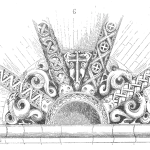
A high-pressure packer for use in 9 5/8”, thick-walled, P-110 casing is being developed for a well barrier application. It is based on a legacy configuration. Is it a candidate for simulation?
The modelling of completion equipment begins when a component is developed using 3D CAD software. The engineer selects component geometry based on application constraints, initial calculations, a basis of design document, etc. After modelling all components in the configuration, these models are merged to create the assembly model.
Simulation is then performed on the models to study their response to inputs. Finite elements analysis (FEA) software is used to study a component’s “localized” response (e.g., stress in a fillet) to a range of combined loading inputs. Computational flow dynamics (CFD) software can be used to simulate the response of an orifice over a range of fluid flowrates. And nonlinear analysis software can be used to simulate the viscoelastic response of a rubber component to a force input over time.
Simulation requires expensive software and computing systems, experts who can perform the simulations, or the use of 3rd parties. Simulation is not always required to establish component or assembly response to inputs, but some reasons for conducting simulation are:
- Regulatory requirements.
- Complex loading scenarios.
- Industry product standard requirements.
- The equipment is for use in a critical application.
- Investigation of nonlinear response to inputs (rubber packing elements).
- Configuration maturity: Is the TRL high (mature, proven) or low (immature, unknown)?
The answer to the question posed at the beginning of this article is that the high-pressure packer should be further analyzed using simulation if the TRL is low, or if any of the other bullets apply. If the decision is YES, then all simulation must be conducted early in the project so that any necessary improvements can be assessed as part of the laboratory testing program.
TRUTH: Simulation must be conducted when the highest equipment reliability is needed.
This is the 8th in a series of 10 articles on critical equipment design for offshore completions.
- Critical Equipment Fundamentals
- Technology Readiness Level (TRL)
- Materials and Design Risk
- Temperature Deration
- Design for Reliability (DfR)
- Using Industry Standards in Design
- Factors of Safety and Load Factors
- Modelling and Simulation
- FMEA Improves the Bottom Line
- Lab Testing Programs
Leave a Reply