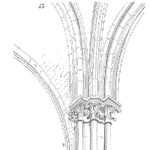
Many explosions in the processing, manufacturing and bulk materials handling industries involve flammable gases or vapours and explosive dusts or fibres. Such chemicals are known as hazardous materials. This article provides a basic overview of the design requirements for hazardous areas.
What is a Hazardous Area?
One definition of a hazardous area is “an area in which an explosive atmosphere is present, or may be expected to be present, in quantities such as to require special precautions for the construction, installation and use of potential ignition sources.” Flammables and combustible dusts are dangerous if present at explosive concentrations; in an atmosphere that will support combustion; when exposed to a sufficiently energetic ignition source. An explosion is impossible unless all three requirements are present together.
Assessing the Hazards
In the case of a flammable gas or vapour its chemical properties and explosive nature are major factors that influence the extent of the hazard. Other relevant properties include the flash point temperature, vapour pressure, boiling point, extent of the explosive range, density of the gas or vapour and the ignition temperature to set off an explosion.
If the hazardous area involves explosive dusts and fibers a good appreciation of the physical, chemical and bulk material properties is required. The critical factors are the dust layer temperature at which a heated surface can ignite a layer of the dust. And the dust cloud ignition temperature at which a cloud of the dust ignites. Additional factors like fineness of particle size, dilution by inert materials and the moisture content also affect the extent of the hazard.
The size of the hazardous zone may increase during maintenance and cleaning if dust is lifted off equipment.
Hazardous Zones
The designation (naming) of the zones reflect whether the hazard is a flammable gas or an explosive dust and the likelihood that a hazard will be present. For a gas/vapour the zones and their definition are listed below.
- Zone 0 – a volume of space an explosive gas atmosphere is continuously present. An example is the vapour space in a fuel storage tank.
- Zone 1 – a volume of space an explosive gas atmosphere occurs periodically in normal operation. An example is while filling the fuel tank of a car.
- Zone 2 – a volume of space an explosive gas atmosphere is not normally expected and if it does occur, it will only be present for a short period of time. An example is drops of liquid from splitting a flange.
For dusts the zone designations are noted below and reflect the probability of the occurrence of an explosive mixture.
- Zone 20 – a volume of space where a combustible dust cloud is present for lengthy periods during normal operation or layers of combustible dust will form. An example is inside a dust collector/filter.
- Zone 21 – a volume of space where a combustible dust cloud is likely to occur during normal operation or layers of combustible dust will gather during operation. An example is beside a 25-kg bag filling-head.
- Zone 22 – a volume of space where due to abnormal conditions a combustible dust cloud may occur infrequently and for short periods of time or layers of combustible will gather over an extended period of time. An example is inside a grain milling room that gradually accumulates dust over years of operation.
A sample hazardous area zone classification drawing is shown in Figure No. 1. With this information, the necessary design decisions can be made.
Once the zone is designated the appropriate hazard protection measures suited to the zone must be applied.
Explosion Protection Techniques
As already noted the three requirements that must coincide for an explosion to occur are – the presence of a fuel, at the right concentration to burn, with an ignition source present.
One explosion control principle is to purposely introduce a non-flammable atmosphere into the process. An example is the use of inert nitrogen or carbon dioxide gas to replace air inside reactors mixing flammable chemicals or inside mills grinding explosive powders.
The other explosion principle used in hazardous areas is to select electrical equipment and designs that remove the ignition source. This can be by enclosing the ignition source or by limiting the energy from the source.
Equipment Approval and Certification
Electrical equipment for hazardous areas is marked with symbols that indicate their certification and classification. They can only be used if the correct markings are in place to verify they are suited to the particular hazardous area concerned. An example is –
The markings Ex II 1 C EEx show it is approved and certified to the specifications of relevant international bodies, while ia indicates the type of protection rating, IIC indicates the explosion group and T6 the temperature class. The markings are permanently on the equipment and recorded on the documentation accompanying the apparatus.
Installation and Maintenance
To insure hazardous area equipment retains its effectiveness it must be installed and maintained so that the protection it provides is continuously available. Only competent and qualified persons can design, install and work with hazardous area apparatus. Cables, glands, sockets, plugs, enclosures, etc must all meet the hazardous area designation. Special cable and gland installation methods and sealing techniques are required to prevent combustible atmospheres and flames from being transferred to connected, neighbouring equipment. Unless the exact requirements are followed the explosion protection is voided.
Always replace equipment in hazardous areas with a certified, exact duplicate.
Once hazardous area equipment is installed it needs ongoing inspection and upkeep. The integrity of the apparatus must be examined periodically. On numerous occasions, bolts have been left out of rated enclosures resulting in the loss of explosion protection capabilities.
Mike Sondalini – Maintenance Engineer
If you found this interesting, you may like the ebook Bulk Materials Handling Introduction.
Great article. Especially like
your emphasis on change detection. As the EE responsible for haz. location oversight, catching changes early was a challenge. Often hidden in an “improvement”, intrinsically safe equipment, static generating equipment, and rebuilt motors were examples.