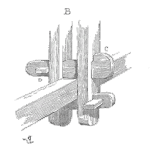
In part two of this three-part article series, I am continuing to showcase some of the best questions I’ve received over the past 5 years from students of my online Root Cause Analysis class, along with my answer to them.
And as Indira Gandhi once said, “The power to question is the basis of all human progress.” And so, it is my hope that by sharing these questions and answers, others may all learn and progress as well.
Hello Mr.Harkins,
I am really enjoying the course so far, thanks for sharing this knowledge. One question, how to apply the Containment Response for a service instead of product, especially when the problem is not directly related with part malfunction but with human action? For example, in the airline industry, how can you “stop the bleeding” if the occurrences came from human mistakes or behavior, which only can be completely solved by further retraining? Or in order industries, if the defect was caused by an operator who did not configurate properly his tools, etc.?
If we think black and white and consider that humans are one gear of the system, should the staff replacement be an option? Thank you!
Hello Ricardo,
Great question. Containment has to do with cleaning up the immediate mess, knowing that if you don’t apply a corrective action, you will have another similar mess soon. As you saw in the class, containment for product issues involves sorting, inspecting, returning/replacing, etc.
In the airline industry for example, if a flight was overbooked and I lost my seat, the containment to my complaint would likely include a free ticket on the next flight, food coupons, a hotel room, etc. The airline would try to fix my specific problem at a cost. But that containment action has nothing to do with why my seat wasn’t available. And in fact, if they don’t seek out the answer to that and subsequent questions, they will give out a bunch of hotel rooms and free tickets.
I hope that helps separate the idea of containment. Root cause analysis principles still very much apply in human-driven work environments.
Hello Ray,
I am trying to understand hypothesis testing and how important it is? And can you share any relevant information in-depth for that?
Hello Pramond … So good to hear from you. Congratulations on completing the 8D course. You are obviously eager to learn about quality.
Hypothesis testing is remarkably important, not just in quality and reliability, but throughout the sciences. In medicine for instance, doctors will test a new drug against a “placebo” using hypothesis testing. The reaction of the placebo-controlled group serves as a baseline when looking at the efficacy of a drug. The response of the patients taking the experimental drug is compared to the patients taking the placebo using hypothesis testing.
In education, a high school principal may use hypothesis testing to compare different teaching methods by examining the test scores of the student. Hypothesis testing is useful there.
In quality, you may want to compare the defects produced in different processes. Again, hypothesis testing will help tremendously.
I didn’t add hypothesis testing to the RCA class because I didn’t think it exactly fit. It is related of course, but hypothesis testing is generally regarded as a more advanced topic. I was thinking about assembling a DOE class and a Quality Engineering Statistics class at some point in the future. This would be a good topic in either.
In the meantime, I would recommend checking out a college level statistics textbook. It will certainly teach hypothesis testing.
Hi Ray,
The company I am with now is most interested in the Cost of Poor Quality. What is the best way to adapt my COQ model to account only for COPQ. Thanks, Derek
Hello Derek,Great hearing from you. Well … Cost of Quality (COQ) is comprised of four categories: preventive, appraisal, internal and external. And only the second two categories — internal and external — involve product defects, or poor quality. Preventive and appraisal are costs incurred before a defect is found. So to answer your question, you could adapt the COQ model for COPQ simply by removing the costs associated with the preventive and appraisal costs.
Leave a Reply