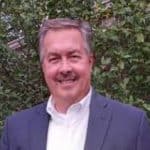
Smooth Transitions from Cooling to Heating with Mark Orlovsky
It’s my pleasure to welcome Mark Orlowski to the podcast. He is a quality warranty and service expert at Modine manufacturing company.
In this episode we covered:
- What is an HVAC system?
- How do you ensure that HVAC systems are operating at optimum efficiency?
- Now, if we’re doing all those basic things, what needs to be done when we’re moving from a cooling to a heating season, or maybe a heating season to a cooling season?
What is an HVAC system?
HVAC stands for heating ventilation and air conditioning.
How do you ensure that HVAC systems are operating at optimum efficiency?
The maintenance that’s required obviously depends upon how complicated the system is. I’d start out with things like filters, belt, belt tensions. What is often overlooked is cleanliness of coils. You need to consider the location that the equipment is in, how dirty it can get, then also understand how critical the application is.
Look at the overall inspection of the product, the cleanliness, look for things like the culminates of the coils. Make sure that all moving parts are properly lubricated, dampers and linkages operate correctly. Check electrical connections at least on an annual basis to make sure that everything is tight.
Now, if we’re doing all those basic things, what needs to be done when we’re moving from a cooling to a heating season, or maybe a heating season to a cooling season?
There are some pieces of the equipment that are designed to be able to change over quickly and depending upon what part of the country you’re in, you can be in heating in the morning, you’ll be cooling mid-day and then back and heating in the evening. Some of the equipment will move through those modes and are designed to do so. But there’s other equipment that needs a lot more attention to move into the heating season.
Document the process, record, and journal what you’ve learned from season to season. Go through a risk assessment of the most critical pieces of equipment. Have critical spares on site, depending upon how critical that piece of equipment is to the building operation or whatever process it involved with.
What type of spares do you typically recommend then?
If it’s an older piece of equipment, that’s critical. Something like a motor can render the piece of equipment useless. Some of the basic kinds include a pilot assembly or a flame sensor, those are ones that are, typical, as well as a pressure switch. The other piece that I think that often gets overlooked is when you have a gas fired piece of equipment, people typically don’t check gas pressure. Gas pressure is important and can cause problems either if it’s too low or too high. If it’s too low, you’re not going to be delivering the BTUs the heat to the space that you paid for. It’s too high that can reduce the life of the equipment.
Is there anything else that we overlook when we’re doing this?
I would say cleaning of condensate drain lines to make sure that they are flowing correctly. The other thing is the electrical connections, having loose or not tight electrical connections is responsible for all kinds of intermittent failures or problems, very hard to troubleshoot. Look at the system as a whole, I am a big believer in checklists.
Do we need to look at anything else or is it just run the air through its cycle?
At a minimum, run it through its cycle. Make sure that the units are on rate on gas ferret equipment. Get into the ins manual and validate that that equipment is on rate and that the setting of the gas pressure is correct for that piece of ventilation equipment. Check temperature, rise and airflow. Make sure that you’re getting the appropriate outdoor air that you plan for. Refrigerant pressures are critical for equipment that’s being on spec.
Are there any warning signs that organizations need to pay attention to?
Watch for things like nuisance trips of a switch. The other thing is to talk to the occupants; whoever’s using that piece of equipment or is being served by.
What is the one thing you want our listeners to take away from this conversation
I would say assessing equipment based on a risk. Go through and identify which pieces of equipment are the most critical to the operation. Spend more time on the more critical pieces of equipment.
Where can people find out more about you?
moldinghvac.com is a good resource. On that website, we’ve got a lot of information and articles for contractors and building owners engineers including that the PM checklist that we recommend. And I’m on LinkedIn.
Do you have any favorite resources that you want to share with our listeners?
There’s some good maintenance ideas and checklists on HVAC contract, director websites. Google and do some internet searches, some of the contractors have outstanding lists on HVAC manufacturer websites, and some good information for building owners’ contractors. Energystart.go is a good resource, and now they have some checklists as well. And recently I think I’ve even seen something in Forbes.
Eruditio Links:
Links:
Rooted In Reliability podcast is a proud member of Reliability.fm network. We encourage you to please rate and review this podcast on iTunes and Stitcher. It ensures the podcast stays relevant and is easy to find by like-minded professionals. It is only with your ratings and reviews that the Rooted In Reliability podcast can continue to grow. Thank you for providing the small but critical support for the Rooted In Reliability podcast!
Leave a Reply