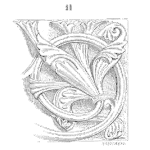
One approach for reliability improvement is to find the weaknesses or faults, then fix them.
This is best done before shipping to the customer.
You may hear this called the Test, Analyze, and Fix Method (TAAF). Or, you may have heard of it called a Reliability Growth Test program (RGT). Either way, the essence is evaluating prototypes to find specific faults.
These systems generally work when (according to O’Connor in Practical Reliability Engineering) when:
- All failures are analyzed and improvement action is taken in design or manufacture, as appropriate.
- All failures are tracked to the root cause.
- Take corrective action as quickly as possible.
There are many types of TAAF programs. Mil Hdbk 189 Military Handbook, Reliability Growth Management lists 17 possible models. A popular and effective model is the Duane Model.
Duane Model
Originally based on aircraft data analysis by James T. Duane (General Electric), the model of the cumulative failure rate fell close to a straight line when plotted on log-log paper.
This model is useful over the phases of a project during development.
The general formula is
$$ \large\displaystyle \frac{{{\theta }_{c}}}{{{\theta }_{o}}}={{\left( \frac{T}{{{T}_{o}}} \right)}^{\alpha }}$$
Where:
θc = The cumulative mean time between failure (MTBF) at the desired time.
θo = The cumulative MTBF at the beginning of the test period
α = The rate of MTBF growth
T = The desired test time or test time since the beginning of the test
To = The beginning test time
The instantaneous MTBF, θi is calculated given θc and α with
$$ \large\displaystyle {{\theta }_{i}}=\frac{{{\theta }_{c}}}{1-\alpha}$$
The value of α in the Duane model is never above 0.6. O’Connor provides a basic guideline to determine the appropriate value of α to use for project planning.
- 0.4 to 0.6 A top priority program to eliminate all failure modes. Immediate attention and correction action prevails.
- 0.3 to 0.4 An above average program on reliability improvement exists. No environmental testing. Action taken on important failure modes only.
- 0.2 to 0.3 Routine attention is paid to reliability improvement. No environmental testing. Action taken on important failure modes only.
- 0 to 0.2 A low priority for reliability improvement
Related:
Duane Plot of Cumulative Failures Over Time (article)
Sources of Reliability Data (article)
9 Reliability Growth Patterns for Two Test Phases (article)
thanks Fred!
following your post for an year now..
Really some really helpful info Shared.
-Sachin