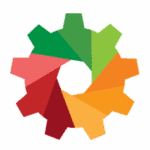
As the owner or maintenance manager at a busy organization, one of your priorities will be to monitor the efficiency of your maintenance team to sustain that level of efficiency (if it’s satisfactory), or improving it (if it’s below an acceptable level). Doing this will require that, among other things, you understand what’s really going on while staff are on the job and then identify any areas for improvement.
With methodologies like wrench time measurement, you can get insights into what is happening with your workforce and find ways to drive improvements that will produce measurable results. However, there are differing opinions on the relevance of wrench time measurement and how to use it to achieve the desired results.
Below, we’ll be discussing how a CMMS can help you to improve wrench time measurement.
What is Wrench Time And Why Should You Care?
Several activities need to happen before a maintenance job can be completed. And although each of these activities is important, in the context of this post, we want to focus on when the job gets done.
For example, let’s look at a basic, everyday maintenance task; replacing a burnt-out light bulb. A technician, building resident, or someone else notices a burnt light and puts in a request to have it replaced. A work order is raised and assigned to “technician X” to fix the problem. Then, the bulb is bought or issued out of the spare parts inventory to technician X who then goes ahead to replace it in 15 minutes.
The wrench time for this task is 15 minutes. It is simply the time spent by the personnel at work, tools in hand, in front of the job. All the activities that took place before the bulb replacement are important as well but they are not wrench time.
So, what can this information do for you?
The idea behind defining and measuring wrench time is that it allows you to pinpoint organizational inefficiencies and thereby prioritize areas for improvement. In addition, several sources including this one indicate that the average wrench time for most organizations is somewhere around 30%. Meaning that if a typical workday lasts about 8 hours, technicians are spending approximately 2 ½ hours working directly on tasks.
This does not mean that the remaining 5 ½ hours are wasted per se. They just might not be used as efficiently as possible. Also, note that in the example we used above, we assumed that the replacement bulb was readily available. If that bulb was out of stock and it had taken another 2 working days to arrive at the location, it indicates an inefficiency that should be improved upon.
How is Wrench Time Measured?
Measuring wrench time can be challenging. Let’s look at 2 of the most common measurement techniques and the issues that often affect the accuracy of each approach.
1) Self Reporting
The self-reporting approach requires maintenance personnel to report their work activities and delay times. The major flaw in this method is that workers tend to overestimate how much time they actually work. They may do this because they genuinely don’t understand how to make the calculations, or because they are afraid of being penalized for reporting low figures.
Therefore, it’s common to see technicians reporting wrench time of 70% and above, which is almost never true.
2) Day-in-the-life-of (DILO)
Under this approach, an observer follows a technician all day to observe how they work. Again, the method comes with its flaws. First, the staff under observation may become nervous or feel threatened which could affect their performance for that day. Secondly, several factors could make that day different from other typical days – there could be delays with inventory, an emergency repair situation arises, a tool is missing or broken, technicians work more because they now they are watched, and so on.
In such cases, any measurements taken won’t reflect the objective reality.
Again, wrench time measurements with DILO are also high at 50% or more.
CMMS and Wrench Time Measurement
We’ve already seen the challenges in getting accurate wrench time measurements so simply measuring wrench time will not improve staff productivity or your maintenance operations. What will improve wrench time is proper maintenance planning and scheduling which is what a CMMS is designed for.
When you’re trying to improve your wrench time, a CMMS will help you to pinpoint where the problems are by tracking the typical work order. Referring back to our previous example (replacing the burnt-out light), let’s imagine that the Work Order for that job was created in your CMMS at 10.00 am on a Tuesday shortly after receiving the request. As the maintenance manager, you know that replacing that type of light takes 15 or at the most 25 minutes to fix. However, by close of work the next day, the work order status still appears as “in progress” in the CMMS database. A job that ought to last minutes has now stretched over 2 working days.
This immediately shows you that there’s a problem. Especially when you notice these delays keep happening repeatedly with other work orders as well. It tells you that there’s a systemic problem with your planning and scheduling that needs to be investigated. Many times, what causes these types of problems is some inefficiency in putting the resources (labor, material, tools, etc) together.
On a side note, if you are using Limble CMMS, you will notice that it tracks how long did the technician had a PM/WO open for which helps technicians more accurately estimate how much time did they spent on a certain PM. It is not perfect, but it can help with tracking wrench time more accurately.
The Issue of Productivity vs Wrench Time
Some of the arguments against measuring wrench time are based on the fact that improving wrench time alone does not automatically translate to improved productivity or better results. If a technician shows up for work and spends the entire day hands on a task without any breaks, but ends up delivering subpar work, although their wrench time would be remarkable, the whole day has been wasted on shoddy work.
If you get your wrench time measurement right, it can reveal areas for you to make improvements and achieve major gains in your maintenance productivity. But you still need to have competent people executing the actual work if you want to see improvements in your plant maintenance.
Leave a Reply