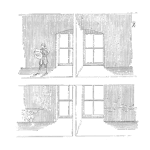
A plan is a guide or roadmap for intended action.
A reliability plan is also a collection of specific tasks and milestones and enhanced with a rationale to allow the entire team fully understand their role accomplishing the reliability objectives.
The plan is a way to achieve the desired business objectives. Meaning the product is reliable enough to meet customer expectations, minimize warranty expenses, and garner market acceptance. The plan is just a plan, it is the accomplishment of the tasks, the decision which improves the design, the signals monitored that stabilize the supply chain and assembly process, that make the difference.
A plan without action is not worth the effort.
Key elements of any Reliability Plan
The overriding key to a successful reliability plan is to understand that no two plans are the same. Using the plan from the previous project is destined to fail. Craft the plan given the current situation, information, and risks.
Although each plan should be tailored to the project each also should address the following key elements:
- Goals/Objectives
- Risks/Challenges
- Predictions/Estimates
Keep in mind that a reliability plan is not a test plan alone. It may or may not include testing. Yet does require a goal, risks, and measurements for comparison to the goal.
Goals/Objectives
How reliable does your product need to be to be considered successful? How many should last how long under what conditions performing which functions?
Be specific.
Connect the reliability goals up to your overall product platform, business financials, and brand. Make these as explicit as possible. Later when evaluation the possibility of releasing a product that is just 1% higher in failure rate than desired, you will have an ability to understand the magnitude of the potential impact.
Connect the goals to the elements within the product and across the product’s lifecycle. Apportion the goals to the major elements and key components of the product and communicate the specifics to your team and suppliers.
Also, evaluate the changing nature of the environment around elements within your product. The temperature is not always the outdoor ambient, for example.
Understand the cost of failure, the cost of warranty per unit shipped, or the cost of a lost customer, or relevant impact of a failure.
This is essential when balancing cost, time to market, and feature set decisions with reliability performance.
Risks/Challenges
Many teams naturally consider what could go wrong, what could fail, during the design process.
The reliability plan should help the team discover, reveal, coordinate and prioritize this list of risks.
Risks and challenges may take a few different forms. What is known to be a problem and what is unknown? For some elements of a system, we know from previous product performance, internal testing, or engineering judgment that this element of the design does not meet our reliability goals. While we do not know how to resolve that issue, it’s a risk.
Sometimes we have a new material, process, invention, or application and that provides a realm of uncertainty. We do not know how the product will perform. We probably have some ideas and most likely a few questions. The plan should include ways to reduce the uncertainty.
Finally, there is the possibility that no one on the team knows about specific risks. These are unknown unknowns. Exploring the performance of early prototypes and discovery evaluations permit the team to reveal weaknesses or faults.
The team’s overall challenge is to finds all the relevant risks, prioritize, and resolve as many risks to reliability as necessary. Running a few simple tests that ‘pass’ generally contain little to no information. Instead, find margins, discover faults, reveal weaknesses deliberately.
If the team already have a long list of issues to resolve, work on those and ensure no new risks create problems.
The amount of risk discovery necessary is inversely proportional to how well the team understands the field reliability performance.
Predictions/Estimates
A goal without a means to measure progress against the goal is pointless.
Likewise, measuring reliability without a goal for comparison is futile.
There is a wide range of reliability engineering techniques to draw from to evaluate the state of the current design. From early predictions based on little more than vague industry collated data, to detailed failure mechanism specific accelerated life testing, the aim is to provide feedback to the team regularly.
The early estimates are ‘rough and uncertain’. Later in the program, the estimate and testing results may provide specific, detailed, models that accurately portray field reliability performance.
Based on the goals and risks, the elements of the plan should provide regular and increasingly accurate measures of the expected reliability performance. Connect each model, prediction, analysis, and life test to a specific reliability goal for comparison. Plus, link the compilation of the estimates to key decision points in the program.
This is just a rough outline for the development of a tailored reliability plan for your project.
Let me know what questions you have and let’s get you a plan that makes a difference and achieves the goals.
Related:
3 Elements of Reliability Goal Setting (article)
Guiding Programs by Product Goals (article)
When is the Best Time to Establish Reliability Goals? (article)
Fred,
I agree with your planning process. Trying to minimize the unknown unknowns requires a lot of teamwork and thinking outside the box.
In a previous post, you mentioned that the process of revising a system or product has risks. Safety, technical, schedule and financial risks must all be considered. Make sure these issues are included in the risk assessment.
Hi Gene, nice addition to the article and I agree your list of additional considerations is essential.
Cheers,
Fred
In addition to what is described I believe the integration of training within the framework of the plan will serve to enhance the effectiveness of the execution of the plan. Too often we have asked team members to participate in activities where they lack the training to meaningfully participate.
I also believe the absence of uncertainty analysis could cause result in barriers that are overlooked and could induce unperceived risk that limits the success of the plan.
Hi Lennox, nice addition. So, what kind of training is most useful. On the spot coaching? Taking advantage of “teachable moments”, or maybe formal classes, either full day approach, workshops, maybe study groups, or a mix? How about something like the Lynda.com approach with asynchronous training courses that your team can study as needed with support by the local reliability pro for Q&A….
There are a lot of options and one of the things I’m exploring doing with the Accendo Reliability site is provide just the right training to support the reliability training/coaching element of being a reliability engineer within an organization. So very interested in what you think will work or be useful?
Cheers,
Fred