (5th Ed)
The PROACT® Root Cause Analysis Quick Reference Guide
Citations:
[i] What is Reliability?. https://asq.org/quality-resources/reliability. [accessed on 12.28.20]
[ii] Pinnacle Releases First Global Economics of Reliability Report for Global Refining. 2020. https://www.globenewswire.com/fr/news-release/2020/12/09/2142500/0/en/Pinnacle-Releases-First-Global-Economics-of-Reliability-Report.html. [Accessed on 12.28.20]
[iii] 2021 State of Maintenance. 2020. https://app.livestorm.co/upkeep/state-of-maintenance-2021-results. [Accessed on 12.28.20]
[iv] Pinnacle Asset Integrity Services. The Economics of Reliability: Interim Report – Global Refining. 2020.
Leave a Reply