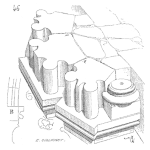
Co-authored by Mike Vella and Ray Harkins
Leaders often initiate change. They are expected to develop a vision for their organization (what we want to become) and create a mission (how we are going to get there). This implies that leaders are dissatisfied with the current state and are motivated to work towards a better future.
Change may be called a “transition” or “movement.” It could be considered evolution or revolution. It might come in the form of a new product or a better way of doing things. Whatever it’s called, change is everywhere and occurs frequently. When change offers greater value, we welcome it and call it progress. But when it results in delays, higher costs, loss of freedom, security, or comfort, it’s painful. As a leader, you have likely been part of initiating change or resisting it. Unless you choose to live outside society, change is the only constant.
We’ve all experienced cultural change. Examples include changes in communication technology (phones and computers), changes in government and political leadership, and changes in business, religious, civic, and charitable organizations. Reflecting on the global pandemic, consider how much had to change to manage our families, finances, transportation, entertainment, and business methods. It seemed that everything was subject to change. Surviving COVID taught us that businesses, governments, economies, and organizations of every type found ways to adapt to the rapidly shifting environment.
Acknowledging the nature of change is one thing, but being challenged as a leader to successfully create change is another. While charging forward with energy and passion may be one approach, there are others. History shows how difficult change is to implement, even when the benefits seem obvious.
Dr. Everett Rodgers, in his book “Diffusion of Innovation,” describes his research on change management. He gives a striking example. Medical science teaches that scurvy, caused by a deficiency of vitamin C, leads to symptoms such as fatigue, swollen gums, joint pain, and anemia. Although we may think of scurvy as an ancient disease associated with sea voyages, today it is most seen in populations with poor diets. The search for a scurvy prevention started over six hundred years ago. In 1497, Vasco de Gama lost 100 of his 160-crew to scurvy. In 1601, English Navy Captain James Lancaster successfully conducted sea-going experiments to evaluate the effectiveness of lemon juice (citrus) for scurvy prevention. English Navy Physician James Lind confirmed Lancaster’s results in 1747. However, it took until 1795 for the British Navy to adopt Lind’s work and confirm citrus as a scurvy prevention. Another seventy years passed before the British Board of Trade adopted this innovative change in 1865. Altogether, a cultural change to add citrus as a scurvy prevention took 264 years.
As a leader, making positive change is challenging and consumes time and energy. The good news is that Rogers’ work provides a process that improves the rate and increases the probability of achieving the desired change.
One of the most interesting elements of Rogers’ work is the “Distribution of Innovativeness” model.
This model explains that people are attracted to change based on their nature and ability to absorb risk. In terms of leading change, two major considerations arise. First, a change agent’s appeal for change will not resonate evenly with the entire population. Those most receptive are the Innovators and Early Adopters. Those least receptive are the Late Majority and Laggards. Rogers teaches leaders to focus their efforts on those naturally receptive to change and let them carry the message to others. Secondly, Rogers provides eight keys to the Diffusion of Innovation:
- Target Innovators and Early Adopters: Carefully select the change team and where they will concentrate their efforts first. This is time well spent.
- Utilize Specialized Channels of Communication: Change agents will be most successful if they represent those they wish to influence.
- Focus on Innovators and Early Adopters: Ensure adequate time and money for travel, communication, experimentation, and training.
- Create Slack for Change: Prepare for variances in time and money needed for the change. Expect the unexpected.
- Invest in Early Adopters: Plan how you’ll invest in the most important part of this process—your people.
- Make Early Innovator Activity Visible: Timing and results matter. Communicate your plan and illustrate its progress.
- Trust and Enable Reinvention: If results matter most, praise and support small changes to the plan and its execution.
- Lead by Example: You are the most visible part of the change. Commit to following the lead that you’ve set.
As a leader, you will inevitably encounter the need for change. By leveraging Rogers’ model and focusing on key principles, you can navigate the complexities of change more effectively, fostering a smoother transition and achieving your goals with greater efficiency. Embracing this structured approach will not only reduce stress and costs but also pave the way for lasting, positive transformation within your organization.
Ray Harkins is the General Manager of Lexington Technologies in Lexington, North Carolina. He earned his Master of Science from Rochester Institute of Technology and his Master of Business Administration from Youngstown State University. He also teaches manufacturing and business-related skills such as Quality Engineering Statistics,Reliability Engineering Statistics, Failure Modes and Effects Analysis (FMEA), and Root Cause Analysis and the 8D Corrective Action Process through the online learning platform, Udemy. He can be reached via LinkedIn at linkedin.com/in/ray-harkins or by email at the.mfg.acad@gmail.com.
Mike Vella is a retired quality and operations leader, most recently serving as Senior VP Operations at the Suter Company and prior, Vice President and General Manager of TI Automotive’s Brake and Fuel Group in North America. Mike was with TI Automotive for 30 years. Mike received his MBA from Wayne State University and his BS from Western Michigan University. His contributions to the Manufacturing Academy include training courses focused on leadership, quality, problem solving and statical analysis.
Leave a Reply