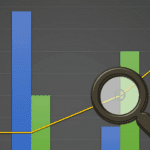
It’s no secret that equipment maintenance software offers many benefits to your organization. However, organizations frequently find that the software doesn’t deliver the end results they anticipated. This often happens because organizations don’t maximize CMMS potential. In other words—they’re not using their software to its fullest potential.
Learn How to Maximize CMMS Potential
Companies often see CMMS software as the solution to their maintenance problems, but software cannot resolve underlying issues. Organizations cannot achieve the results they desire from a CMMS implementation if their work processes are flawed and inefficient to begin with. A CMMS implementation can also fail to achieve the hoped-for results if organizations don’t use all of the features their maintenance management software offers or if they don’t have access to quality data.
By failing to maximize CMMS potential, your organization is missing many opportunities to save time and money. Most CMMS users don’t use their software to its fullest capacity and occupy only 10-50% of the available functionality. Most users don’t even know about all of the features that their CMMS system offers.
Many organizations just use their maintenance software for recordkeeping purposes. However, a CMMS system’s functionality goes far beyond recordkeeping. The more you use your CMMS software, the more you can increase your organization’s productivity and profitability. The following are some ways in which maintenance managers can maximize CMMS potential.
Improve and Maintain Data Quality
One of the primary factors that contribute to the effectiveness of CMMS software is data quality. It’s essential to have access to quality data if you want your CMMS to provide accurate, real-time statistics and business intelligence. You can improve data quality by establishing data standards, naming conventions, and classification requirements. Before migrating your data to a new CMMS, standardize and enhance the data according to your pre-defined standards. Cleaning up and standardizing inconsistent, incomplete, and inaccurate data will enable you to use your CMMS to reduce equipment downtime, leverage reporting functionalities, identify and dispose of excess inventory, and improve maintenance efficiency.
Analyze Work Orders and Improve Processes
Maintenance software is a great tool for identifying areas for improvement. Maintenance managers can use CMMS software to analyze work orders, identify areas where maintenance technicians spend too much time on non-value-added tasks, and then determine ways to improve the situation.
Record Key Measurements
Record key equipment measurements, such as pressure and temperature. Analyzing this data will allow you to identify abnormal readings and address issues to avoid equipment failure. In addition, maintenance technicians can define acceptable ranges and criteria for equipment measurements and input this information in the CMMS. If a recording falls out of that range, the system will automatically notify maintenance technicians immediately so that they can take corrective action.
Carry out Long-Term Capital Planning
Equipment maintenance software can also aid you with long-term capital planning by helping you accurately predict timing for equipment replacements. You can refer to the equipment’s installation date and evaluate its expected performance life in order to predict when it will need to be replaced.
You can also analyze the repair costs of a piece of equipment to determine whether the end of the equipment’s performance life is near. Additionally, the data that CMMS software provides can be helpful in justifying capital expenditures for equipment replacement.
How to Achieve CMMS Optimization
In the process of optimizing the use of your maintenance software, you’re bound to hit many roadblocks. Some of the most common reasons why organizations struggle to unlock the full potential of their CMMS systems include the following:
- Lack of commitment from upper management
- Failing to perform a comprehensive needs analysis to determine department and organization needs
- Lack of IT support
- Inflexible IT or corporate policies
- Failing to develop an implementation strategy and plan
- Lack of CMMS training
- Improper specification of required CMMS features and functions
- Not selecting a CMMS capable of meeting your department’s current and future needs
Selecting the right maintenance management software for your organization is crucial if you want to maximize its potential. Choosing the right software vendor is equally as important. Your vendor should be knowledgeable and financially stable as well as have a proven track record, strong references, and stellar support. Select maintenance software that offers flexibility, ease of use, scalability, and key features, like user-customizable screens, mobile capability, a robust reporting module, and data security.
By doing your due diligence, you can ensure that your CMMS system will serve your organization’s needs for years to come. If you’re looking for feature-rich, fully customizable CMMS software from an experienced and knowledgeable vendor, contact DPSI today or sign up for a free trial. We have over 30 years of experience helping customers overcome maintenance challenges and maximize CMMS potential.
Leave a Reply