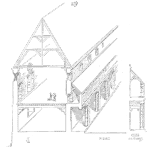
If a human is going to build, install, monitor, use, operate, repair, or dismantle, then the design team must consider human factors.
According to Wikipedia
Ergonomics (or human factors) is the scientific discipline concerned with the understanding of interactions among humans and other elements of a system, and the profession that applies theory, principles, data and methods to design in order to optimize human well-being and overall system performance.
Failures of a design may occur because the system is:
- unsafe to handle or operate
- unable to be created, assembled or installed
- difficult to operate correctly
- difficult to maintain correctly
Thus the design team should consider the four aspects of human factors
- Safety
- Workmanship/Manufacturing
- Operation
- Maintenance
Let’s consider each in turn.
Safety
Safety is a consistent concern across the entire product lifecycle and the development process.
Safety of the materials, assembly process, transportation, and installation and so on. The choices made during the design process may involve a hazardous element of a product yet should only be included with sufficient benefit and justification.
Today few would consider including asbestos in a product, due to the dangers involve processing and handling the material Likewise, a system that operates or fails presenting a danger to the operator will only be considered in essential situations.
The risks are not just to the design operating as expected it should include all elements of the procurement, assembly and use conditions. Safety concerns include the consideration of abnormal or unusual situations too. If a system is improperly operated it should remain safe.
Design features that minimize hazardous situations may be called “fail-safe” as the intent is when a failure does occur for any reason, the system does so in a safe manner.
The inclusion of operating signals and feedback naturally include elements of the normal operation and should provide clear signals when potentially dangerous situations occur.
The design of an electrical panel should provide access for troubleshooting and maintenance yet does not have to expose the technician to high current or voltage unnecessarily. Shielding, for example, may provide protection when the technician is probing the low voltage control system located nearby.
Workmanship/Manufacturing
This has a couple of components to consider.
First is the ability of the people involved in the creation (assembly and manufacturing) to actually successfully build the product. For example creating a design with a difficult to see fastener, makes the assembly easy to improperly assembly as the faster is difficult to fasten and not visible for inspection.
The design for assembly approach focused on ease of assembly in order to improve throughput and quality. The human factor elements include features that make the process easy to assembly, for example without requirements to fasten parts that are not visible. Human factor elements may also include features that do not permit improper assembly, such as orientation or alignment features that allow only one way for parts to fit.
The second component to consider is the workmanship of the product.
The finish, for example, should meet the design requirements, yet should also not pose an obstacle to proper operation or maintenance. Think of the work involved in painting a window. The requirement may be to cover all the wooden surface with an even coat of paint.
The workmanship aspect involves not painting across guide channels or sliding surfaces which make opening or closing the window difficult.
Operation
The human factor consideration here start in design and impact how a person interacts without error with the device.
This includes simple things like tactile features of buttons indicating the use is a twist, push/pull, or touch. The shape and texture of button provide visual and kinetic information for the appropriate operation of the button.
The design team should consider touch, audio, and visual interactions with the device. In some cases, smell or taste may be included. The visual elements obviously include layout, screen display, the location of emergency shutoff buttons and warnings, etc. The use of size, shape, color, labels, and layout all impact what is seen during normal or abnormal operation.
The design of control panels, cockpits, and business dashboards all require the balance between presenting the most important information clearly, yet including sufficient information for decision making in a wide range of unknown situations. With more electronics being including in passenger vehicles the ability to inform/entertain and not distract the driver is a critical human factors consideration.
A product that is difficult to understand, use or operate due to poor layout, labeling and other human factor elements may lead to the customer deeming the product a failure, not using the product, or improperly using the product.
In some situations, the device used improperly due to poor consideration of human interaction cues may lead to safety problems.
Maintenance
This is in part similar to the set of operation considerations, the ability to maintain a piece of equipment also relies on the range of human factor considerations, just focused on the needs of the maintenance activities.
This includes diagnostic information presentation, access panels or working space, inspection, lubrication, and alignment features, and the ability to actually remove and replace elements as needed.
Ideally, the design of the system will minimize the need for maintenance thus avoiding the need for human factor elements focused on maintenance activities. A range of feedback mechanisms to assist a device in its proper operation along with self-lubricating or sealed bearings, and samples of the design minimizing the need for ongoing maintenance.
When maintenance is necessary it should be easy and efficient. The design impacts the ability for the maintenance personnel to know what needs maintenance and then the layout and features of the system permit rapid repair, alignment, or replacement. Ideally, one or few tools are necessary. No specialized training is necessary, etc.
Think about the office printer or copier, when a paper jam occurs the display panel provides images and instructions to open panels, then images and directions printed on the panels and elements of the device provide easy access and direction to clear paper jams.
The system had to include the ability to detect the jam and its location, then software to drive the display panel, graphic artists for the images, mechanical and electrical engineers to provide safe and clear access to the proper locations, and the ability to sense completion of the clearing operation and restarting functionality.
The elements for consideration for human factors or ergonomics involve nearly every aspect of a product.
The tasks often fall to the industrial, electrical, mechanical, and software engineers, yet will impact the efficient manufacture, the reliable operation and the safe maintenance of the device.
Related:
General Human Factors Design Principles (article)
Safety Factor (article)
Deciding What Should Have Fault Tolerance (article)
Leave a Reply