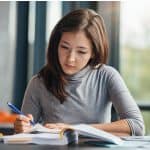
Selecting Which FMEAs to Do
FMEAs take time and cost money. They should be done when a certain level of risk can be effectively addressed by the FMEA procedure. Preliminary Risk Assessment is a procedure that uses company-determined criteria to select which FMEAs to do.
“The key is to schedule your priorities.” ― Steven Covey
Why is Preliminary Risk Assessment Important?
Short of doing FMEAs on all subsystems and components, which can be very expensive and time consuming, there needs to be a way to prioritize potential FMEA projects, to help identify which FMEAs to do. One way to do this prioritization is called Preliminary Risk Assessment.
What is Preliminary Risk Assessment
Preliminary Risk Assessment is a procedure to prioritize which FMEAs will be done as part of a new project. It assess the risk associated with subsystems or components (when performing Design FMEAs) or process steps (when performing Process FMEAs) against company-defined risk criteria.
How is Preliminary Risk Assessment Performed?
The following is a simple procedure for performing a Preliminary Risk Assessment:
1. Open up a spreadsheet. In the first column, for Design FMEAs, list the system hierarchy (subsystems and components). For Process FMEAs, list the process steps.
2. Across the top of the spreadsheet enter the company-specific risk criteria used to prioritize the risk of the subsystems and components. The company-specific risk criteria can be identified by the project team. Example below.
3. The next step is to rank each risk criteria for each row in the system hierarchy on a scale, such as high, medium, or low, or 1 to 3. In other words, assess the risk for each item in the system hierarchy (or the process hierarchy), according to the risk criteria.
4. The final step uses simple arithmetic to multiply the cells in each row to obtain a risk index number for each of the subsystems or components in the system hierarchy. This index can then be used as input to the FMEA selection decision.
What are examples of risk criteria
The following are examples of risk criteria for selecting FMEAs. Companies can and should use their own criteria.
1. Potential for safety issues (What is the degree of safety risk associated with the item?)
2. New technology (What is the degree of new technology being introduced with the item?)
3. New applications of existing technology (What is the degree of change being introduced with the item?)
4. History of significant field problems (What level of field problems has been associated with the item or similar items?)
5. Potential for important regulation issues (What level of government regulation is associated with the item?)
6. Supplier capability (What is the risk associated with the supplier of the item?)
Note: These risk criteria can and should be tailored to the circumstances of an individual company or organization and applied to each item in the Bill of Materials.
Example of Preliminary Risk Assessment
The following is a fictitious example of a Preliminary Risk Assessment for an all-terrain bicycle system.
In this example, only the subsystems are assessed; however, the same procedure can be used for selection of components. The results of the Preliminary Risk Assessment in this example point towards two subsystems: frame and hand brake.
FMEA Tip # 1
In many cases, specific changes to a design or manufacturing process are being considered. The nature of the proposed changes can be documented and becomes input to the preliminary risk assessment. This includes changes in design, material, manufacturer, supplier, supplier design or process, usage environment, interfaces, specifications, performance requirements, or any other changes.
FMEA Tip # 2
Preliminary risk assessment can be applied to Process FMEAs. Each of the steps in the process hierarchy (as documented in the process flow diagram) can be analyzed by the preliminary risk assessment procedure, the same as with Design FMEA.
FMEA Tip # 3
The company-specific risk criteria can include a weighting factor, if the company wishes to weight certain criteria more than others. Example is safety concerns.
Problem
You are asked to perform a Design FMEA on a new Bicycle Hand Brake subsystem. In addition to the Hand Brake subsystem DFMEA, you are considering which components may need FMEAs. In this example, the bicycle hand brake is made up of 4 components: brake lever, brake cable, brake pad and brake caliper.
The Preliminary Risk Assessment for the components of the Hand Brake Subsystem DFMEA follows:
How might you use this Preliminary Risk Assessment to select which FMEAs will be done?
Solution
The Preliminary Risk Assessment rating provides input to the project team to help select which FMEAs to perform. Based on this analysis, the highest rating for components of the hand brake subsystem is for the brake cable, followed by brake pads, brake lever and brake caliper. The All-Terrain project team can use this analysis as input to the decision on which FMEAs to do for the hand brake components. Other factors to consider include project budget, project timing, and whether the component is designed in-house or by a supplier. In this fictitious example, the All-Terrain team decided to do Design FMEAs on the hand brake subsystem (based on earlier Preliminary Risk Assessment for bicycle subsystems) and the brake cable (based on this analysis). Given time and resources, they may also add a Design FMEA on the brake pads.
FMEA Question
Reader
Is it recommended to get the design engineers themselves to perform an FMEA or should this job stay with specialists like reliability and safety engineers? For the design engineers it would cost time and keep them away from their normally time-critical design tasks, as they have to be trained first in FMEA tasks. On the other side, it would increase their insight in quality parameters like reliability and safety of their products and systems engineering.
I normally try to perform the FMEA myself applying interview techniques, but in smaller companies (subcontractors), FMEA work is performed by the design engineers themselves.
What is your recommendation?
Reply
Thanks for your question. I have three comments for your consideration.
First, in my experience, FMEAs should be performed by a team, not by an individual. Below is an excerpt from my book on the subject of FMEA teams:
One of the most important steps in preparing for an FMEA is selecting the right team because FMEA is a cross-functional team activity. Doing an FMEA by one person, or with an inadequate or incomplete team, is unacceptable and inevitably results in poor quality. There are three primary reasons for the necessity to have the correct team when doing an FMEA.
1. People have “blind spots.” A well-defined cross-functional team minimizes the errors inherent with “blind spots.”
2. The FMEA analysis requires subject-matter experts from a variety of disciplines to ensure incorporation of all necessary inputs into the exercise, and that the proper expertise is applied to the design or process being analyzed.
3. One of the indispensable values of an FMEA is the cross talk and synergy between subject-matter experts that occurs during the meetings. Well-defined groups can discover things that individuals often miss.
A typical core team for a System or Design FMEA might include representatives from system engineering, design engineering, manufacturing engineering, test engineering, field service, and quality or reliability. Large systems or subsystems may require more than one design representative. Supplier partners may be included for critical parts on a need to know basis.
A typical core team for a Process FMEA might include representatives from manufacturing engineering, plant assembly, product engineering, supplier quality, end-of-line test, maintenance, and quality or reliability.
In addition, the FMEA core team can invite other experts for specific topics during FMEA meetings, when their topic is being discussed.
Second, it is important to identify the roles and responsibilities for FMEA. Turning, again, to my book:
Companies vary widely in how they organize the functions of systems engineering, design engineering, quality, reliability, manufacturing, service and other departments that will provide representation to FMEA teams. There is no template defining the specific roles and responsibilities for carrying out the FMEA tasks, however, there are certain guidelines. FMEA needs the support of a reliability or quality “homeroom”, where the body of knowledge of FMEA is supported with standards, procedures, training, and facilitation. It is usually a good practice to make the design engineer responsible for accomplishing Design FMEAs and the process engineer responsible for accomplishing Process FMEAs, with the support of the skilled resources from the reliability or quality “homeroom.”
My preference is for a trained representative from the quality or reliability department to facilitate the FMEA, with design engineering owning the document. However, I’ve seen companies successfully implement FMEA with design engineering doing the facilitation, as long as the correct team is formed and trained, and the facilitator is trained in the skills of facilitation.
Third, FMEA teams should be trained based on the following guidelines:
FMEA team members need training in the basics of FMEAs before the FMEA team meetings begin. This can either be full team training by an expert in FMEA methods, or at minimum, the team needs a good overview of FMEA fundamentals. If the FMEA team is not familiar with the basics of FMEAs, such as procedure, definitions, examples, and lessons learned, then the meetings will be much longer than necessary and the results will be unsatisfactory.
At minimum, I recommend at least one person being well trained in the fundamentals of FMEA, and leading the effort. The FMEA team can then be trained in an overview of the fundamentals.
Next Article
FMEA procedure includes assessing three types of risk: severity, occurrence, and detection. In the next article, action strategies to reduce severity risk are discussed. Yes, it is possible to reduce the risk related to severity.
Leave a Reply