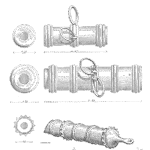
Co-authored by Mike Vella
Hard work alone doesn’t guarantee success in business. Even after you’ve invested your inspiration, money, emotions, creativity, and prayers, the reality is that we live in a highly competitive world. You can’t afford to simply tread water. So, let’s assume you’ve either made a strong start in your field or joined a profitable company. What ensures that your future will be better than today? The answer lies in leadership and the team deciding to continually evolve, change, and improve.
As a Leader or Manager, you already know that continuous improvement is key to sustaining and growing your business. If left unchecked, rising costs—both fixed and variable—will slowly erode your profits, quarter after quarter, until they vanish altogether. Meanwhile, customers are rarely content with the status quo. They expect more value with every purchase, which means your competition is constantly eyeing your sales, eager to turn your customers into theirs.
Despite recognizing the importance of continuous improvement, it often gets pushed down the priority list. Leaders and managers are so consumed with managing today’s issues that tomorrow’s needs always seem to arrive too quickly.
From a strategic perspective, one way to think about continuous improvement is through the lens of the Operating Profit Bridge. Picture yourself as a Group President or General Manager. Sometime in the third quarter, you start planning for the next year’s business. Leaders and their teams know their performance will be judged by how well they plan and execute the business strategy. Typically, unless faced with extraordinary challenges, the plan will be designed to ensure that next year’s performance exceeds the current one.
But there are two key forces threatening profits: planned price concessions to retain customer value and inevitable cost inflation. To bridge the gap from this year’s operating profit to next year’s, these two negative factors must be countered. The strongest tools at your disposal are improvements in quality and productivity, along with reductions in material and component costs. If your value proposition is strong, additional profit will come from increased revenue.
Now that the challenge is clear, what does continuous improvement actually look like in practice? Given that the challenges are ongoing, continuous improvement must be approached systematically, not randomly.
The first step in creating a culture of continuous improvement is for Leadership to decide that it is a core value. This commitment should be viewed as critical as any other asset the company owns—whether that’s equipment, technology, facilities, patents, or intellectual property. Once that decision is made, the next question is how to implement it.
One proven method is the Quality Operating System (QOS), developed by Ford Motor Company’s Electronics Division in 1986. QOS offers a systematic way of managing continuous improvement, helping businesses track performance through structured, customer-focused metrics. When effectively designed and executed, QOS drives improvement across all areas of the business, benefiting everyone who relies on your success—your family, suppliers, community, employees, and customers.
The QOS process employs tools that systematically enhance customer satisfaction and financial performance, ultimately leading to long-term business growth. Here’s a brief outline of the process in ten steps:
- Define what’s important to your customer.
- Determine what your customer values most in your relationship.
- Common factors may include quality, cost, delivery, innovation, safety, reliability, and service.
- Confirm how your customer measures satisfaction.
- Don’t assume you know what your customer values.
- Validate that your efforts align with their actual desires—not just what you think they want.
- Identify the drivers of results.
- Focus on managing internal process controls (leading indicators) that directly impact what your customer values (lagging indicators).
- Teach your team to use simple visual tools to track progress.
- Utilize trend charts, histograms, Pareto charts, and more to visually represent performance.
- Hold regular meetings to compare current performance against targets.
- Ensure your efforts are consistently moving toward the desired outcomes.
- Analyze the data.
- Use tools like Cause & Effect, regression, and correlation analysis to identify the true drivers of performance.
- Implement structured problem solving to tackle chronic issues.
- Define the problem, identify the root cause, and take corrective action.
- Verify the effectiveness of corrective actions.
- Use tools like trend and Paynter charts to track progress.
- Confirm customer satisfaction.
- Share your performance results with the customer and compare them against expectations.
- Repeat the process.
- Continuous improvement is just that—continuous.
Success in business is never guaranteed, and the threats to long-term viability are often known. Continually satisfied customers are the foundation of a winning strategy. By continuously adding value to the customer relationship, you protect and grow your revenue. Leaders must instill continuous improvement as a core company value—one that identifies customer needs, tracks performance, and mobilizes the organization’s efforts through a structured process like QOS.
Ray Harkins is the General Manager of Lexington Technologies in Lexington, North Carolina. He earned his Master of Science from Rochester Institute of Technology and his Master of Business Administration from Youngstown State University. He also teaches manufacturing and business-related skills such as Quality Engineering Statistics,Reliability Engineering Statistics, Failure Modes and Effects Analysis (FMEA), and Root Cause Analysis and the 8D Corrective Action Process through the online learning platform, Udemy. He can be reached via LinkedIn at linkedin.com/in/ray-harkins or by email at the.mfg.acad@gmail.com.
Mike Vella is a retired quality and operations leader, most recently serving as Senior VP Operations at the Suter Company and prior, Vice President and General Manager of TI Automotive’s Brake and Fuel Group in North America. Mike was with TI Automotive for 30 years. Mike received his MBA from Wayne State University and his BS from Western Michigan University. His contributions to the Manufacturing Academy include training courses focused on leadership, quality, problem solving and statical analysis.
Leave a Reply