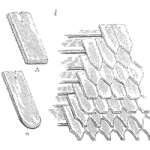
As stated before, variation happens.
The root cause of the variation for a stable process includes material, environmental, equipment, and so on, changes that occur during the process. No saw cuts the same length of material twice – look close enough there is some difference.
The difference between a stable and unstable process is the occurrence of special causes. A stable process has a predictable range of resulting dimensions and the variation is due to the inherent variability of the materials, machines, etc.
An unstable process experiences special causes. These are unique events which shift the process mean and/or increase the process standard deviation. Special causes may include using the wrong material, altering equipment settings or alignment, or even an increase in measurement error by using a damaged gauge.
Accidents, errors, mistakes, drift, wear, inattention, etc. all may lead to a change in the otherwise stable results of a process.
Special Causes
We notice some special causes even without control chart monitor. If we track scrap or failure rates we may notice spikes in the rate indicating something has gone wrong.
The red circles indicate a signal that something is causing a deviation from normal. Often a team converges on the issue to identify and resolve the problem. This reactive approach missing one of the key benefits of control chart monitoring.
A control chart doesn’t eliminate the occurrence of special causes. It does shorten the time to detect the occurrence of special causes thus reducing scrap and the time necessary to resolve or remove the causes. Control charts are often located at one or more stations within a process thus closer to the likely source of the change. This enhances the ability to find the source of variation.
Special causes may also dramatically reduce scrap or failure rates. These events indicate an opportunity to improve the process.
Like adverse events, it takes investigation and understanding of the contributing factors so the process improvements remain in place and create a better and stable process.
Common Causes
A stable process may have a high scrap rate. And the process may not reveal beneficial special causes to prompt scrap rate reductions. In this case, the control chart may not provide what changes will cause improvements.
Common causes of variation create the predictable range of readings seen from a stable process. A team focused on improving a stable process may need to investigate a wide range of possible causes before recommending ways to reduce variation or shift the mean to minimize scrap.
Tools such as a cause-and-effect diagram, fishbone diagram, or brainstorming will help identify potential causes. Then it may be simple experimentation, hypothesis testing, to determine if a change is effective or not. For more complicated combinations of causes and changes, the team may employ a design of experiments approach.
The changes may require different materials, equipment, procedures, or other systemic changes to realize improvements.
Dr. Deming suggests that 94% of all problems are due to common causes of variation. By focusing on reducing variation from the range of possible sources the process will produce fewer failures.
Making fundamental changes in design, materials, equipment and so on may require significant resources to accomplish, thus requires management support.
Related:
Sources of Variation (article)
Nelson Funnel Experiment (article)
Process Capability (article)
a good point!
Hello Everyone,
Can anyone please direct me to question banks for the CRE. I have been preparing for few months and want to evaluate myself now. If you have a simulator or question bank, I would highly appreciate if you could share it with me.
Thanks
Hi Ria,
Try asq.org and search for CRE – they have a 75 sample exam that you can take online or download and take. From what I understand it’s a bit tougher than the actual exam. Your mileage may vary.
Cheers,
Fred