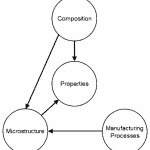
This article is the first in a series about material engineering and product reliability. The intent of the article is to provide you with a basic understanding of product reliability as viewed through the eyes of a material engineer. When I first talk to engineers who have a different background or focus, I start with the basics. As we speak more, I expand into relevant areas one at a time. That is what I hope to do with this series. Introduce you to some basics, and then move on to a deeper dive into the topic.
When considering product reliability, a materials engineer is concerned with how the materials in components respond when exposed to stressors that can cause the materials to degrade. Stressors include mechanical loads, corrosive environments, chemicals, heat and cold, electricity, and radiation. You may find additional stressors based on the environment components are used in, or how they are used. It’s a problem if a component or joint in a product degrades to the point where it stops functioning as required.
As a materials engineer, I am concerned with more than just product reliability. For product design, I must consider performance, reliability, and cost of components and joints. This means looking deeper than just how materials respond to stressors.
In this first article in the series, I will discuss the component and joint design process, the two pillars of product design, and a common approach to product design. There will also be a brief overview of materials engineering. Future articles will focus on reliability.
Finally, since I’m a metallurgical engineer my focus is on metals and coatings. Future articles will cover metals, but the discussion in this article applies to all materials – metals, polymers, ceramics, and new materials that don’t fit neatly into the three categories.
Product design
Companies try to design products that meet certain performance and reliability requirements at the lowest possible cost. Since any product is an assembly of components, whether this goal is achieved depends on each component meeting its performance and reliability requirements, and whether they can be fabricated at the lowest possible cost.
An example of the components in a product are the components in a bicycle crank.
Performance requirements describe the attributes a component must have to function as required. The attributes are described in terms of mechanical, electromagnetic, thermal, optical, physical, chemical, electrochemical, and cosmetic properties. For example, strength, electrical resistance, and mass. Performance requirements include mechanical loads that must be supported, electrical current that must be carried, and cosmetic appearance.
Reliability requirements describe the stressors to which a component will be exposed, the time length of exposure, and the expected response of the component’s materials. Examples of stressors cyclic stresses, wear, high temperatures, and salt water (corrosion). A component fails when the material degrades to the point where the component no longer functions as required.
The discussion also applies to weld, solder, and braze joints between components. But for ease of writing, the discussion will only mention components.
Two pillars of component performance, reliability, and cost
The performance, reliability, and cost of any component depend on two things:
- Component form. This includes component shape, dimensions, and features.
- Component materials. For metals, this includes alloy, process for making stock metal or fabricating a component, heat treatment, and coatings.
For any component, both form and materials can be engineered when a component is being designed. This includes making trade-offs between component form and materials to optimize its design to meet the performance and reliability requirements at the lowest possible cost.
Engineering the materials means considering different types and grades of materials, coatings, how stock materials (sheet, plate, powder,…) are produced, components fabrication process, and heat treating to achieve the desired properties and attributes in the component being designed
For example, consider a component machined from a steel bar. One option might be to use cold-drawn carbon steel to meet the mechanical requirements. Or, it might be possible to use hot-rolled alloy steel bar and heat treat the component after fabrication to get the desired mechanical properties. It’s also important to consider ease of machining, ease of heat treating, reliability, and cost when selecting the alloy, steel mill processing, fabrication, and heat treatment.
Common approach
However, engineering component form and materials does not happen at many companies. Instead, engineering teams focus on engineering component form, and to a large extent, overlook engineering the materials.
This happens because many companies don’t have materials engineering expertise on staff. Instead, mechanical engineers are expected also to be materials engineering experts. That’s not realistic. While they are good, capable engineers, they don’t have materials engineering training or experience, or the materials engineering perspective.
So, when designing a new product that is an iteration of a current product, designers often select the same metals used in the current product. If it’s a completely new product, design engineers often only consider and select materials familiar to them. In both cases, there can be problems if the performance and reliability requirements of the component being designed differ from past products, and the materials selected are not suitable for the new application.
The potential problems are component reliability issues that delay product launch and result in customer returns. Also, in both cases, since the options of materials considered is restricted, opportunities are missed to reduce costs and innovate better components by considering different materials.
What is materials engineering?
Materials engineering is the application of materials science to engineering decisions and problems. Materials science is concerned with the relationship between a material’s properties, its composition and microscopic structures, and the manufacturing processes used to make components, stock materials like metal bar or plastic sheet, and form joints between components. For metals, microscopic structures include grains and phases, both of which and have a big impact on metal properties. Just because they can’t be seen with the naked eye doesn’t mean they can be ignored.
Understanding materials science makes it possible to leverage it to engineer the materials used in components. As mentioned earlier, engineering the materials means considering different types and grades of materials, coatings, how stock materials (sheet, plate, powder,…) are produced, components fabrication process, and heat treating for the purpose of achieving the desired properties and attributes in the component being designed.
Fabrication and joining properties are also important
Keep in mind that properties related to performance and reliability are not the only important properties. Ease of fabrication and joining are also important. Selecting materials that make component fabrication difficult results in higher costs due to special handling and quality problems.
Leveraging materials engineering
Being able to leverage materials engineering enables design of products that meet performance and reliability requirements at low cost, and with fewer problems during product testing and manufacturing. Sometimes it results in designs not thought to be possible.
The next article will discuss component design and how materials engineering fits in.
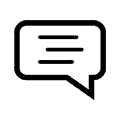
Thank you for starting the series on materials reliability. It needs updating. I have used Kececioglu’s Weibull fits for common materials, but that’s old, and Weibull may not be justified.
I have had a bicycle crank failure!
I look forward to more articles, because my next article will be on multivariate reliability models of the form P[Stress > strength] or P[g(Stress, strength) = fail] when stresses and strengths are multivariate, dependent vectors. I’m interested in load sharing and Miner’s rule.