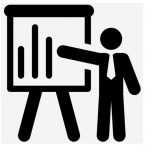
One of the most important concepts in designing for reliability is robust design. This article is a high-level overview of robust design and its relationship to FMEA.
“For the robust, an error is information.” Nassim Nicholas Taleb
What is the definition of “robust”?
The Oxford English dictionary has two connotations for the word “robust”:
1. (of an object) sturdy in construction
2. (of a system) able to withstand or overcome adverse conditions.
What is a Robust Design?
The engineering application of robust design is not merely “sturdy in construction.” Focusing on making designs sturdy, without paying attention to other parameters, such as weight and packaging, risks sub-optimizing the design. For example, if a design engineer focuses on the first connotation of the definition of robust “sturdy in construction”, the product may end up too heavy or too big. In addition, if the focus becomes merely reducing variation, such as tightening tolerances, the cost of the product can skyrocket.
The key to robust design is understanding the second connotation to the definition “(of a system) able to withstand or overcome adverse conditions.” Robust Design is a methodology to develop designs that are insensitive to anticipated variation.
What is the origin and application of Robust Design?
The following is an excerpt from a paper by faculty at Iowa State University, titled “Robust Design”:
Robust product design is a concept from the teachings of Dr. Genichi Taguchi. It is defined as reducing variation in a product without eliminating the causes of the variation. In other words, making the product or process insensitive to variation.
This variation (sometimes called noise) can come from a variety of factors and can be classified into three main types: internal variation, external variation, and unit to unit variation. Internal variation is due to deterioration such as the wear of a machine, and aging of materials. External variation is from factor relating to environmental conditions such as temperature, humidity and dust. Unit-to-unit variation is variations between parts due to variations in material, processes and equipment.
Examples of robust design include umbrella fabric that will not deteriorate when exposed to varying environments (external variation), food products that have long shelf lives (internal variation), and replacement parts that will fit properly (unit-to-unit variation). The goal of robust design is to come up with a way to make the final product consistent when the process is subject to a variety of “noise”.
Robust parameter design is used to find the appropriate control factor levels in the design to make the system less sensitive to variations in uncontrollable noise factors (i.e., to make the system robust).
What is the relationship between Robust Design and FMEA?
As covered in chapter three of Effective FMEAs:
The primary objective of an FMEA is to improve the design. For System FMEAs, the objective is to improve the design of the system. For Design FMEAs, the objective is to improve the design of the subsystem or component. For Process FMEAs, the objective is to improve the design of the manufacturing process.
The end result of FMEA should be design (or process) improvements. One of the most important types of design improvement is a robust design.
What specific ways can FMEA support Robust Designs?
There are at least two ways that FMEA can support robust designs. The first way is to perform a Parameter Diagram (P-Diagram) before beginning the System/Design FMEA. P-Diagram takes the inputs from a system and relates those inputs to desired outputs of a design that the engineer is creating, also considering non-controllable outside influences. Using P-Diagram to support FMEA is the subject of issue 182 of Reliability Hotwire eMagazine, including mapping of P-Diagram elements to FMEA.
The second way that FMEA can support robust design is by using selected action strategies to reduce risk. Risk reduction strategies are thoroughly discussed in chapter 7 of Effective FMEAs. When the FMEA team identifies risk that can be reduced by making the product design more robust, they should enter the improvement task in the Recommended Actions column of the FMEA. The action(s) can be specific design changes to make the design more robust, or can launch specific techniques that can be performed to make the design more robust.
For example, there are other methods than FMEA that support robust design. Specifically, Design of Experiments, also called Taguchi methods, is the primary technique that achieves robust design. FMEA teams can use the Recommended Actions column of their FMEA to recommend a DOE.
What is an example of using FMEA to implement Robust Design?
In this brief and fictitious example, we’ll take a further look at the hand brake subsystem of a bicycle.
A P-Diagram performed as part of the preparation for a hand brake Design FMEA reveals a “noise factor” of brake pad orientation. The friction generated by the brake pad against the wheel rim is sensitive to the orientation of the brake pad, when it is assembled in the plant or by the user.
When the FMEA team is addressing a design-related cause that has to do with the orientation of the brake pad, they can consider robust design techniques, such as DOE or product error-proofing, to make the brake pad adjustment design more robust to the “noise” of adjustment.
Excerpt from All-Terrain Hand Brake Design FMEA – Robust Design example
What resources are there for Robust Design?
The following is a shortlist of Robust Design resources.
Article in HotWire: “Taguchi Robust Design for Product Improvement”
Article in HotWire: “Taguchi Robust Design for Product Improvement: Part II”
Excerpt from book Manufacturing Processes: Integrated Product and Process Design
Presentation slides on Robust Design from MIT Sloan
Reliawiki.org article “Robust Parameter Design”
SAE International: Robust Design C1231
Quality Engineering Using Robust Design
FMEA Tips
Use the Recommended Actions column of the FMEA worksheet to launch quality and reliability tools. This is one of the keys to successful FMEAs. The FMEA team may not always be able to identify the exact engineering solution to reduce risk to an acceptable level. When this is the case, the team should recommend the tool(s) that are needed to improve the product or process design.
Next Article
One of the hot topics in the FMEA world is how to get better results with FMEAs, in less time. The next article summarizes years of experience and lessons learned on strategies to shorten FMEA in-meeting time.
Leave a Reply