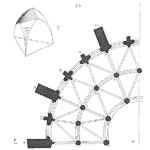
This article covers the operation of steam traps and how they work. Steam is a greatly used medium. Its use ranges from heating process and domestic fluids through to driving turbines by the expansion of the vapour. Yet the steam trap at the bottom of a drop leg is easily forgotten.
Stream Trap Operation
During distribution throughout a plant, steam vapour cools down on pipe walls to become hot, distilled water (condensate). It pools in the bottom of piping and if not removed it builds-up, filling pipelines and stopping steam flow and heat transfer. Condensate must be drained away from steam lines. Installing collection pockets with drop- pipes throughout the distribution system does this. At the bottom of the drop-pipe is fitted a steam trap. The trap discharges hot condensate until steam arrives, at which point it shuts and awaits accumulation of more condensate.
The simplest (but least effective) steam trap is an orifice plate. This is a small hole, about 1 – 1.5-mm diameter in 3- mm thick sheet metal put between flanges. Figure No. 1 shows the orifice plate in use as a steam trap. The orifice plate forces the condensate to pool. It must then flow through the small orifice before discharging into near- atmospheric pressure in the condensate recovery piping.
The orifice plate works in two ways. When the condensate load is heavy it collects and backs-up. The hot water cools and the steam pressure slowly forces the condensate out. If the water collected has cooled to below 100o C it drains out as a stream of water. If instead the condensate load reduces, there is less time to back-up and cool. In this case hot, high- pressure condensate enters the hole at more than 100o C and flows into a pipe that is at near atmospheric pressure. Water at atmospheric pressure boils at 100o C. The very hot water flashes-off into steam, which expands to take-up more space and chokes the flow through the hole. The condensate collects and repeats the cycle.
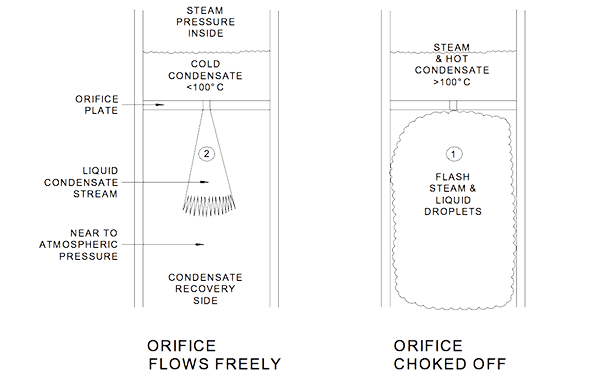
Stream Trap Types
A steam trap serves the same purpose as the orifice plate but regulates the flow by stopping the steam with the use of a valve. They function as an automatic valve that is closed to steam but opens when condensate is present. A secondary important benefit of some designs is their ability to also vent-off air and gases trapped in the steam piping. Steam traps use one of three principles to operate.
- Thermostatic steam traps sense the temperature difference between the cooled condensate and the steam temperature. They can be either a fluid filled balloon (usually alcohol) which expands as the temperature rises and moves a valve onto its seat to stop flow, or a bi- metallic lever where the different thermal growth rates of dissimilar metals move a plug on and off its seat.
- Mechanical steam traps sense the change in phase density between liquid condensate and the vapourous steam. These traps connect an internal valve to a float. As the float rises in a float trap or the bucket falls in a bucket trap, the valve opens and condensate discharges. Steam vapour arriving in the trap changes the buoyancy and the opposite motion occurs and shuts the valve.
- Thermodynamic steam traps sense the difference in dynamic (changing) pressures between both sides of an internal valve. These steam traps use the presence of the steam vapour to shut off. An expanding vapour discharges at high velocity. This high velocity creates a low pressure on the inlet side of the valve and the higher pressure on the outlet forces the valve closed.
Stream Trap Selection
Choice of a steam trap depends on –
- the size of the internal valve orifice for discharge,
- the temperature and pressure of the liquid condensate,
- the available difference in pressure across the trap,
- whether incondensable air/gas will be present,
- the cleanliness of the distribution system,
- the cost of the available options,
- the required longevity (life) between failures.
A steam trap installation requires a strainer up-stream as well as a way to prove the trap’s operation.
Is The Stream Trap Working?
It is vitally important that every steam trap in the piping system is operating properly. Steam traps need to be checked at least every six months and their operation proven. Traps can stop working because of –
- dirt in valve orifices (always fit a strainer up-stream)
- steam and air locks (pipes should fall steeply all the way to the trap and the gases vented off at the high points)
- high back pressure in condensate lines (blockages or use of a too small diameter pipe)
- water hammer or freezing destroying trap internals
- group trapping (one trap is used to remove water build- up in more than one drop leg. Unequal pressures develop and water is held-up in the low-pressure legs).
Fortunately all properly working traps will force condensate to collect upstream and then discharge it. This means we need only detect the build-back of condensate and its removal to confirm the trap’s operation.
To observe a trap’s operation a sight glass fitted one (1) meter downstream is ideal. Look for the ebb and flow of condensate passing the glass port. An alternative to using a sight glass is to install a bleed point down stream of the trap that can be opened to observe the flow characteristics. On float traps under heavy condensate loads it maybe necessary to cutback the flow by partly closing an up-steam valve to give it time to operate. Open the valve up after the test.
There are also electronic devices available such as acoustic meters and temperature pyrometers that can be used externally. The acoustic sensor permits listening to the internal noises while the pyrometer is used to observe the pipe wall temperature at the up-stream entry. If the trap is working properly the pipe wall temperature will fall as the condensate cools down and then get hotter as steam replaces the drained off condensate.
Mike Sondalini – Maintenance Engineer
If you found this interesting, you may like the ebook Process Control Essentials.
Leave a Reply