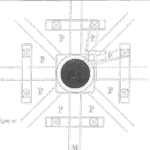
What you will learn from this article.
- There are two ways to detect holidays in tank linings.
- Explanation of the low voltage ‘wet sponge’ method of testing linings.
- The second method is high voltage spark detection.
- Importance of confirming the presence of sufficient liner thickness.
- The likely trouble spots where linings can thin.
By John F. Delahunt
2001 Carmagen Engineering, Inc. @ www.carmagen.com All Rights Reserved [reprinted with permission of Feed Forward Publishing]
Example of holidays include burst air bubble pits as a coating dries, the edges formed by corners of plates and rolled steel sections causing the coating to thin at the tip and weld overhangs and flux holes preventing the coating from contacting the metal surface.
An important evaluation of bottom linings after application to aboveground storage tanks (AST) is holiday (i.e., discontinuity, ‘pin holes’) detection. Linings are principally applied to ASTs to prevent internal corrosion that may be severe. Therefore, any holidays must be detected and repaired prior to the newly lined tank being returned to service.
Generally, two types of holiday detection are employed. For thin bottom linings under 20 mils (0.02 in, 0.5 mm)) dry film thickness (DFT), low voltage/wet sponge detectors are specified. For those linings greater than 20 mils DFT, high voltage spark detectors are employed. Each of these has its own advantages and disadvantages; the subsequent paragraphs describe these for the low voltage wet sponge test. In a subsequent newsletter, the high voltage spark detector will be described.
A low voltage wet sponge detector is a simple electronic device; it consists of a wet sponge, an energy source (5 to 90 volt battery), a ground wire connector, and another connecting lead wire to the wet sponge. The electrical leads are connected to the battery. In practice, the wet sponge is moved over the relatively thin lining and a holiday/discontinuity is detected by the wetness contacting bare steel and activating either an audible or visual indicator.
Primarily, there are several advantages and disadvantages to this type of detector; advantages include:
- The wet sponge is low cost … one commercial model costs approximately USD$250.
- It is fairly easy to use and extensive training is not required.
- It is a non-destructive test.
However, there are several disadvantages, including:
- The lining must be dry and free of moisture.
- Locating a holiday after audible indication may be time consuming.
- The lining must be dried after locating a holiday; otherwise “telegraphing” can result. Telegraphing is current traveling along a wet path and erroneously indicating a holiday where none exists.
- The major problem, however, is that it cannot locate a thickness defect that is masked by the lining.
Concerning this last point, one manufacturer states in their literature that “a coating of only one mil (0.001 in.) of paint (or coating) is sufficient to repel the current (of the low voltage battery)” and the alarm circuit of the wet sponge detector will not be activated. This inadequate thickness in the tank lining most probably will cause premature failure.
In AST lining work, these thin areas may occur at sharp edges and corners, corroded or pitted areas, welds and weld spatter, mechanical fasteners, and structural shapes. To reiterate, as long as these are coated even with a lining thickness of only 5-10% of that specified, no holiday will be detected and the opportunity for early failure is very real. Therefore, thin film linings are frequently not specified for existing corroded tanks. Heavy-bodied linings are used because of the greater chance to apply a lining to a thickness that will have greater success.
If a thin lining is used – in a new or existing tank – “striping” is frequently employed. With striping, an additional coat of lining is applied to those areas specified above where thin coatings may exist. The complete lining system is subsequently applied. Steel Structures Painting Council Specification SSPC-PA-1 contains details concerning stripe painting.
A number of standards and recommended practices are available regarding holiday detection. These include the following:
- NACE RP0188 – “Discontinuity (Holiday) Testing of Protective Coatings.”
- ASTM D5162 – “Practice for Discontinuity (Holiday) Testing of Non-Conductive Protective Coating on Metallic Substrate.”
Additional information on the use of the wet sponge holiday detector may be found in these documents. Other standards for holiday detection on pipe (internal/external), concrete and rubber linings are available also.
If you found this interesting, you may like the ebook Process Control Essentials.
Sir what is the maximum temperature to conduct holiday testing on the bottom of the tank