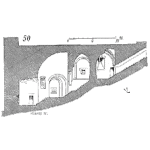
CMMS overview
A proper Computer Maintenance Management System (CMMS) setup can make a world of difference in an organization’s asset management journey. Conversely, a substandard setup can be a living hell for Reliability Engineers like myself and other analysts. This article highlights some practices to avoid in order to gain the most out of your CMMS in the long run. The examples given are based on my own experience in industry. There could be many more learnings out there. Reader comments and suggestions are most welcome as this will benefit the entire Maintenance and Reliability community.
In industry, the CMMS is an indispensable repository of historical records and asset attributes. More and more records are input daily. It is literally the “gold mine” of records and data needed to perform asset related studies. Various stakeholders in the organization will use the output of those studies in order to make the best decisions with regards to the long-term management of their assets. This in turn increases revenue and reduces unnecessary spend. Preventing assets from failing unexpectedly also leads to a safer work environment. Safety remains a paramount value in industry. Everyone coming in to work every day needs to return home healthy.
1 – Lack of cost tracking – to be avoided at all “cost”!
The best CMMS set-ups I experienced in my career were those integrated in an Enterprise Resource Planning (ERP) platform. ERP is a software system that helps organizations automate and manage all internal core business processes. From HR to Finance via Maintenance Management in our case. It coordinates the flow of data between a company’s business processes. In doing so, it provides a single “source of truth” and streamlined operations across the enterprise. What is crucial is its capability to link a company’s financials, supply chain, operations, commerce, reporting, manufacturing, and human resources activities on one platform.
In the case of the CMMS, the asset records such as maintenance tasks completed or spares parts consumed should be connected to a cost or expense module. This in turn, tracks and reports both individual and collective expenses relating to asset maintenance. Cost tracking leads to cost management which in turn leads to cost reduction and data driven decisions. After all, the financial goal of every for-profit entity is to maximize revenues and minimize expenses. This is difficult to achieve when the cost of a task entered in the CMMS is not linked to a cost center. Such as an invoice, cost of labor or expense.
Believe it or not, some companies I have worked for have a CMMS that does not track cost. The CMMS and cost modules use different platforms. They do not communicate with each other. Sometimes, the ERP is first installed in the company without a CMMS module. The CMMS becomes somewhat an after thought, installed in isolation and using different software. This kind of “mishmashed” setup causes tremendous hardship when making financial analysis or budget decisions for assets. Going from one platform to another leads to wasted efforts. This in turn leads to approximations, errors and ultimately lack of confidence in the results. An analyst’s nightmare and a decision maker’s dilemma!
2 – Upgrading the CMMS structure after many years
Sometimes there is an awakening in an organization to start using the CMMS that has been chugging along for a few decades. A revamp is deemed required and changes are planned. A good example of this is the need for standardization of entries leading to structured and streamlined records. Upgrading and seeking improvements is a great initiative in itself. However, one has to be careful with those changes.
Changing the structure of records can lead to discontinuity in the data chronology and alter the integrity of data moving forward. Making it difficult to do a proper analysis. Introducing new records for equipment already running for decades has limited benefits. Except for studies that start from the time of the change. For example, a pump has been running for 25 years with no or very little maintenance records. Maintenance history is to be recorded as of now. The gaps in records will make it difficult not to say impossible to establish life parameters. It would be like jumping on a moving train that has left the station ages ago.
Conversely, when implementing changes in the CMMS, some individuals suggest discarding all the historical data and start from scratch. Especially in the case where the records have not been properly or consistently entered. This is especially common with Information Management and Technology departments who, for good reasons, want to minimize their data storage costs. However, discarding this historical data is a grave error.
Records are records good or bad. Artificial Intelligence technologies such as Machine Learning, can be used to “clean” those records. This in order to “squeeze” out buried yet valuable information. Remember, data is like gold. Sometimes you need to go deep and hard into the rock bed to retrieve it. This digging could eventually be worth the effort. Discarding records might be akin to “throwing away the baby with the bath water”.
In all the above discourse about CMMS structure changes, the best long-term strategy is to get the correct CMMS setup from the start. That is from the early days of an operation. Standards like ISO 14224 can be a great guide for this exercise.
3 – WIIFM for Field Techs entering Maintenance Records
WIIFM is an acronym referring to “What’s In It For Me”. It reflects human nature in essence. Self gain helps to facilitate or make employees respond favorably to an organizational change. Having a CMMS requires employees not only to enter records or maintenance history but above all enter them correctly. Implementing a new CMMS platform very often comes with user training. This is essential as it helps the people who input the data understand and use the system as required.
However, what is often missing is the explanation as to why this information is important. Or, how it will benefit those same data inputters such as maintenance technicians. It is crucial to explain the “WIIFM” to those who take time from their busy schedules to enter historical records yet feel no one will use those. In practical terms, data analysts like myself should build case studies based on the entered records and showcase the benefits of those to employees. In plain language the message is:
“When you enter data correctly in the CMMS, this is what I can do with it so that we can develop an effective maintenance strategy together. For you field workers, this reduces unplanned failures. You see less safety excursions. Overall there is less firefighting and stress in your job.”
The WIIFM benefits can also be enhanced by having the following CMMS implementation approaches:
- Ensure that the CMMS actually works for users rather than having them work for it. Don’t make entering records complicated and cumbersome for people who are busy and generally abhor administrative tasks. For example, avoid dropdowns with more than 10 selections. Or provide technicians with hand-held devices which eliminate trips to an office computer.
- Take user feedback seriously. New systems are likely to have flaws and bugs. It is important to make users part of the solution rather than having it imposed on them.
Leave a Reply