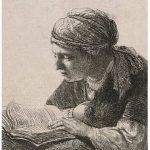
I am often asked for my opinion about the FMEA Handbook that was jointly published by AIAG and VDA in 2019. Here is a summary of my candid views on this handbook, excerpted from a presentation I gave at the 2019 Guangbin Yang Reliability Symposium.
What is AIAG – VDA FMEA Handbook?
AIAG is Automotive Industry Action Group. It was founded in 1982 by the three largest North American automotive OEMs. Over the years, AIAG created and maintained an FMEA standard for use in the North American automotive industry.
VDA was founded in December 1980 as a German quality management standard. VDA created and maintained an FMEA document for use in Germany and Europe.
AIAG approach to FMEA was different than VDA approach to FMEA.
Sometime prior to 2019, AIAG and VDA began working together to create a single “harmonized” approach to FMEA that was intended to be used in North America and Europe and beyond. It was published in 2019.
Points of Agreement
I’ll begin by saying we should all agree, successful FMEA implementation is a critical objective in industry. Aim for making FMEA highly effective, and not a “check-box.”
A few of the positive contributions made by the new AIAG & VDA FMEA Handbook:
- OEMs/suppliers have access to a common approach to FMEA, across continents
- Many FMEA concepts described in the Handbook are well written
- Alignment w/ ISO 26262. Example: FMEA-MSR *
- Concept of Action Priority attempts to resolve flaws with RPN
* MSR is Monitoring and System Response
Significant Concerns
Unnecessary Complexity
Proper approach: FMEA procedure and format should be as simple as possible. New or updated standards or handbooks should not add complexity.
Why? Complexity consumes valuable time and reduces effectiveness. Critical issues can be missed.
Concerns:
- The FMEA Handbook adds considerable new terminology and other complexities.
- Performing FMEA with use of Excel spreadsheet is very cumbersome.
- Complexity can obscure higher-risk issues (“missing the forest for the trees”)
Resource Intensive
Proper approach: FMEAs should be as streamlined as possible, ensuring no higher-risk issues are missed.
Why? FMEAs need to be implemented in a way that supports product development process and allows teams to spend valuable time on most important issues.
Concerns:
- FMEA Handbook consumes valuable time on potentially lower-risk tasks.
- Use of AIAG/VDA friendly software requires dedicated administrative support.
Enforced Hierarchical Chain
Proper approach: FMEA procedure should focus on targeted areas of risk.
Why? FMEAs take time and cost money. They should be done when a certain level of risk can be effectively addressed by FMEA procedure.
Concerns:
- FMEA handbook enforces function and failure networks, which can lead to overly large FMEAs and unnecessary work. There are “work-arounds,” but you shouldn’t need to use “work arounds.”
- Example: enforcing causes at next lower level can miss important causes.
Wrong Sequence
Proper approach: An FMEA Recommended Practice or Standard should be developed or updated first. An FMEA Reference Manual or Handbook should follow the standard. In the past, SAE J1739 (published as an FMEA Recommended Practice or Standard) was published prior to AIAG (published as an FMEA Reference Manual).
Why? An FMEA standard outlines what must be done. An FMEA Handbook shows how to do what must be done.
Concerns:
- Getting the proverbial “cart before the horse” (wrong sequence) can result in sub-optimization. When that happens, the FMEA Handbook is not guided by a best-practice standard.
Inadequate Focus on Interfaces
Proper approach: Including all higher-risk interfaces in scope of FMEA is crucial to successful FMEA application.
Why? More that 50% of problems occur at the interfaces.
Concerns:
- FMEA Handbook does an inadequate job of clearly identifying high-risk interfaces and ensuring interface risk is reduced to acceptable level.
PFMEA Issues
Proper approach: Process FMEA procedure needs to be properly linked to Process Flow Diagram, Process Control Plan, and corresponding Work Instructions.
Why? Potential manufacturing or assembly deficiencies are identified and controlled through these linkages.
Concerns:
- FMEA Handbook is deficient in linking Process Flow Diagram, Process FMEA, Process Control Plan, and Work Instructions.
- Insufficient guidance on application of significant characteristics.
- Enforced causes at next lower level can miss important process causes.
A word about Harmonization
Much of the effort to integrate the approaches from AIAG and VDA was done in the name of “harmonization.” Although this can be a noble goal, there are potential downsides.
Harmonization makes sense when the differences between the two approaches are not significant, and when the process being harmonized would become more effective for company or user.
- Example: early versions of AIAG and SAE J1739
Harmonization or alignment does not make sense when the differences between the two approaches are significant, and when the process being harmonized would become less effective for company or user.
- Example: areas of significant concern in this presentation
Summary
Effective FMEA implementation is critical to safe, reliable and economical products. The new AIAG/VDA FMEA Handbook, although providing some positives, adds unnecessary complexity to FMEA applications, and is not best practice in certain areas.
My opinion: impact on North American Auto Industry may be a reduction in overall FMEA effectiveness.
My focus is to support SAE J1739 to be the best possible FMEA standard.
Next Article
The next article will address a series of reader questions on FMEA Detection.
Dear mister Carlson,
I’ve read your interesting review of the AIAG/VDA FMEA manual and must agree with most of your comments. I see lots of hesitation at OEM’s to fully implement the new approach. Do you believe it will survive or rather be adapted?
Kind Regards
Hi Patrick,
I appreciate your comments on the AIAG/VDA article. The hesitation from OEMs is understandable. I wish I knew the answer to your questions. I know that automotive engineers want to do a good job on products and processes, and FMEA is crucial to that goal. My view is that automotive companies should take a hard look at SAE J1739 as an alternative. It is leaner and more effective in my opinion.
Carl
Dear Carl.
I fully agreeded with most of your valued comments. SAE J1739 is more suitable tool from engineering eyes.
regards
Mark
Great post Carl.
Thanks, Francisco. Glad you liked it.
Carl
Hi Carlson,
Since I am new to fmea topic I want to know whether fmea is 5 step for rpn methodology and it is 7 step for ACTION PRIROTY ..Please correct my question
Hi Ram Kumar,
Thanks for your question.
As you can see from the article “Reviewing AIAG/VDA FMEA Handbook,” I believe there are many shortcomings to the AIAG/VDA approach. I prefer the SAE J1739:2021 standard, which outlines a six-step process. These FMEA process steps are the same regardless of whether you are using RPN or Action Priority. I prefer Action Priority to RPN, as it accounts for all combinations of S, O, and D. If you use RPN, you must address high-severity regardless of RPN value.
Please feel free to ask any follow-up questions.
Carl