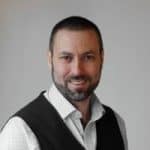
A Systems Engineering Approach to Reliability with Andrew Kelleher
It is my pleasure to welcome Andrew Keller to the podcast. He is the Managing Director for Rams Men Taught in Germany.
I’ve trained as a materials engineer, having spent approximately 20 years working in different aspects of reliability engineering from failure analysis to risk-based inspection, to design. He has experience in all aspects of reliability engineering. He is now self-employed, helping and targeting process plant engineers.
In this episode we covered:
- What’s the traditional approach to improving reliability implants that we typically, see?
- There’s lots of tools out there: FMLA, RCA, maybe some work planning, I don’t know if they’re interconnected as well as they should be?
- When we look at using all these different tools when needed: FLMA, RCA, what are the limitations when we have that ad hoc approach?
What’s the traditional approach to improving reliability implants that we typically, see?
When I reflect, for example, on my time in the aerospace industry, if you would ask the engineers what their approaches are, they would say they have a safe life approach, or a defect in damage tolerant approach. I think they have a whole lot of tools and methods that they apply. They have criticality analysis as maybe a standard tool, FMLAs risk-based processes, root cause failure analysis, bad actor analysis standards and practices, but that’s a collection of tools, but I’m not sure that classifies to be called an approach.
There’s lots of tools out there: FMLA, RCA, maybe some work planning, I don’t know if they’re interconnected as well as they should be?
There’s no integrated concept. There’s no focal point where you’d say that is our approach and everything ties back to that.
When we look at using all these different tools when needed: FLMA, RCA, what are the limitations when we have that ad hoc approach?
There’s lots of open questions and lots of opportunity for discussion yet, and lots of different ways of doing it as well. There are very few standards out there on how to do a criticality analysis. You can freely access the copy of the NORSOK standard for criticality analysis for maintenance purposes on the internet, but I’ll defy you to try and implement that. It’s not implementable. It sounds good as a PowerPoint solution, but once you try to apply it, it’s very difficult. Maybe the existing tools are not the right tools for the job, because it just brings too much discussion.
How do we calculate that discussion upfront when you’re developing your own internal standards?
Having the discussion upfront on a long-term doesn’t help anyway. Because after five years, the engineers have changed, or they need to do a review, and looking at the documentation from the previous work, no one can understand it. The complex assumptions and boundary conditions were not fully documented at that point. They almost start from scratch again. So even upfront discussion is not a sustainable method for making improvements.
How do we go about overcoming all these issues and gaps that we see?
It’s a question of what the right tool for the job is. There are different types of systems; simple systems, complex systems, characterized for example, by a stochastic behavior and chaotic systems. We need to find a balance between availability, production capacity and maintenance costs. Make an optimal decision in a complex system and essentially the right tool for the job. To make optimal decisions in a complex system, you need simulations i.e., your ‘S’, the solution system, which is essentially your model. It must be equally as complex as your problem system, such as the production plant.
Are those simulations part of like a system engineering package, or is it kind of independent to what we’re looking at?
On one hand we need simulation to make decisions, but on the other hand, we need a systems engineering approach. A systems engineering approach for myself is balancing the resources you have to achieve the optimum result for the business. And the optimum result for the business is related to the business goals. And safety as well if that’s in your task. Your job is to optimize the multi-dimensional performance vector of the whole production plant.
How do we combine those two different aspects then?
If we want to model our system, there are different ways we can start. We can do:
- A top-down approach
Where we say we make one black box model of the whole production system, based on, e.g., your production loss, accounting data for the last five years, how much you’ve produced, how many process production losses you had, which maintenance costs or other costs you had as well. If your plant’s been collecting this data in a good fashion, you can make a black box model of your entire production system in a short while which will estimate your production system behavior based on your historical experiences. It doesn’t let you make asset decisions, but it’s a basis for your further modeling activities.
2. A bottom-up approach
This is a phenomenological model of the asset with its failure, damage processes, and its maintenance tasks. And based on this, you can include this small sub model in your main model, and you can then very quickly have an estimation of the influence of this asset on your entire production system.
Where do we build this simulation?
The first tool you may be familiar with this Relias soft tool; the reliability block diagram model, and the viable module. This tool is specifically designed more for mechanical and electrical components, not so much for production plants, with supply chains and tankage and flows. There are other tools on the market which you can use to try and make a simulation of your production.
I designed a simulation tool for the needs of the business, and I designed it for engineers, but not for experts. That means that the model is developed just by dragging and dropping standard objects, essentially, which I provide. And with these objects, clicking them together and joining them together, doing some simple configurations, you can base basically built in very quickly, a good estimation of your production system behavior.
Your solution system needs to be equally as complex as the product as the problem system. We don’t need to make the model as complex as one might think to have stochastically robust outcomes.
What type of benefits do organizations typically connect specked with this new type of approach?
It’s the early days yet. But I have some experience implementing stuff in process plants. Two types of main improvements that you can expect the first time is that:
- Acid engineers start working with renewed enthusiasm on reliability improvements. They will see that it is the way to proceed, and it will enable them to do things that they couldn’t do before
- From a system engineering approach, it shows you where you need to apply your effort. The tool and the method will help you decide where to start and how to go about that in a systematic fashion, and to reap the benefits of that
- You could improve your production by maybe 1% or decrease your maintenance costs by 10%. Just taking some numbers, I think they’re reasonable because you’re optimizing the whole system
- The tool is not just made for experts. Different people can work together using the same tool and instantly make better decisions.
Where can organizations find out about this new approach?
On Linked in, and via our website rams-mentaught.com. Contact me via the details on my internet site. I’m also planning a two-day seminar where I will teach the basics of systems using my tool as a basis for that. That would be a good point for any companies who are interested in finding out more.
What type of challenges can they expect if they are going to use this approach?
When you start with such an approach and you start modeling your system, you will be requested to provide data, which maybe you haven’t started collecting before. I think that’s not a barrier because you can make good estimates of this data, but it’s also insightful because it makes you think about the important data you haven’t been worrying about. This method forces you to talk with your experts and get their estimate of what these values are.
What is the one thing you want our listeners to take away from the conversation today?
There’s an English proverb that says in the land of the blind, the one-eyed man is king. Listeners need to reflect on their own experiences and choose to be the one-eyed man. There’s no information for complex systems and that’s our production system.
Do you have any resources you want to share with our listeners?
I have a couple of small podcasts which I made myself that they could listen to which explain the concepts a little bit more in details.
Eruditio Links:
Andrew Kelleher Links:
Rooted In Reliability podcast is a proud member of Reliability.fm network. We encourage you to please rate and review this podcast on iTunes and Stitcher. It ensures the podcast stays relevant and is easy to find by like-minded professionals. It is only with your ratings and reviews that the Rooted In Reliability podcast can continue to grow. Thank you for providing the small but critical support for the Rooted In Reliability podcast!
Leave a Reply