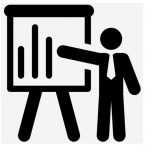
One of the more challenging aspects of FMEA is the subject of Occurrence. Part of every FMEA standard or procedure is the assessment of Occurrence based on an agreed-upon scale. Here are some pointers for when and how to use occurrence in an FMEA.
We’ll start with a definition. The Oxford English dictionary defines “occurrence” as “the fact or frequency of something happening.”
What is Occurrence in FMEA?
Excerpting from my article “Understanding FMEA Occurrence: Part 1”
“Occurrence” is a ranking number associated with the likelihood that the failure mode and its associated cause will be present in the item being analyzed. For System and Design FMEAs, the occurrence ranking considers the likelihood of occurrence during the design life of the product. For Process FMEAs the occurrence ranking considers the likelihood of occurrence during production. It is based on the criteria from the corresponding occurrence scale. The occurrence ranking has a relative meaning rather than an absolute value and is determined without regard to the severity or likelihood of detection.
There are four aspects or considerations when assessing the likelihood of occurrence. These can be challenging. We’ll cover them one by one.
Occurrence consideration 1: What is it the occurrence of?
The first occurrence topic I will discuss has to do with WHAT is occurring that is being assessed for likelihood. In Design FMEAs, occurrence is assessed for the Failure Mode due to the specific Cause. The
WHAT is the Cause of failure. The reason for this is to differentiate the risk associated with the various causes of failure modes. Merely assigning occurrence levels to failure modes misses the opportunity to differentiate risk from causes.
Occurrence consideration 2: What is the time period during which occurrence is assessed?
For Design FMEAs, most FMEA standards state that the time period for which to estimate the likelihood of occurrence is the anticipated useful life. However, this is not an entirely satisfactory range of time for certain Modes of Operation. For example, during storage mode, the FMEA team may wish to consider failure modes and associated causes that occur during the storage time period.
For Process FMEAs, the typical time period is during the production process.
Occurrence consideration 3: By what method is occurrence assessed?
The third occurrence topic is the METHOD for assessing occurrence. In my practice, I consider three inputs when assessing occurrence ratings: prevention controls, field/manufacturing history for similar items (when applicable), and degree of change.
Input 1: Prevention Controls describe how a failure mode, cause, or effect is prevented, based on actions or methods currently planned or in place. If the Prevention Controls are good, they can reduce the likelihood of occurrence.
Input 2: For similar items, field history (for Design FMEAs) or manufacturing history (for Process FMEAs), can provide useful input to the assessment for likelihood of occurrence. It is not exact, and only should be used as input to the discussion.
Input 3: The third input when assessing occurrence is the degree of design change (for Design FMEAs) or process change (for Process FMEAs). The more change there is from the previous configuration or application, the higher the risk of failure. This includes changes to design, process, environment, duty cycles, etc.
Occurrence consideration 4: Is the occurrence assessment qualitative or quantitative?
The short answer to this question is that assessing the likelihood of occurrence in an FMEA is a qualitative process.
Reference MIL-STD 1629A, section 3.1 “Qualitative approach,” which says, “Individual failure mode probabilities of occurrence should be grouped into distinct, logically defined levels, which establish the qualitative failure probability level . . .”
Reference SAE J1739:2021 section 5.4.2.1, which says, “The assessment of likelihood of occurrence for a specific cause, can be identified by the DFMEA team using a qualitative (subjective) method.”
This brings up the question of the role of objective failure rate probabilities that are sometimes used in occurrence scales. Numerical failure rates can at times be useful as qualitative guidance to focus the team discussion on one level of the occurrence scale over another. It is still a qualitative assessment.
What is purpose of occurrence in FMEA?
The purpose of assessing occurrence in Design or Process FMEA is to allow the FMEA team to consider the risk based on the likelihood that the failure mode and associated cause will be present during a specified time period. The risk of occurrence will be used along with the risk of severity and detection in order to prioritize risk.
What is a common misunderstanding about Occurrence?
For Design FMEAs, since occurrence assessment is qualitative and not objective, the occurrence rating should not be used to calculate reliability.
Next article
In the next Inside FMEA article I will take up another set of reader questions concerning Risk Prioritization in FMEAs, and which method is preferred.
Leave a Reply