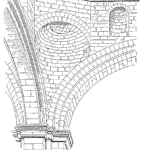
This article explains the operation of peristaltic (hose) pumps and gives twelve points to be aware of when using them.
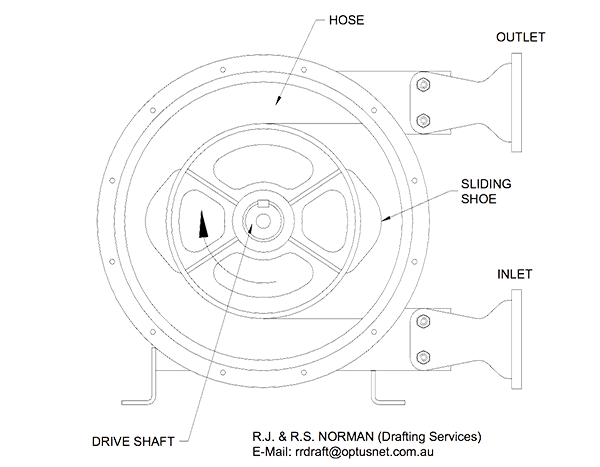
A peristaltic or hose pump consists of a rubber hose in a bath of lubricant, mounted on the inside of round track that is squeezed closed by revolving wheels or a sliding shoe. The squashed area moves around the hose and pushes the contents through it. Behind the moving squeezed area a vacuum is formed and draws in more of the contents being pumped. There usually are two squeeze points 180o apart and driven through a gearbox by a motor.
They were originally designed for pumping blood during hospital operations and mimicked the way the human body used its internal muscles to push fluids and pastes about. Figure 1 shows a simplified drawing of a peristaltic pump. The pumps come in small to large sizes but pumping volumes are low and subsequently, a big and expensive pump is needed for high flow rates.
Below are twelve issues to consider when using these pumps.
- They are a positive displacement pump and must always be allowed to discharge when in operation. If a downstream valve is closed the pump will deadhead and rupture the hose. You may need to fit a relief valve in the pipeline to protect the pump against over-pressure.
- Hose material compatibility with the chemical being pumped and the operating temperature is critical for long operating life. Tell the supplier the full range of chemicals being pumped and their temperatures. The ranges of rubbers for the hoses available are limited.
- Flush the pump out with water after use. Leaving the chemical sitting inside the hose for great lengths of time could cause deterioration of the hose rubber.
- They are expensive to maintain. The squeezing action stresses the rubber hose and it fails comparatively more often than other pump designs. In the large sizes, a hose can cost 20% of the pump price.
- They are not suited to continuous operation. The hose materials used have a limited working life and if the pump is run continuously this limit is soon reached.
- The hoses have limited ‘memory’ and eventually are squeezed out of shape and are not able to stay round and pumping efficiency drops.
- Rocks and pebbles rip the inside of the hose. Because the pumps suck strongly they make good sump pumps but will also draw in solids from the sump bottom. A coarse strainer needs to be fitted to the suction line.
- Sludge, slurries and high viscosity liquids are pumped easily and these pumps are versatile in the range of duties they can perform.
- Flakes of rubber working off the hose as it is squashed can contaminate the hose lubricant. When the hose does eventually rupture its contents leak into the lubricant and may cause other internal damage.
- Shim adjustment is critical for the hose to be properly squeezed for efficient operation. The positions of the shoes or revolving wheels that squeeze the hose are adjusted by shims. The shims must be set to just close the inside face of the rubber hose together without heavy compression. Use a pressure gauge on the suction side to set and check the shims.
- Big pumps are top heavy and if being transported on a truck they will fall over when going around a corner unless strapped down.
- They can be run dry but not forever. The hoses can be squashed while empty without immediate damage if valves are not closed. Solids trapped in the hose while dry-run will be embedded in the rubber.
Mike Sondalini – Maintenance Engineer
If you found this interesting, you may like the ebook Process Control Essentials.
Very nice article. Peristaltic (Hose) Pumps are rarely shown in technical publications
I’ve also come to notice peristaltic pumps aren’t exactly the royalty of chemical hose products. Mine got squeezed out of shape in record breaking time and was extremely heavy and clumsy to move around. Luckily better alternatives do exist.
Very informative. You Just made me a better operator
Also the higher the viscosity the less consistent the flow rate is. I use a peristaltic to pump polyurethane. The Part A has a high viscosity and the Part B has a lower viscosity close to water. The problem I have is the volume that is displaced by the Part A side is always dropping during the life of the tube. The Part B side drops initially when a new tube is used but then stays consistent. It seems to be worse the softer the tubing is.
what could be the reason for slow movement of a high viscosity liquid?, knowing that it was working so fast , could it be the gear box