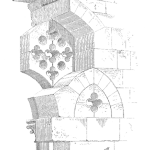
Guest post by Ken Latino.
About 13 years ago, I began a reliability journey at a large paper mill. At that time, the mill was pretty reactive and I was naïve enough to think I was going to single handedly turn it around. While I thought I had all the answers and was going to teach the mill a thing or two about reliability, it ended up teaching me a hell of a lot more.
This short essay is about the lessons I learned and the practical side of reliability and later what has become known as Asset Performance Management or APM.
Lesson 1 – Patience
When I started in my reliability role, I had lots of initiatives that I was ready to implement immediately. I wanted to institute a mill-wide RCA program, Operator Driven Reliability, Asset Strategy Management and many others. What I learned was that in a large plant with over 1100 people and 50,000 assets, there is always a lot more work then resources. The initiatives that I was suggesting only created more work, in the short term, and it was not practical. I once had one of our Operations Superintendents ask me how much time his people would need to put in each week for the RCA effort. I told him conservatively that it would take 3 to 4 hours a week. He laughed at me and said HELL NO. So the lesson is that while proactive activities are needed, they will always take a backseat to reactive, urgent work. So try a pilot in a receptive area of the facility and do whatever it takes to make it successful. Then expand once people can see the value. This is how to create a virtuous cycle that can stand the test of time.
Lesson 2 – Culture
I was very fortunate to have supportive management that gave me tremendous freedom to implement my reliability initiatives. But even with supportive management, culture ultimately drives behavior. It is nearly impossible to promote proactive behaviors when the culture has been living with reaction for over a century. At the end of the day, the frontline worker needs to embrace the proactive activities. I remember one of our oilers telling me; “you guys think you are running the mill, but the fact is we are the ones who run the mill!”. That stuck with me because I learned that operators, maintenance craftsmen and other frontline workers are the ones who can make or break any initiative. I was again very fortunate to have worked with some of the greatest operators and craftsmen in the world. Once they saw that the improvement initiatives were beneficial and actually helped them do their jobs, they supported the effort 100%. The lesson here is to work directly with your frontline workforce to implement your reliability efforts. Once they embrace the concept and see the value, they are the ones who have the greatest influence on driving improvement and they will change the culture.
Lesson 3 – Work Processes
In order for an initiative to stand the test of time, there needs to be defined work processes. We developed a high level reliability model that showed how all of the work processes fit together into a continuous improvement process. We developed large posters and posted these across the mill as a constant reminder of the why, how and what we were trying to do. We even developed a glossy “brochure” of the process that we used with senior leadership and to demonstrate to customers our commitment to reliable operations and meeting customer commitments. Work processes were the driving factor to the changes. They are the step by step guides that make the changes sustainable and reproducible over time. The lesson here is that real change takes time and there needs to be formal work processes to sustain the change over the long term.
Lesson 4 – Technology
When we started, we had a spreadsheet for everything. We had multiple point solutions that were not integrated with each other or our SAP system. Again, I was fortunate to have very enlightened management that provided support and tools when we needed them. We asked for a digital solution that could be used to enable our reliability work processes. The decision was made to invest in the Meridium APM (now GE APM) solution. This set of APM tools allowed us to enable the work processes that we had developed. It was integrated with our SAP system so we could perform inspections using handheld devices and then seamlessly create SAP notifications from our findings. This integration, along with many others, were the keys to making the work processes practical and effective. The lesson here is that any system must be easy and practical if it is going to be used. Without the automation and integration of the APM solution, our work processes would have been impractical with way too many manual steps to be effective.
Lesson 5 – People
At the end of the day, great work is about the collective efforts of people. Everyone has something to contribute and everyone has good ideas. It does not matter if you are a laborer, millwright, operator, supervisor, manager or executive. Everyone has a way to contribute to make our assets perform better. I worked with some of the greatest people at the mill. The managers/executives who gave me the flexibility to try new things, the maintenance journeymen who supported me and saved my ass on weekend duty and the operators who educated me on creative ways to instill reliability activities into operations. The lesson here is that everyone’s ideas matter and everyone has an important role to play in asset performance. We just need to be willing to listen and to engage with our people!
While I am no longer at the mill, I am happy to report that they are doing great. They continue to look for new and innovative ways to improve asset performance. So while I thought I was the one who was going to teach them a thing or two about reliability, they were really the ones who ended up teaching me!
Leave a Reply