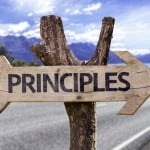
Getting to the Root of the Matter
Does a cause description need to be a design or manufacturing deficiency? Why? This is one of the more important questions to consider if you want to achieve quality FMEAs.
“The effort to get at the truth has to precede all other efforts.”
Albert Einstein
Definition of “Cause”
The Oxford English dictionary defines “cause ” as “a thing that gives rise to an action, phenomenon or condition.”
What is the definition of “Cause” in an FMEA?
A “cause” is the specific reason for the failure, preferably found by asking “why” until the root cause is determined. For Design FMEAs, the cause is the design deficiency that results in the failure mode. For Process FMEAs, the cause is the manufacturing or assembly deficiency (or source of variation) that results in the failure mode.
How are Causes identified in FMEAs?
The FMEA team considers each failure mode, and determines the underlying reason for the failure mode. There can be one or more causes, and the team should identify as many causes as are needed to document their concerns. Causes should be described in sufficient detail to establish the underlying reasons for the cause, often called the “root” cause. The only exception to this is for higher levels of analysis, such as System FMEAs, in which the cause may remain at a higher level, such as a component failure, and not carried all the way down to the reason for the component failure. For high-risk issues, the FMEA team can recommend a lower-level FMEA to drill down to root cause. It is vital to understand the primary reasons for the failure. It is often useful to use the phrase “due to” to help get the root cause. For example, in the case of the projector lamp shattering, a possible cause could be “over pressure due to wrong gas.”
In Design FMEAs, root causes are often described in terms of product characteristics, such as dimensions, weight, orientation, hardness, strength, etc. The design deficiency relates to the product characteristic, such as “material too soft.” In Process FMEAs, root causes are often described in terms of process characteristics, such as oven temperature, tool wear, part position, weld-device current, pressure, flow rate, etc. The manufacturing deficiency relates to the process characteristic, such as “insufficient or intermittent weld-device current.”
What is an example of a Design FMEA cause?
Item: Power steering pump
Function: Delivers hydraulic power for steering by transforming oil pressure at inlet (xx psi) into higher oil pressure at outlet ([yy] psi) during engine idle speed
Failure Mode: Inadequate outlet pressure (less than [yy] psi)
Effect (Local: Pump): Low pressure fluid goes to steering gear
Effect (Next level: Steering Subsystem): Increased friction at steering gear
Effect (End user): Increased steering effort with potential accident during steering maneuvers
Cause: Fluid incorrectly specified (viscosity too low)
Poorly worded example of Cause: Outlet pressure too low
What is an example of a Process FMEA cause?
Process Step: Induction harden shafts using induction hardening machine
Function: Induction harden shafts using induction-hardening machine ABC, with minimum hardness Brinell Hardness Number (BHN) “X”, according to specification #123.
Failure Mode: Shaft hardness less than BHN “X”
Effect (In plant): 100% scrap
Effect (End user): Potential shaft fracture with complete loss of performance
Cause: Induction machine electrical voltage/current settings incorrect for part number
Poorly worded example of Cause: Operator error
Application Tip
It is impossible to overstress the importance of fully analyzing and understanding the cause. A half-analyzed cause has little value, as the cause is the heart and soul of the FMEA. Take the example of a projector lamp shattering. If the FMEA team simply describes the cause as “over pressure” and does not ask why the over pressure, the root cause of “wrong gas” is not established. The team will end up trying to solve “over pressure,” and may miss recommending the correct gas specification. The problem will not be solved. It is often useful to use the phrase “due to” to help get the root cause. For example, in the case of the projector lamp shattering, a possible cause could be “over pressure due to wrong gas.”
Many practitioners use repeated questioning of the FMEA team to ensure that the basic “why” is determined as the cause of a failure mode. This technique, called the Five Whys, can be very helpful, especially when the root cause is not forthcoming. The Five Whys is a technique developed by Taiichi Ohno, originator of the Toyota Production System. It means that by asking “why” five times, the team will be able to discover the progression of cause-and-effect relationships behind a problem and the root cause that is below the surface.
Next Article
The next article presents beginner, intermediate and advanced problems relating to FMEA causes, along with solutions. One of the problems poses a realistic and especially challenging circumstance that FMEA teams can experience.
Leave a Reply