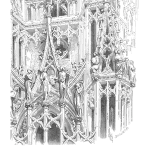
One method to clean particles from a liquid or gas is to pass it through a filter. The filter is a screen that traps and holds the contaminants on its surface while allowing the fluid to twist its way past the build-up and screen. The screen can be used until the back- pressure from the collected contaminants choke it so severely that the fluid flow falls drastically. At that point the screen must be cleaned. This article explains how membrane and leaf filtration processes work and the critical factors that produce successful filtration results.
Keywords: filter cake, pressure-leaf filtration, filter aid, precoat
What is membrane and leaf filtration?
The name membrane filtration comes from the media used to remove particulate contaminant from the fluid stream. In the first days of the technology, fabric such as cotton cloth was drawn tight across a frame and liquid was passed through it. The cloth was the membrane used to retain the material filtered from the liquid stream. A coffee filter paper is a membrane filter.
Leaf filters consisted of flat, circular or rectangular filter elements spaced apart inside a pressure vessel. Circular designs are clamped together on a center shaft while vertical designs are positioned side by side on a manifold. A coffee plunger is a leaf filter.
The Filtration Process
Filtration is the removal of particles above a certain size by trapping them on a screen (membrane) full of holes of a smaller size. Where microscopic or gelatinous contaminants are to be removed it is often necessary to introduce a filter aid onto the screen.
When particularly fine filtration is required and the screen hole size is not sufficiently small a precoat is first layered onto the screen as a bed on which the filtered material can form and not be flushed through the screen. If the filtered material rapidly causes back-pressure it is possible to use the filter aid as a body feed continuously injected into the liquid stream. In this case the body feed settles onto the screen along with the material to be filtered and creates cavities and openings through the cake which become fine passages for the liquid to pass but are to small for the contaminant.
The first filtered particles are held back by the screen or precoat. They begin to bridge over the holes and voids. Soon the bridged material becomes the actual filtering media and the screen only acts as the supporting structure.
Precoat is not used unless it is necessary. Long, streaky or flat contaminants intertwine and will form a weave mat across the screen. Round or chunky contaminants tumble together filling up the gaps between neighbours and will themselves form a sediment bed across the supporting screen. Figure No. 1 shows a filtering bed formed on a supporting screen.
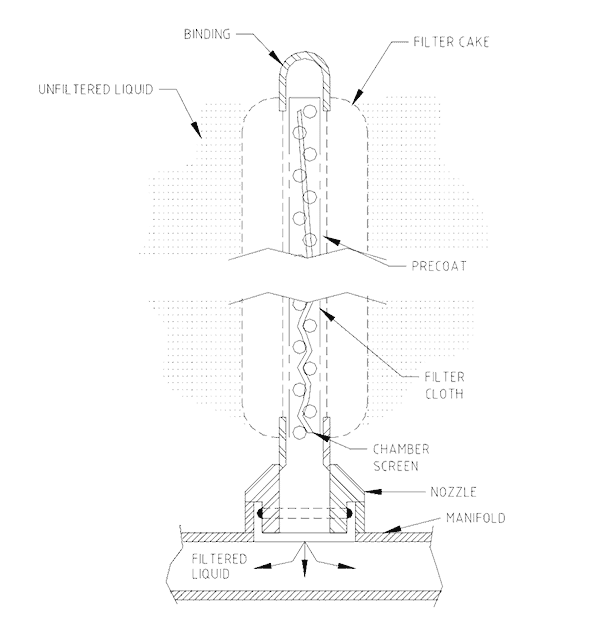
The built-up sediment cake can be removed by a number of methods. Shaking, spinning and blown-off by water or air are common. Automatic cleaning sprays starting at the top and working their way down can be installed and used to wash down the screens. Shaft mounted screens are spun clean by rotating the screens at high speed after emptying the filter. Non-automated designs require the filter to be opened up and the screens manually hosed down.
Critical Factors Affecting Filtration
There are several key factors that must be confirmed to insure successful membrane filtration.
- Screen hole size determines the size of particles that will pass through the screen and those which will not. The holes in the filter screen or fabric must not be so large that the filter weave or sediment bed cannot develop.
- Filter cake thickness must be consistent in size and homogeneous (uniform in make-up) across the screen otherwise differential flow patterns occur and only part of the filter is used and throughput soon falls. Fortunately the nature of creating a bed means that any preferential flow in one area builds the bed up until the pressure is even with the rest of the bed. Provided the contaminant size is evenly distributed in the flow stream the cake on the screen should filter equally everywhere.
- Low flow velocity through the filter is need so as to not disturbed the filter cake and move it off the screen. This requires sufficient surface area of screen or membrane. The filter manufacture can best advise you on the necessary filtering area and fluid velocities.
- Process chemical attack of the screen material is prevented by proper selection of fabric of sufficient thickness to also provide the necessary mechanical strength to take the forces that develop as the back- pressure increases during the filtration run.
Problems with Filter Screens and Membranes.
Below is a list of typical problems that can occur with membrane and with leaf filters and what to do to solve them.
- Screen or fabric blinding occurs when the particles to be filtered get caught in the screen itself and block the holes. This introduces a solid obstruction to the flow and if enough holes or pores are blocked the flow falls and back-pressure builds quickly. Examine the particles causing the blinding and consider changing screen, or membrane design, or hole shape; use a course filter aid to make a filtering bed; change to a different type of particulate removal technology.
- Screen or fabric rupture can be a result of fair-wear- and-tear over a long period of time. It could also be the result of high local velocities across the screen; large solids impacting the screen, water hammer, excessively high differential pressure or chemical attack.
- Poor fabrication and assembly of the screen onto the frame. Screen wire is very delicate and a crease or a scratch introduces a stress raiser, which becomes the weakest point under pressure. Do not damage filter screens, replace damaged screens. The screen wire must be sealed into the frame and/or hub so that the flow cannot pass between the wire screen and the frame. If necessary use two-pack epoxies, or similar, to fill the voids between the screen wire and the frame.
- Improper cleaning of the screen between filter runs due to caked-on old sediment. If necessary repeat the cleaning sequence to try and dislodge the cake. Chemical cleaning can be used if safe to do so or use hot liquid flushing in an attempt to soften the built-up.
- Silted filtrate from the filter can be a sign of screen rupture. In the case of screens rotated for cleaning it can also mean the shaft seals are passing. On manifold screen arrangements it can mean the seal between the manifold and screen is damaged or not sitting properly, or the screen is not properly positioned in the manifold.
Mike Sondalini – Equipment Longevity Engineer
References: Perry’s Chemical Engineers Handbook, R. H. Perry, D. Green, 6th Edition, McGraw-Hill International
If you found this interesting, you may like the ebook Bulk Materials Handling Introduction.
Leave a Reply