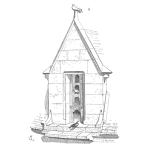
A common first step in the learning journey of a quality engineer is mastering a set of data visualization tools called the “Seven Basic Quality Tools.” Popularized by an architect of the modern quality movement, Karou Ishikawa, the seven basic quality tools allow practitioners to readily extract useful insights from raw data and build a foundation for further statistical analysis. These tools stand as pillars of systematic problem-solving, aiding in the identification, analysis, and improvement of processes.
These seven tools, in order of complexity, are: Check Sheets, Flowcharts, Cause and Effect Diagrams, Histograms, Pareto Diagrams, Scatter Plots, and Control Charts.
Check sheets are simple, yet effective tools for collecting and organizing data. Technicians and inspectors use them to systematically record and tally information, facilitating the identification of patterns and trends. Whether monitoring machine downtime, defects, or any other measurable variable, check sheets offer a structured approach to data collection, providing a solid foundation for further analysis.
Flowcharts provide a visual representation of the steps in a process, helping engineers identify inefficiencies, bottlenecks, and opportunities for improvement. By mapping out the sequence of activities, engineers can streamline processes, reduce waste, and enhance overall efficiency. Flowcharts serve as a valuable communication tool, facilitating a shared understanding of complex processes among team members. Flowcharts also set the stage for more elaborate process mapping tools like Swim Lane Diagrams and Value Stream Maps.
Cause-and-effect diagrams – also eponymously named Ishikawa Diagrams — are powerful tools for identifying and organizing potential causes of a problem. By visually mapping out the factors influencing a specific outcome, engineers can systematically analyze and address the root causes of issues. This tool promotes cross-functional collaboration and helps teams gain a comprehensive understanding of complex problems, fostering effective problem-solving. Cause-and-effect diagrams are also commonly used in conjunction with another problem-solving framework called the “Six M’s”, referring to the six major sources of process variation: Machine. Method, Manpower, Material, Measurement, and Mother Nature.
Histograms are graphical representations of data distributions, offering engineers visual insights into the variability of a process. By displaying data in a bar chart format, histograms reveal the frequency and distribution of specific characteristics, enabling engineers to pinpoint areas for improvement. Engineers can use histograms to identify patterns, outliers, and potential root causes of issues affecting the quality of a product or process.
Based on the so called “80/20 rule”, Pareto analysis and its associated visualization the Pareto diagram, helps problem-solvers identify and prioritize the most critical issues affecting a process. By focusing efforts on the vital few factors that contribute the most to a problem, engineers can maximize the impact of their improvements. This tool aids in decision-making, ensuring that resources are allocated efficiently to address the primary contributors to quality issues.
Scatter diagrams are used to identify relationships between two variables, helping engineers understand the correlation between factors that may impact a process or product quality. By plotting data points on a graph, engineers can visually assess whether changes in one variable correspond to changes in another. This tool aids in identifying potential cause-and-effect relationships and guides targeted interventions for process improvement.
Control charts are instrumental in monitoring and maintaining the stability of a process over time. By plotting data points against predetermined control limits, engineers can distinguish between common cause and special cause variation. This tool enables timely detection of deviations from the norm, allowing for prompt corrective actions to maintain consistent quality levels in processes.
In the intricate world of engineering, the Seven Basic Quality Tools underpin systematic problem-solving and process improvement. By leveraging these tools, engineers can analyze data, identify trends, and make informed decisions to enhance the quality of their products and processes. As technology advances and industries evolve, mastering these foundational tools remains essential for delivering excellence in every facet of quality.Ray Harkins is the General Manager of Lexington Technologies in Lexington, North Carolina. He earned his Master of Science from Rochester Institute of Technology and his Master of Business Administration from Youngstown State University. He also teaches manufacturing and business-related skills such as Reliability Engineering Statistics, Quality Engineering Statistics, and Root Cause Analysis and the 8D Corrective Action Process through the online learning platform, Udemy. He can be reached via LinkedIn at linkedin.com/in/ray-harkins or by email at the.mfg.acad@gmail.com.
Leave a Reply