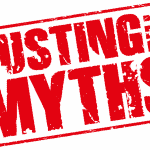
Many believe strongly in the value of warranties on new / refurbished equipment. They go to great lengths talking about how important it is to do the manufacturer’s recommended maintenance to maintain validity of the warranty. This is a continuation of the last blog article on having too many failures despite following manufacturer’s recommendations. Manufacturer’s usually recommend maintenance and spare parts for their products. In our last blog we can see that those recommendations are often flawed. So what about their warranty?
Warranty is a form of insurance, or as I see it – gambling – against yourself. The payoff only happens when something bad happens (to you). Like gambling in a big casino, the odds are not in your favor. In fact it’s the house that usually wins. After all, whose money do you think they use to build those grand casinos?
If you have a failure, and then claim that it was caused by something the manufacturer warranted, then you are counting on a payoff of some amount, generally limited to the capital cost of the asset that failed in an extreme case. The cost of its removal, installation and the downtime associated with loss of its use is not covered. So, as a rule, the warranty will only pay out a fraction of your total costs due to the failure. The kicker is that payment isn’t a sure thing. No one likes to lose a gamble. Buried somewhere in the terms of the warranty you are likely to find a clause or statement that requires you to follow the manufacturer’s recommended maintenance. If you haven’t followed it, or even if you have but you can’t prove it, then the warranty claim will be deemed invalid.
From the legalistic perspective that’s fair – you didn’t do the maintenance that they said you should do, you suffered a problem, but that was your risk when you failed to do the recommended maintenance that had been prescribed. Whether that maintenance is effective or not, is not even a consideration. Most warranty claims run into this glitch and it can take months of contractual wrangling to settle, often with your company (the end user) getting nothing other than costs of having gone through the claims process.
Are warranties worth it?
In my opinion, no, and here’s why.
Few warranty claims ever pay off due some fact such as failing to do the recommended maintenance. Doing that maintenance, as we saw in our last myth buster (#20), is not often the right maintenance and it can fail to deliver the reliable service you want. You end up spending more on maintenance that you really should, and you get less uptime in return.
Warranties don’t go on forever. They are generally limited to a period of time for new assets and after they are rebuilt, if they were rebuilt by manufacturer’s recommended repair shops. The old equipment you have is not covered. It will however, be operated and maintained for a long time to come. Maintenance practices and discipline are no different for new assets under warranty than they are for older assets long out of warranty. After all, it’s the same maintenance department looking after those programs If compliance to maintenance schedules isn’t perfect, you won’t make good on any warranty claims.
Following the manufacturer’s recommended maintenance to remain in compliance also very often requires that you use parts supplied by the OEM. Failure to do so can invalidate the warranty. While the maintainers may indeed ask for those parts, does the supply chain deliver them, or do they find less expensive, equivalent alternatives? In practice, the latter often happens. After all, the supply of parts for maintenance warranty isn’t handled any differently than the supply of parts for any other maintenance work.
Management of the warranties is a lot of work for people in contracts – they need to watch dates of validity, ensure compliance to all conditions and then be aware of any potential claims that may arise. Good sharing of information among your purchasing, contracts, insurance, and maintenance groups is essential. In reality, that sharing of information is often not all that good.
Summing it up, the effort required to actually make good on any warranty claim is quite high, involves a number of different groups / departments, good information sharing and good discipline in executing a very specific maintenance program that we are, later quite often, willing to compromise.
On the manufacturer’s part, they’ve got it pretty sweet. Assuming their products are manufactured to high quality standards (most are), then materials and workmanship are good and the chances of a flaw that will trigger a warranty claim are low. By providing a good product they are at low risk. Then they require that the buyer follow a very specific program of maintenance, using materials that they supply (usually at a premium) – both conditions that many end users won’t adhere to. They lower their risks even further. Of course they are charging for the warranty – it’s built into their costs, which the buyer pays. They are like the house in a casino and they have the buyers gambling against themselves.
So as a manufacturer, they’ve got it good – they make money selling you the asset, its warranty, and parts, and reduce their risks by providing a good product (which they’d do anyway) and enforcing their conditions if there is any deviation from their dictates.
What does a warranty cost? It’s about 2 to 3 % of the capital cost of the asset. Considering that you are highly unlikely to make a claim, and if you do, even more unlikely to win it, and then if you do, the payoff is low, then is it money spent wisely?
The cost of a full Reliability Centered Maintenance program will be about 2 to 3 % of the capital cost of an asset. Instead of giving you no return, it will produce a comprehensive program tailored exactly to your operational situation that stands a very high chance of producing reliable operation, uptime / availability and low costs.
When I compare those two options, I’d go for the RCM program every time.
Leave a Reply