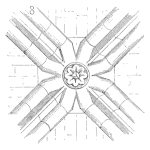
I got a call last week from a friend I used to work with who called just to catch up on what I had going on in life. After a few minutes of conversation on what each of us had going on he asked me what I thought of the phrase “Precision Maintenance.”
I must admit, I was a bit confused by the question. I told him I think a lack of precision maintenance might me the leading cause of failure for nearly every company in the world. I don’t think we spend nearly enough time training and certifying tradespeople in precision maintenance techniques and that the reduction in skilled trades apprentice programs has made the problem worse.
It was right then that he interrupted me by saying; “Let me clarify my question; shouldn’t all maintenance be precision maintenance? Shouldn’t we just insist any and all maintenance be done with precision? It’s like we’re trying to say you only need to apply maintenance correctly when you’re aligning a rotating asset or assembling a flange when all of our work should be done with precision. To me it seems like someone who failed to train their tradespeople and never had to align a set of sheaves suddenly came to the realization that if you don’t do it right it’s not going to last as long so now we need a precision maintenance task. No, you need to train your people, so they know how to properly install and maintain your equipment. Isn’t this the real cause?”
He wasn’t done….
“Think about this, I have performed vibration analysis for nearly 100 companies, and I had maybe a dozen who would have me come in to specifically perform vibration analysis on rotating assets that had just been reinstalled to verify alignment. With those companies, it was rare for me to find an alignment issue. When I did it was typically temperature related where the alignment was performed cold and when the system heated up the alignment changed. In nearly all of those cases, the tradesperson who performed that alignment learned how to compensate for the thermal expansion. At the companies who didn’t have me come in, more than 40% of their assets were found to be misaligned at the first reading and it was rare for them to shut the asset down to make corrections. They just lived with the fact that some of their people were incapable of or ignorant when it came to performing a proper alignment. So here they work for a company that gives them one chance to get it right and the data clearly shows they don’t have the capability to do so.
When we worked together 30 years ago, no one ever used the phrase precision maintenance. We were all taught how to do the job the right way and as apprentices most of the Journeymen we worked with insisted that we always work with precision. Those we worked with who didn’t were looked down upon and called hacks or butchers. So, when I hear the term “Precision Maintenance” it tells me I’m working with someone who thinks working with precision only applies to part of what we do instead of everything we do. I’ll finish my rant by saying, the day I go on LinkedIn and see some Hospital Administrator talking about “Precision Surgery” you can bet I’ll be avoiding that place!”
Those who know me know when I go silent, I’m in deep thought, and as I thought about what I just heard I was once again interrupted; “I whish I was there to see your face! You use that term all the time!”
I don’t thing my reply was what my friend expected to hear. “You’re right I do talk about Precision Maintenance a lot. I in fact attempt to teach all my customers that the vast majority of their failures start with the design and installation of their assets. That a lack of precision in how we perform our work results in failures that have a huge impact on reliability and asset lifecycle costs. But what you said is without a doubt 100% correct. Better yet, you made me think or rethink how we use this term in our community.”
Good friends share laughs and talk about old times. Great friends do that and then ask difficult questions to challenge how we think.
As always, I’m interested in your thoughts and comments! Enjoy!
Douglas Plucknette is the creator of RCM Blitz™, the author of Reliability Centered Maintenance using RCM Blitz™ and Co-Author of Clean, Green and Reliable a best-selling book on how to reduce energy consumption in manufacturing plants through equipment reliability. Doug has published over 100 articles on Maintenance and Reliability, and has been a featured Speaker as well as Keynote Speaker at a countless number of conferences around the world.
Leave a Reply