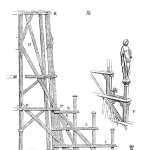
Frac plugs create a seal with the inner diameter of the casing. With the frac ball on seat in the frac plug, a check valve is formed in the casing which resists fracturing pressures up to 15,000 psi. Composite frac plugs use substantially composite components and rubber seals. Degradable frac plugs use components manufactured from magnesium (Mg) alloys.

A frac plug (FP) has three missions. The 1st is to resist fracturing pressure, the 2nd is to stay at its setting location until removed, and the 3nd is quick removal (~15 minutes). When compared to cast iron versions, composite versions are intrinsically quicker to remove. Quick removal for degradable versions means substantial deterioration within ~14 days of installation.
Most composite and degradable versions use a permanent packer configuration to achieve missions 1 and 2. Composite materials and magnesium alloys are used to achieve the removal mission. A large variety of thermoset materials are used for structural components, and both chopped fiber and continuous fiber reinforced materials are used. Some higher temperature versions use reinforced thermoplastic materials. The magnesium materials used in degradable products tend to be “designer alloys” and are highly customized to achieve strength and degradation targets.
But configuration and materials selection are only the start. It is difficult to model the response of these materials to combinations of pressure and temperature. Also, the response of components can change when manufactured at different suppliers, or when sources of resins and powders change. Thus, further de-risking through FMEA and laboratory tests is necessary to achieve high intrinsic reliability. See The Importance of Post-delivery Feedback.
High frac plug reliability is critical to unconventional completions because they ensure that expensive fracturing fluids go into the right perforations. Purchasing a plug with a claim of high reliability is a good start, but there is more to the selection process. As mentioned in The Plug and Perf Process, a frac plug is part of a system of PnP tools, the intrinsic reliability of which must be established by the OEM prior to installation. And high frac plug reliability is also possible only when wellbore cleanliness and low tortuosity are achieved. See Equipment Risk. A frac plug OEM can add reasonable debris tolerance to its product but cannot design it with tolerance for an infinite range of damaging wellbore conditions.
TRUTH: FP reliability is influenced by companion tools and the downhole environment.
This is the 2nd in a series of five articles on why Frac Plugs fail in Plug and Perf applications.
Leave a Reply