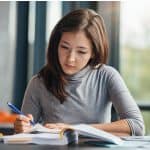
FMEA teams should agree to the ground rules that guide the analysis and the underlying assumptions that impact the entire FMEA. Failure to do so will add complexity and confusion to the resulting FMEA, and waste people’s time. Don’t miss this important step in FMEA preparation.
“Your assumptions are your windows on the world. Scrub them off every once in a while, or the light won’t come in.” Isaac Asimov
ground rule
The Oxford English Dictionary defines “ground rule” as “a basic rule about what should be done in a particular situation, event etc.”
assumption
The Merriam-Webster Dictionary defines “assumption” as “a fact or statement (as a proposition, axiom, postulate, or notion) taken for granted.”
Establishing ground rules and assumptions
Before beginning an FMEA, the team should discuss (and document) the specific ground rules for how it will be performed and the underlying assumptions of the analysis. Some of these guidelines may have been determined previously by the department’s standard practices for FMEA and some may be specific to the particular analysis project.
Ground rules are important so the team can move through the analysis in an effective manner, using the least amount of in-meeting time.
Identifying the underlying assumptions is one of the most critical steps in FMEA preparation. FMEA is about analyzing failures, and what constitutes a failure in a given analysis depends on certain assumptions, as covered below.
A Design FMEA focuses on design-related issues emphasizing how the design can be improved to ensure that product-related risk is low during the useful life of the equipment. This includes any potential failure modes and causes that can occur during the manufacturing or assembly process, which are the result of the design. The team may choose to mitigate such failure modes (for example: error-proofing, design-for-assembly, etc.), and these recommendations should be placed in the recommended actions column.
A Design FMEA usually assumes the product will be manufactured within engineering specifications. In addition, the Design FMEA team may wish to consider an exception: the part design may include a deficiency that could cause unacceptable variation in the manufacturing or assembly process.
A Process FMEA focuses on process-related issues for the manufacturing or assembly process, with emphasis on how the manufacturing process can be improved to ensure that process related risk is low. The team may identify design opportunities to eliminate or reduce the occurrence of process failure modes, and these should be placed in the recommended actions column of the PFMEA. An example is a design change that eliminates the possibility of operator misassembling a part.
Process FMEAs typically assume incoming parts and materials to an operation meet design intent. In addition, the PFMEA team may wish to consider an exception when historical data indicates incoming part quality issues: incoming parts or materials may have variation and do not necessarily meet engineering requirements.
Example of ground rules and assumptions the FMEA team may consider
- For Design FMEAs, does the FMEA team assume the product will be manufactured or assembled within engineering specifications?
- For Design FMEAs, does the FMEA team wish to consider an exception, such as the part design may include a deficiency that could cause unacceptable variation in the manufacturing or assembly process?
- For Process FMEAs, does the FMEA team assume incoming parts and materials to an operation meet design intent?
- For Process FMEAs, does the FMEA team wish to consider an exception, such as incoming parts or materials may have variation and do not necessarily meet engineering requirements?
- What are the assumed environmental conditions?
- What are the assumed operating profiles?
- Will the FMEA team assume product abuse by the user? If so, to what levels?
- What is the definition of failure used in the FMEA?
- How will the FMEA team prioritize issues for corrective actions?
- What is the process by which the FMEA team obtains approval for FMEA recommended actions and follow-up for execution?
- What meeting norms should the team adopt so that meetings run smoothly and efficiently?
- Who will enter data into the FMEA software during meetings? Will there be a scribe, or will the facilitator enter the data?
- How will the FMEA team come to decisions on each of the FMEA tasks?
- If applicable, how will the FMEA team coordinate with suppliers? Will supplier FMEAs be reviewed and approved by the FMEA team for critical parts according to defined FMEA quality objectives?
- How will the organization track the completion of recommended actions and ensure risk reduction to an acceptable level?
Ground Rules and Assumptions checklist
Click here to access a PDF copy of the FMEA Ground Rules and Assumptions Checklist. This checklist can be modified to fit the circumstances of individual FMEA teams or companies.
FMEA Tip
Ground rules and assumptions should be written down and agreed upon by the FMEA team before commencing the FMEA. They should be electronically attached to the FMEA, so there can be no question as to what assumptions the team is using throughout the analysis.
Problem
The ABC lawn mower company designs a residential mower to be able to operate safely on ground slopes up to 30 degrees without tipping over. In other words, the operating profile is anywhere between 0 and 30 degrees. However, it is possible for a customer to make a mistake and use the lawn mower on a steeper slope, say 45 degrees, and subsequently the mower can tip over with potential injury to the user. Is this “tipping over” a system failure? Should the FMEA team ignore this potential failure because it occurs outside the specified operating profile? What should be the assumption that the FMEA team makes regarding this type of potential abuse by customers?
Solution
Although products are designed for use within specified environmental conditions and operating profiles, where possible they should be safe even when there is foreseeable misuse (within limitations discussed below). In this example, if the lawn mower tips over, even when used on a slope greater than the specified 30 degrees, the mower system design can include a safety feature that stops the mower blade from spinning in order to protect the user from injury because of tipping over. The FMEA team can assume this “foreseeable misuse” and consider this failure within the scope of the FMEA.
FMEA Q&A
The important thing is not to stop questioning. – Albert Einstein
Reader question:
Our production process is running according to specifications, standards, etc., but we have a problem related to design. Because of this design problem, we could have a failure with our product. We believe a design change is needed (add material) in order to prevent the product failure. My question is this: is there something that I should introduce in P-FMEA if the failure cause is related to design? We have that failure in P-FMEA but with causes related to the process, not design. We implement a cost reduction on the product and we decrease the material quantity (the product is not affected). Also for this, should I update something in P-FMEA?
Answer:
Regarding your question about design-related problems that come up during a Process
FMEA, let me begin with assumptions. The following is from chapter 5 of my book:
A Process FMEA focuses on process-related issues for the manufacturing or assembly process, with emphasis on how the manufacturing process can be improved to ensure that process related risk is low. The team may identify design opportunities to eliminate or reduce the occurrence of process failure modes, and these should be placed in the recommended actions column of the PFMEA. An example is a design change that eliminates the possibility of operator misassembling a part.
Process FMEAs typically assume incoming parts and materials to an operation meet design intent. In addition, the PFMEA team may wish to consider an exception when historical data indicates incoming part quality issues: incoming parts or materials may have variation and do not necessarily meet engineering requirements.
For Design FMEAs, the cause is the design deficiency that results in the failure mode. For Process FMEAs, the cause is the manufacturing or assembly deficiency (or source of variation) that results in the failure mode. However, if the process team is aware that there is a design deficiency, two strategies can be used. The first strategy is to improve the manufacturing process in order to make it robust to the design deficiency. In other words, the manufacturing process is modified to be able to produce the product to specifications regardless of the design deficiency. The second strategy is to make note of the anticipated design problem and request it be addressed with a Design FMEA or other design solution.
Although this second strategy is not the usual focus of a Process FMEA, if the Process FMEA team believes the product has a design deficiency that is outside the scope of the Process FMEA, I would rather they take action to communicate the issue to the design team and request resolution, than allow the product to result in field failures.
Next Article
Once you have identified the scope of the FMEA project, made the scope visible, and identified the assumptions for the analysis, it is time identify the FMEA team members. The next article discusses the composition of the FMEA team, including why each member is needed, and the underlying reason for a cross-functional team.
Leave a Reply