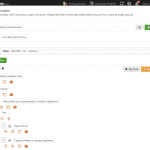
Equipment maintenance is a requisite for companies that seek high-performance from their physical assets. If they can leverage a well-executed maintenance strategy, such organizations should gain the expected advantages that reliable assets will deliver such as reductions in operational costs and unplanned shutdowns.
One of the oldest and most popular of maintenance strategies is Preventive maintenance where assets are maintained at regular intervals to lessen the likelihood of failure. Like other maintenance strategies, it is a dynamic process that begins with maintenance planning.
But, the process is useless without accurate and timely data. Data is inseparable from efficient maintenance management and it is the take-off point for maintenance planning. We discuss this further and the unique part that computerized maintenance software (CMMS) plays below.
The Preventive Maintenance Process
Preventive maintenance need not be complex as long as the best practices for implementation are followed. For a smooth flow of the process, here is an overview of the 5 major steps:
1) Identify Work
Decide the assets to include in the plan. These will typically be the company’s most critical assets. This is a thorough process that includes identifying:
- Machines with the most potential to disrupt production/organizational success.
- Equipment that requires regular maintenance.
- Equipment with high repair and replacement costs.
As you can imagine, CMMS is a perfect way to store all of this data for future use, as well as to ensure you are keeping accurate records.
2) Plan Work
Plan the specifics of the maintenance tasks for each asset. The details will include what to do, how often to do it, the spare parts to use, etc. Valuable sources for this information are manufacturers’ recommendations, information from each machine’s maintenance history (if you have kept any up to this point), and insight from technicians that worked on those assets in the past.
What is great about having a CMMS is that it gives you an easy way to store all of that data in one place. What’s more, in some CMMS systems, you can outline the work that needs to be done for a particular PM/Word Order (as seen on the picture below).
3) Schedule Work
Based on the information gathered so far, create a schedule that covers the following:
- Priority tasks with due dates. Start by establishing the maintenance intervals (annual, semi-annual, quarterly, etc) for high priority assets. Thereafter, lower priority assets can follow.
- Skills availability. Assign each task to a qualified technician.
- Materials availability. Check that all required materials and spare parts will be available at the scheduled periods.
- Communication and recording. Decide on how the information will be communicated within the team and how records will be kept.
Originally, CMMS system gained traction because they were able to successfully automate this whole process. While today they can do much more, this is still the main reason why many businesses opt-in for a CMMS.
4) Execute Work
Carry out all scheduled tasks when due and track them to monitor their progress till completion. It’s important to avoid deferred maintenance at this stage because continuously postponing repairs and services will eventually lead to emergencies and more of reactive maintenance.
If you are interested in much more in-depth advice on how to plan and execute an effective preventive maintenance plan, I highly recommend reading this preventive maintenance guide.
The Importance of Accurate Data for Maintenance Planning
If there is one thing that any maintenance plan cannot do without, it is accurate and timely data. This section delves into 3 key categories of data necessary for efficient preventive maintenance planning and the roles CMMS plays in each area.
1) Asset Register
Physically inspecting a facility and creating an inventory of all relevant equipment and assets is one of the most time-consuming aspects of preventive maintenance. However, this exercise cannot be avoided as it is the foundation for maintenance planning and it helps to ensure that preventive works are executed when due on every critical operational equipment.
CMMS and Asset Registers
Once this raw data is available, it is advisable to upload it into a CMMS. Among other things, a CMMS will help to:
- locate every asset
- access and navigate the asset register on-site or remotely
- easily update the register when required with new assets
When you have all of this data in your CMMS, you can be very precise with your planning, but you have to ensure that the data is always up-to-date. This means you have to enter accurate data and ensure your technicians are updating records as they conduct repairs.
Planning wise, having all of your assets into a CMMS lets you create an initial preventive maintenance plan to see the volume of preventive work you actually have to do on a daily, weekly, and monthly basis. You can also use this information to assign work more appropriately for each shift, as well as review if you possibly need to hire more people to do all of it on time.
2) Equipment History
Another category of vital data is equipment history. These come in the form of equipment maintenance logs that provide information like how much repairs and what kind of work has been done on a machine in the past.
They also reveal any limitations and other peculiarities of the asset. Equipment history enables maintenance teams to quickly narrow down any potential performance issues and thus make timely decisions to improve equipment reliability and prevent costly downtime.
CMMS and Equipment History
Using a CMMS for equipment history beats trying to store decades of paper records in the following ways:
- there’s less room for human error
- data can be accessed remotely
- keep and retrieve data faster and with less space than paper records
- several users can view the same information simultaneously
- it’s an admissible resource for regulatory audits
If you are in charge of creating a maintenance schedule, you can also use the equipment history in your CMMS to generate useful reports like:
- review how long do certain repairs take to complete on average – this helps you create a realistic time frame for repairs and enables you to create a more efficient (and fair) maintenance schedule
- review how your technicians perform and if some are better with one type of task than other – you can use this to either organize training or to assign work to technicians that are most suited for executing it
3) Spare Parts Inventory
Whether a company uses 100s of different spare parts or a few, managing them is important for preventive maintenance planning – repairs will simply not happen if the necessary parts are unavailable.
But, knowing what parts to stock and the quantity of each item to keep can be tricky and is what guarantees successful spare parts inventory management. This helps to reduce maintenance backlog caused by unavailable parts, reduce maintenance inventory costs, and reduce stockout.
Arriving at an ideal stock level is a combination of data from both the asset register and the equipment history. The asset register helps to establish the items to stock while the equipment history gives a better idea of the frequency of usage and the quantities to stock.
CMMS and Spare Parts Inventory
Spare parts inventory management can be challenging especially with regards to under- or over-stocking items. Integrating spare parts inventory with a CMMS helps to:
- analyze usage trends and set reorder levels,
- automate stock counting
- review how many spare parts are used for routine repairs – this helps you with forecasting spare parts demand and keep less inventory on hand
For example, if you use Limble, when creating a PM you can assign it the spare parts that are likely to be used for that process. When the technicians mark the PM as finished, the system will immediately subtract those spare parts from your inventory. In the interest of keeping your records highly accurate, the technicians can write in the number of actual spare parts used if it differs from the assigned value.
What this does for your maintenance planning efforts is that you can schedule PMs for months ahead, let CMMS calculate how many spare parts are likely to be spent during this period, and use that as a starting point for forecasting spare parts inventory demand.
Maintenance Planning and Reliability
Maintenance planning and reliability are obviously interconnected. One of the core goals of maintenance planning is to avoid machine failure by reducing – to the barest minimum – any conditions that will prevent it from performing a required function.
Furthermore, maintenance planning helps to extend equipment lifetime and reduces the frequency of service interruptions. Clearly, maintenance planning directly affects the system’s reliability – it ensures the right intervention at the right time. Too much maintenance intervention often results in higher maintenance costs and wasted parts while too little will reduce asset reliability.
Since one of the objectives of reliability engineering is to ensure uninterrupted asset uptime and minimize effects of asset failures on business operations, maintenance planning is an essential tool for creating a cost-effective, balanced, and reliable system.
Leave a Reply