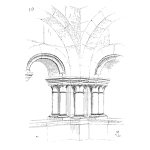
The wellsite is 200 miles offshore, and based on experience with the application, your team is confident about reliability. But will the downhole tool survive the journey to setting depth?
OEMs validate their downhole tools to operate within specification, but downhole tools must frequently survive poor casing conditions, tortuous well paths, unplanned corrosive events, and rough handling on the rig, as well as other inputs. These are variables that are hard to replicate under laboratory conditions. To compensate, engineers may “over design” the product. But does this really give the product survivability?
The solution is different for each product, but the bottom line is that the product must be tolerant of mis-use. FRACAS programs can inform on the possibilities for mis-use with historical application data, and DfR programs can guide engineers on designing for reliability. But the following will improve reliability and survivability in any downhole tool:
- Design with margin for all application parameters.
- Use thicker cross-sections at critical bending locations.
- Avoid excessive bending of long tools during handling by specifying hoisting points and fixtures.
- Do not ignore Young’s modulus – elastic deflection can be a failure mode in hydrostatically operated tools.
- Account for low temperature limits as well as elevated temperature limits on elastomeric seals.
- Understand 3rd party component ratings – for example, rupture disks should have a safe margin between operating pressure and rupture pressure.
As with margin, a thorough discussion of survivability requires far more than one page. However, designing with survivability in mind should be an institutional best practice for OEMs providing products for critical downhole applications.
TRUTH: One cannot design for the unknown, but products can survive the known.
This is the 5th of six articles on Design for Reality for downhole tools and systems.
Leave a Reply