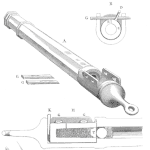
“A failure analysis is a waste of resources. We know why it failed. We need to move on.”
If you have participated in a failure analysis, you have likely heard the preceding comments, and been told to fix the problem ASAP. You make a change, but the same failure re-surfaces and you are in the hot seat again. What can you do to improve the failure analysis process in the future? Let us begin by reviewing some realities of failures.
A failure can be very costly. The costs of developing an improved product and replacing defective products add up quickly. Failure can also result in brand damage, a cost which includes lost sales and future discounts.
A failure analysis interrupts the organization. Pulling your best and brightest into the analysis puts other projects on hold, leading to opportunity cost.
As an example, consider the following scenario. An oilfield product is leaking in a customer’s well. The investigation reveals that it contains a cracked seal. The multi-disciplinary failure analysis team focuses on the cracked seal, designing and testing new versions. The team gets a new seal to pass a test. The product is put back in service, but the leak occurs again. The team’s approach indicates a Failure to Analyze.
TRUTH: A failure becomes more costly when the failure analysis is conducted poorly.
The cracked seal may be a symptom of another problem. The Failure Analysis should use a method such as the 5 Whys Root Cause Analysis, in which “why” is asked at least 5 times. Begin by asking why the failure occurred. Use the answer to this question to create the second question, and so on, until you have asked and answered at least 5 questions. For example:
- Why did the product leak? The seal cracked.
- Why did the seal crack? Because of high volumetric expansion.
- Why was volumetric expansion high? Because an incompatible fluid in the well caused excessive seal swelling.
- Why was an incompatible fluid in the well? Because the fluids program was changed at the wellsite and we were not consulted about seal compatibility.
- Why were we not consulted about seal compatibility? Because the management of change process was not used. This is the true ROOT CAUSE.
This process of asking “Why” at least 5 times identified the true root cause. Find the root cause and you know which problem to fix.
Great post! Simple and straightforward to the point Fred!
Thank you for your feedback on my article!