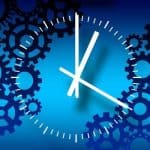
Maintenance workflow is the step-by-step process that gets initiated by some trigger event to the point where the action is closed out. For example, in a typical maintenance operation, a trigger event could be a report of faulty equipment. The step-by-step workflow process would include the generation of a maintenance order, the planning of the task, the execution of the repair and the reporting at the end of the job. Every organization has a workflow process whether it is officially documented or not; there is always a standard way to get things done. When this process is not well-defined, it can lead to frustrations on the part of employees trying to get their jobs done as well as major inefficiencies that are costly to the organization over time. In comes maintenance management software…
CMMS Software Improves Maintenance Workflow
With the advent of CMMS software and the continuous improvement in workflow aided by these systems, substantial advancements have been made in managing maintenance workflow processes and the automation of standard tasks. There are four main stages in a maintenance process:
Stage 1: there is the initiation phase where a maintenance event is triggered. This begins with the report of a fault or is triggering by a preventive maintenance scheduled event. In some cases, condition monitoring of equipment may pick up an increase in vibration or some other fault, which leads to the trigger of a maintenance activity. A CMMS system is designed to enable these events to be automatically triggered by the system, or triggered by an authorized user.
Stage 2: the maintenance event is planned. A planner will have access to the trigger event as well as parts and resource availability for maintenance technicians through the CMMS system. Work orders can then be automatically generated, parts issued to technicians and time allocated for known tasks.
Stage 3: The work will be completed in the field and equipment restored to normal operating conditions. Results of the work will be entered into the system that can then be used for Root Cause Analysis, which can be used to improve the preventive maintenance program.
Stage 4: Reports, graphs or dashboards can be generated so that management is able to evaluate performance of the maintenance and asset management function against metrics, as well as identify opportunities for improvement. Automatic events can also be programmed into a CMMS system, so that the failure to complete scheduled preventive maintenance tasks (or health and safety tasks) are elevated to the appropriate level of management.
A CMMS system with a well-defined workflow process can be invaluable tool in managing reliability of assets as well as the efficiency of the maintenance function. Automatic handling of key inputs ensures that the right information gets to the person who needs it. Integrating workflow with parts availability means that a maintenance planner has all the information they need at their fingertips to efficiently plan the resources to get the job done. Data analysis ensures that progress against metrics can be monitored on an ongoing basis and improvements driven through immediate access to information. This results in improved maintenance performance and reliability.
DPSI’s maintenance management software helps manufacturers and other organizations successfully manage all types of maintenance workflow. Interested to see what our work order management software could do for you? Get started with a free trial today!
Leave a Reply