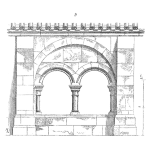
The technician explained it to me like this: “The part costs only $5, but I need to disassemble other stuff to get to it, so my labor charge will be $300. But don’t worry, I replace lots of these.”
Many of us have experienced the sticker shock of a routine service on a vehicle or home appliance. But ease of service is also a challenge with completion and intervention tools. Good serviceability is essential since many of these tools are reusable, must withstand high tension, torque and pressures, and operate reliably and safely under difficult downhole conditions.
There are negative outcomes for any downhole tool that is difficult to service, such as:
- Skipping or delaying a recommended service
- Skipping service steps or performing them below standard.
- Safety incidents that result from inadequate or complicated service instructions.

(component value USD 55)
requires USD 100s in shop labor
Each of these leads to higher costs for servicing and reduced reliability. And high-value safety incidents can involve human injury or fatality. But focusing on serviceability during design leads to lower cost, higher reliability, and greater safety.
In general, engineering teams can improve serviceability by:
- Identifying repair components vs. consumables
- Providing recommended replacement intervals
- Locating consumable components for easy access
- Identifying preferred tools for service and repair
- Creating simple and straightforward service processes
- Creating post-service tests and acceptance criteria.
As with margin and survivability, a thorough discussion of serviceability requires more than one page. But humans perform product servicing which is often taken for granted. Service processes must enable humans to perform service in a way that is economical, safe and leads to product reliability. All are achieved when serviceability is given priority during design.
TRUTH: Design teams are uniquely qualified to drive optimal serviceability.
This is the 6th of six articles on Design for Reality for downhole tools and systems.
Leave a Reply