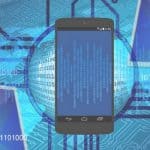
Want to achieve a worthwhile return-on-investment (ROI) from your software? Then it’s important to learn about some of the most commonly underused computerized maintenance management system (CMMS) functions. Many organizations do not use all of the features their preventive maintenance software provides, or don’t use the functions to their full capacity. According to a national CMMS survey conducted by Reliable Plant magazine, a majority of plant maintenance managers feel they aren’t using their preventive maintenance software to its maximum capability.
Modern-day CMMS systems are crammed with various features, and users don’t necessarily need to access and master every feature of the system. However, it becomes a problem when users get so comfortable with their way of doing things that they avoid features they’re not familiar with. Especially if those features could potentially improve their productivity. Understanding what impact underutilized CMMS functions can have on your maintenance department will help you make the most of your software.
Most Underutilized CMMS Functions:
Mobile
Mobile options synchronize wireless mobile devices with CMMS systems, allowing maintenance technicians to monitor real-time data and complete a variety of tasks while on the go. Mobile CMMS functions increase your maintenance department’s efficiency and productivity by enabling maintenance technicians who are on the move to enter data, access information about assets and repairs, and create work orders and requests. This helps eliminate paperwork, reduce travel time and increase data accuracy.
Timekeeping
It’s important for maintenance managers to break down the hours employees spend on specific maintenance tasks in order to better understand how maintenance technicians are using their time. The time that a technician spends completing a work order is one of the primary factors that determine the cost of a job.
Preventive Maintenance
Although most organizations use their CMMS systems to schedule preventive maintenance, they often fail to schedule predictive maintenance. People use the terms predictive maintenance and preventive maintenance interchangeably, but they are two very different types of tasks. Preventive maintenance of an asset is based on the passage of a set amount of time, while predictive maintenance refines maintenance tasks to times when they’re functionally necessary. Collecting and analyzing data can help you determine when to perform predictive maintenance tasks.
Web Request System
A web request system allows non-licensed users to submit work requests from any computer with Internet or network access via a simple web form. Allowing customers and employees to make requests online saves you time and minimizes data entry. Users can also opt to receive email notifications to track their requests.
Data Collection
Your CMMS is only as beneficial as the data that it provides. Maintenance managers need good data to make informed decisions. Maintenance technicians play a crucial role in collecting data, and it’s important to provide accurate information when completing work orders. Technicians must take their role in data collection and input seriously in order for maintenance managers to obtain useful data.
Many maintenance departments struggle to make the most of their CMMS systems. It could be the systems they’re using are too complex, or that managers aren’t using the data provided for analysis and decision-making. Perhaps it’s that staff members haven’t undergone the proper training necessary to use all functions. Whatever the case, remember that CMMS software can help you do more with less when implemented properly. In order to realize all advantages, find an experienced CMMS software vendor who will partner with you to ensure success.
Organizations that fail to utilize important CMMS functions and continually improve overall usage are missing out on valuable cost-savings opportunities. DPSI is committed to helping you make the most of your maintenance management software and maximize your ROI. From initial setup to ongoing management, we work closely with your team to ensure you don’t become just another failed CMMS statistic. Contact us today to learn more about our CMMS products and services, or sign up for a free demonstration of our software.
Some surprises here, but I guess its like all of the features on my washing machine!