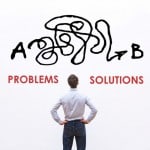
Problems and Solutions
The DC-10 case study continues by asking for causes to the door latch-pin failure. The advanced problem poses a realistic and especially challenging circumstance that FMEA teams can experience.
“Judge a man by his questions, not his answers.” Voltaire
If you haven’t yet read the article “Understanding FMEA Causes – Part 1“, this would be a good time, as it presents fundamental information about the causes of failure in an FMEA.
Beginner’s Problem
In an FMEA, which of the following is true about a “cause”? (Select all that apply)
1. A “cause” is the specific reason for the failure.
2. A “cause” is the potential consequence or impact of the failure to the system or end user.
3. There is always one cause for every failure mode.
4. If a cause occurs, the corresponding failure mode occurs.
Beginner’s Solution
In an FMEA, which of the following is true about a “cause”? (Select all that apply)
1. A “cause” is the specific reason for the failure.
(True)
2. A “cause” is the potential consequence or impact of the failure to the system or end user.
(False. The potential consequence or impact of the failure to the system or end user describes an “effect.”)
3. There is always one cause for every failure mode.
(False. There may be many causes for each failure mode.)
4. If a cause occurs, the corresponding failure mode occurs.
(True)
Intermediate Problem
[The intermediate problem repeats the same scenario from previous months. This month, readers will be asked to continue the analysis by the identification of a cause.]
Scenario: On June 12, 1972 an American Airlines DC-10 aircraft lost its aft cargo door soon after taking off from Detroit. We’ll use this incident to practice identifying the elements of an FMEA. Here is the background to the FMEA problem.
McDonnell Douglas learned from cabin pressure testing that an improperly closed cargo door could burst open due to loss of cabin pressure, potentially resulting in the floor of the passenger compartment crashing down into the cargo compartment. The temporary solution was to put a vent flap in the door that would close by the same linkage that shut the cargo door, which would keep the airliner from holding pressure unless the cargo door was safely latched, thereby alerting the pilot to the problem. However, a bit of excessive force by a baggage handler shutting the door could make the vent flap close even though the cargo door was not fully latched.
The DC-10 with the cargo door vent flap was put back in service. On a brief layover before the Flight 96 leg to Detroit, a cargo handler had trouble shutting the rear cargo door, but managed to get it shut with a little extra force. Since the door-latch signaled “closed,” the warning light in the cockpit did not show a problem. However, the force the cargo handler used to shut the door bent a metal linkage on the inside of the door, preventing it from closing properly. The air pressure during ascent generated too much force on the bent door linkage. It sheared off the pins, releasing the door. The cabin near the door collapsed and jammed the control cables to the tail. The rest is tragic history.
The probable failure sequence of the DC-10 cargo door is:
* Airline cargo handler uses extra force to close rear door, bending door pin. Door does not securely close.
* The door vent flap does not trigger the electronic alarm, and the pilot is not notified the cargo door failed to lock securely.
* The air pressure outside the cargo door drops during ascent, until pressure on the door from the inside causes the door-latch pin to shear. The cargo door blows out.
* High-pressure air inside the cabin collapses the floor, resulting in hydraulic lines and cables becoming non-functional.
We’ll use the door latch-pin failure on DC cargo door latching subsystem as an example to practice identifying functions, failure modes, effects, causes and controls, based on the cargo door latch-pin failure history.
In previous months, we focused on one possible function, one possible failure mode for the identified function and one possible effect for the identified failure. The answer for the function of the door latch-pin was something similar to “fully secure the cargo door in the closed position during all operating loads and environmental conditions without allowing the door to close unless fully latched;” for the failure mode, it was something similar to “door latch pin bends under maximum stress loading,” and for the effect of the failure it was something similar to “bent latch pin allows the door to appear to be closed when it is not fully secure, thus failing to abort airplane takeoff, potentially creating a pressure differential between inside and outside air, with the possibility of catastrophic cargo door blowout during flight.”
This month we’ll focus on a cause for the failure of the door latch-pin of the DC-10 cargo door. We’ll continue this exercise in the next several months as we focus on the proper identification of controls and recommended actions.
Problem: Use the door latch-pin failure of the DC-10 cargo door latching subsystem as an example to identify one possible cause for the identified failure mode “Door latch pin bends under maximum stress loading.”
Intermediate Solution
For the cause, your answer should be something like “Door latch pin bends under extreme loads due to inadequate pin diameter” or “Specification of pin material has inadequate hardness.”
Advanced Problem
Scenario: A Process FMEA is being performed on an optical prism, which is part of a precision laser system. The prism glass surfaces must be very smooth in order to accurately reflect and redirect light for laser applications. When the Process FMEA was nearing completion, the FMEA facilitator asked the FMEA team if there were any concerns that had not been brought forward or addressed. One of the team members said there was a concern. However, in their entire prism manufacturing history, there had never been a workable solution to this problem; therefore, it would be a waste of time to bring it up in the FMEA. The facilitator asked about the concern, and the team member said it had to do with gas bubbles in the prism glass. He said that no one understands why these bubbles occur, and they will occur from time to time in the manufacturing process. The entire team concurred that this problem will occur at a moderate frequency and when it does, the prism surface cannot be smoothed properly and the laser system performance will be degraded. However, since it has no solution, putting it in the FMEA would only waste the time of the FMEA team and management. The FMEA facilitator considered different options, including leaving the gas bubble concern out of the Process FMEA, or entering it without a cause. There may be other options the facilitator should consider.
Problem: In your opinion, what should the FMEA facilitator do and why? Write down your answer and compare to the following.
Advanced Solution
There are times when the cause of a problem is not immediately available to the FMEA team. When this happens, the FMEA facilitator should recognize this fact, and avoid the temptation to skip over the problem or enter ineffective solutions in the FMEA. This takes excellent facilitation skills and willingness to face difficult choices.
Summarizing the problem, the FMEA team believed gas bubbles would occur with moderate frequency; and when they did occur, the performance of the laser system would be degraded. Leaving this concern out of the Process FMEA is not a good option. It is always best to factually, and without emotion, include the concerns of the FMEA team, along with recommendations for addressing the most serious concerns. However, in this case, the FMEA team did not know the reason for the problem. The FMEA facilitator and team can do the following: The gas bubble concern can be entered as a failure mode. The cause of failure can be temporarily noted as “unknown.” The team can use the Recommended Actions column to brainstorm actions to identify the cause of the problem. If the team does not know what to do, the FMEA facilitator should encourage the team to identify specific steps to analyze the cause of the problem. Possibly new laboratory equipment is needed to analyze the nature of the gas bubbles. Possibly a review of academic research literature into the gas bubble problem would be helpful. Possibly one or two new FMEA team members need to be added, who have skills and experience with the problem. The FMEA team should enter the steps that are needed to get to the root cause of the problem, and bring the gas bubble problem and the recommended steps to the attention of management in order to obtain support for root cause analysis. Once the root cause is identified, the cause of the problem should be entered in the FMEA and new recommendations should be added to the FMEA to reduce the risk associated with the problem to an acceptable level.
Next Article
Is it a good idea to do one generic FMEA for harnesses and use it as a reference for other FMEAs for similar applications? This question is answered in the next article, along with practical advice on how to apply generic FMEAs.
Leave a Reply