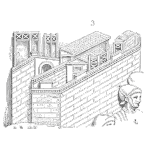
We have statistics to describe the variation that occurs in our world. Statistics is the language of variation.
If each of your produced products were identical in every way to all products produced, with no variability, we wouldn’t be concerned with the effect of variation on the performance and reliability of our designs.
Yet, variation does happen and we have a range of tools to identify and minimize the naturally occurring variation.
One of the roles of a reliability engineer is to identify and minimize variation that increases the probability of failure.
Let’s look at a generic manufacturing process to identify the various sources of variation that occurs.
Total process spread – is the accumulated variations from all sources.
Lot to lot variation – is the differences that occur from one batch of material or processing to the next. The equipment we use, the raw materials, and processing conditions are all different for each lot, even when everything else is the same, lot to lot variation reflects the variation of the incoming materials and stability of the process.
Stream to stream variation – is the differences that occur from one process stream (sequence of equipment or tools) to the next. Even in the same factory with two production lines of the same equipment models and process steps will produce products that are consistently different. Even factors like the different in temperature and humidity due to different physical location may be sufficient to cause the variation. Also, the differences in equipment and processing between the two lines contribute to stream to stream variation.
Time to time variation – reflects the difference over time. This is within or between lots, or within or between streams, just time will change equipment. Daily or seasonal variations in temperature may be sufficient to cause changes. Also, consider the physical changes to equipment over time (wear, corrosion, etc.) along with changes in how the people change (experience, attention, etc.) as it impacts product consistency.
Piece to piece variation – Even controlling or minimizing all the above sources of variability no two items, even produced one right after the other on a production line, are the same. They have physically different material as a minimum, yet often do exhibit a range of variations that may include welding joint strength differences due to slight changes in material, changes in coatings, due to small differences in surface contamination or material roughness, etc.
Within piece variability – captures the variation across the product. For example, the coating on a steel tube may vary in thickness along the length of the tube. The steel also varies along the length in thickness, composition, and strength, for example. Very few materials have absolutely uniform material properties over the area or volume used in products, while often an acceptably small variation, it sometimes becomes important.
Inherent error of measurement – in order to detect differences we make measurements. Measurement error includes both human and equipment components and left uncontrolled may dominate the sources of variability. Often measurements actually change the product being measured, thus there is a variation from measurement to measurement due to physical changes caused by the measurement. Considering and minimizing measurement error (and damage) is a great starting point to then focus on which next source of variability to improve next.
Variation happens and it’s with an understanding of the sources of variation along with adequate measurement techniques that we can work to create products consistently and avoid product failures.
Related:
Why do statistical based testing? (article)
Special and Common Causes of Process Variation (article)
Nelson Funnel Experiment (article)
Leave a Reply