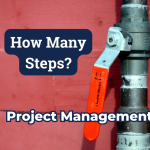
Project managers are challenged by creating, implementing, and maintaining workflows, Standard Operating Procedures (SOPs), and standard instructions. The same applies to maintenance and reliability professionals who develop preventative maintenance (PMs) and job plans. Knowing the difference between each type is the first step. Then, the number of steps in each of these often depends on the audience’s experience, the task’s complexity, and preference. It’s most important for project managers to find the sweet spot.
Project Management and the Most Common Workflows
This is my Top 12 list of the most common workflows accompanying any project.
1. Request For Information
2. Change Order
3. Monthly Status Report
4. Consultant Invoice Approval
5. Pay Application Approval
6. Set Work Breakdown Structure
7. Permits
8. Amendment Review and Approval
9. Budget Change Approval
10. Commitment Approval
11. Design Review – One Lane
12. Field Inspection/Daily Reports
Processes, Procedures, and Standard Instructions
Process
A process is a series of actions or operations conducing to an end [Merriman-Websters]. Think of a process as everything needed, expressed or implied, to produce an outcome.
Procedures
A procedure, or Standard Operating Procedure (SOP), is a series of steps followed in a regular definite order [Merriman-Websters]. Although procedures rarely capture every aspect of a process, they usually include all of the binding pieces needed for accountability.
Instructions, Guidelines, and Checklists vs. SOPs and Processes
Instructions
Instructions are detailed directions on how to do a specific task or action. Instructions may be part of an SOP, but they are typically shorter.
Guidelines
Guidelines are recommendations or best practices for carrying out an activity or task. They provide general advice but don’t go into specific steps or rigid instructions.
For example, a guideline for managing team meetings might recommend “Include time for team member feedback” but not mandate a specific structure, exact timing, or place in the meeting sequence.
Checklists
A checklist is a list of items or actions that need to be completed to ensure that a process or procedure is conducted correctly. It is a tool for confirming that tasks are not forgotten, but it does not necessarily explain how each task should be performed.
For example, a checklist for equipment maintenance might list “Check oil level,” “Inspect cables,” and “Test functionality.”
The Instructions, Guidelines, and Checklists for this short essay are the same (less specific than procedures and processes).
Procedure (SOP) vs. Process
A procedure (or Standard Operating Procedure) is a detailed, step-by-step guide for conducting a specific task or activity. It outlines the exact steps, responsibilities, tools, and materials required to complete a task and is often standardized to ensure consistency, quality, and compliance with regulations. SOPs are typically prescriptive, formalized, and legally binding.
A process is a high-level series of steps or activities that need to be followed to achieve a specific outcome. It’s more focused on the flow of work and the sequence of events (hence, the term Workflows, Work Processes, or Business Process Mapping). However, a process may not provide the detailed “how” to perform each step.
A process is more flexible and less prescriptive than an SOP.
The Good, the Bad, and the Ugly
The good, the bad, and the ugly of workflow depend on where you sit, which includes your industry and your specific organizational context.
Most people and organizations don’t have well-developed workflows; even if they were once well-developed, they are not well-maintained.
One of the first things we do when failures or near misses occur is map the workflows associated with the event. That makes business process mapping one of the three essential tools for any Root Cause Analysis.
Written Work Processes In Practice
Most people and organizations prefer fewer formal steps. Here’s a breakdown:
Experienced Staff: 8 to 12 Steps
- Why? Experienced professionals benefit from concise instructions that focus on key actions or decisions. They often rely on their expertise to fill in the nuances or contexts that aren’t explicitly detailed.
- When to Use? High-level workflows for tasks where staff already have a solid foundation and familiarity with the process.
- Challenges: Over-simplification leads to missed nuances if critical steps are skipped.
Experienced personnel, experienced managers, and project managers from general manufacturing or traditional construction companies tend to prefer fewer documented steps.
Inexperienced Staff: 28 to 34 Steps
- Why? Novices require more detailed, granular instructions to avoid missing any important steps. This includes explicitly stating things that experienced professionals might find intuitive.
- When to Use? Training materials, onboarding documents, or tasks where precision and consistency are critical.
- Challenges: Detailed instructions can be overwhelming if not organized well, leading to a risk of information overload.
Outside consultants tend to push organizations in this direction. So do project managers from high-reliability organizations or sectors like surgical centers, pharmaceutical manufacturing, aviation, and nuclear power tend to want detailed steps.
The Troublesome Middle
The troublesome middle is the 12- to 18-step work processes that work best in practice. However, neither extreme is completely happy, so a see-saw battle usually ensues when the workflows are reviewed and updated.
Quite frankly, no one is ever really happy when workflows are reviewed or updated because of the transitions that occur between those who approved them in the first place.
Balancing the Step Count
- Chunking: Break down long processes into manageable sections (phases or sub-tasks). For example, instead of one SOP with 30 steps, create three sections with ten steps each.
- Formats: Use flowcharts, diagrams, or bullet points to make the document more digestible.
- Customization: Start with the detailed version and develop a condensed “quick guide” for experienced users and refresher training.
- Updates: As staff gain proficiency, evolve detailed SOPs to summaries or decision trees.
Practical Guideline
When creating instructions, assess:
- Audience Skill Level: How much prior knowledge or expertise do they have?
- Task Complexity: Does the task involve multiple systems, tools, or decision points?
- Risk of Errors: How critical is following each step exactly as written?
A mix of detailed and high-level guides might ultimately serve your organization best, ensuring flexibility for varying levels of expertise.
How Many Steps Are Needed for Standard Instructions
Yep, from the subtitle, you can tell I prefer shorter standard instructions and SOPs. With that said, I really prefer standard instructions to standard operating procedures. Start simple and build complexity over time. Minimize what you must maintain. Above all, hire and retain project managers who know what they are doing. Competence overcomes many shortfalls in the process.
JD Solomon served in executive leadership roles at two Fortune 500 companies before starting JD Solomon, Inc., just before the pandemic. JD is the founder of Communicating with FINESSE®, the creator of the FINESSE fishbone diagram®, and the co-creator of the SOAP criticality method©.
Leave a Reply